
Williams Advanced Engineering is the technology and engineering services business of the Williams Group. It specialises in advanced lightweight materials, hybrid power systems and electronics, aerodynamics, vehicle dynamics, and holistic integration capabilities. We caught up with company executives to learn more about its latest projects, advances in hybrid battery systems, electric vehicles and lightweight solutions.
Could you explain a little more about Williams Advanced Engineering (WAE) and the type of projects you are working?
Williams Advanced Engineering Limited is the technology and engineering services business of the Williams Group. The company combines cutting-edge technology and the industry's best engineers, with precision and speed to market derived from four decades of success in the ultra-competitive environment of Formula One.
Working in close collaboration with its customers across industry, Williams Advanced Engineering helps meet the sustainability challenges of the 21st century and improve performance, with its expertise in aero and thermodynamics, electrification, advanced lightweight materials and vehicle integration.
The genesis for the diversification of Williams started with the hybridisation of Formula One in 2008. Williams was the only team to develop hybrid systems entirely in-house, creating both battery and flywheel equivalents. However, it is technically possible to trace the origins of Williams Advanced Engineering back even further, as Williams has been completing projects outside of Formula One on an ad hoc basis since the 1980s with projects such as the Metro 6R4 rally car, Renault British Touring Car Championship entry and the BMW Le Mans 24 hours car.
Realising the commercial potential of the hybrid technology developed for the Formula One car, Williams entered the commercial world by creating a business called Williams Hybrid Power to take the flywheel technology into other industries, such as public transport. This business was sold to GKN in 2014.
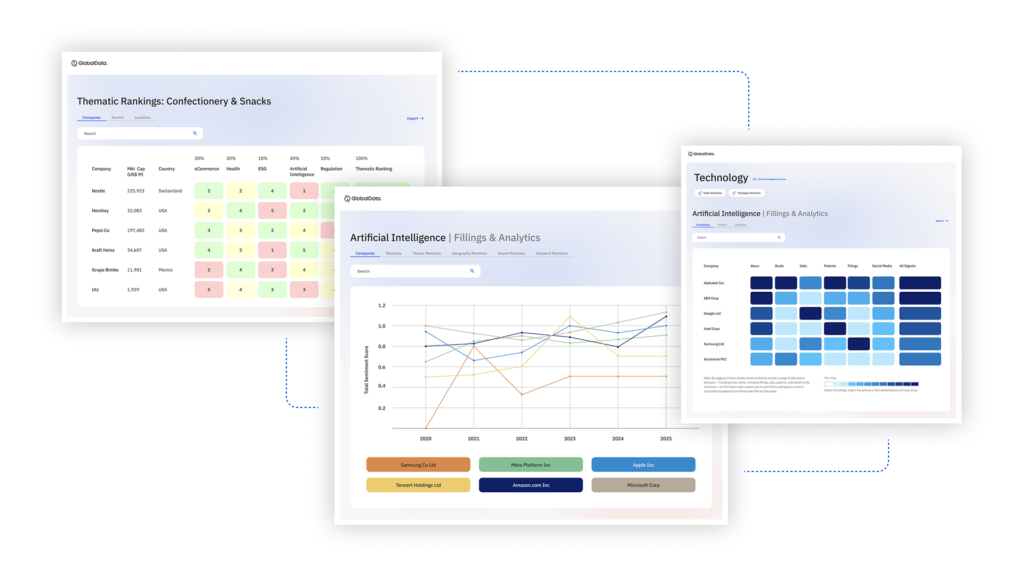
US Tariffs are shifting - will you react or anticipate?
Don’t let policy changes catch you off guard. Stay proactive with real-time data and expert analysis.
By GlobalDataWith expertise in hybrid propulsion systems growing, Williams was approached by Jaguar Land Rover in 2010 to help in the creation of their C-X75 hybrid supercar.
With the C-X75 project in 2010, Williams decided to create an umbrella brand to house all of our projects outside of Formula One. This was the birth of Williams Advanced Engineering.
Williams Advanced Engineering has grown exponentially since its creation in 2010. It opened a dedicated new facility in 2014 and has now completed over 80 projects, with over 40 current projects in a range of sectors for more than 20 customers. There are now more than 250 employees in Williams Advanced Engineering.
In what ways is WAE pushing back the technical boundaries of batteries for electric vehicles?
In 2009 Formula One regulation changes allowed teams to store and reuse energy for the first time.
Williams has developed high power density batteries and electric motors for a range of applications and market sectors.
Since then, Williams has developed world-leading expertise in both flywheel and battery Kinetic Energy Recovery Systems (KERS) for automotive, motorsport, public transport and energy applications. Williams has developed high power density batteries and electric motors for a range of applications and market sectors where high performance, endurance and predictability are key customer requirements. We have expertise in the design and manufacture of the battery, motor generator unit, inverter and battery management system. But what really sets us apart is our ability to get these components to work together in unison.
We understand that the UK Government's Faraday Battery Challenge has chosen a consortium led by WAE to develop further innovative lithium-ion battery systems for vehicles …
Yes, it's true that earlier this year the UK Government's Faraday Battery Challenge chose a consortium led by Williams Advanced Engineering to develop further innovative lithium-ion battery systems for vehicles. The consortium, with Imperial College London, Zap & Go, PowerOasis and Codeplay, seeks to research and deliver higher power, higher energy batteries using fewer cells that last longer and charge more quickly than today's technology. Such higher power, lighter, longer life batteries that charge more quickly would deliver greater range for electric vehicles, a key challenge for future sustainable mobility.
The project will deliver a hybrid battery system, setting global standards for the future of such products and seeking to extend the UK's leadership in electric vehicles. A study has already shown that hybrid batteries can deliver higher power and energy in a lighter product than lithium-ion alone.
Williams Advanced Engineering has powered the entire ABB FIA Formula E grid since its inception and was also chosen by the FIA (Fédération Internationale de l'Automobile) earlier this year to be the sole battery supplier in the electrification of the FIA World Rallycross Championship from 2020. The company was honoured with a Queen's Award for Enterprise in Innovation in April 2018 for its commercialisation of electrification know-how from its experience in Formula E.
From the very first race in Beijing, China in 2014, the batteries have proven their worth. A major collision during the race demonstrated the safety of the batteries and there have been only two ontrack battery failures in all the races. There has been no on-track battery failure since mid-way through season two, 30 races ago.
The equivalent of more than 1,100 Formula E cars have travelled more than 240,000 miles – the equivalent of a trip from the Earth to the Moon – powered by the Williams Advanced Engineering batteries. The batteries have powered the equivalent of a journey of more than one and a half times around the world in race conditions since the last battery failure on track.
Could you tell us a little more about your EV concept and how does it inform the next generation of FCEVs?
Williams Advanced Engineering has reimagined how electric cars are designed and constructed.
With the car industry currently focussed on how it transitions from the internal combustion engine to a fully electric future, a major challenge for manufacturers is how to maximise vehicle efficiency, given current limitations. Responding to this challenge, Williams Advanced Engineering has reimagined how electric cars are designed and constructed. This new approach is designed to make EVs lighter, safer and greener, with longer range and better performance.
The concept features several innovations in battery pack design, cooling systems and lightweight structures, which have each been cleverly integrated into a single, scalable platform. For instance, Williams' engineers have developed a highly automated, near zero waste process that is being implemented to create fibre reinforced suspension components on the EV platform, providing up to 40% weight reduction over a conventional aluminium wishbone.
Another innovation being showcased is the process of forming high-strength 3D structures from 2D materials which, in this instance, has created an exoskeleton for a battery module that also contributes to the structural performance of the battery.
Developed by in-house specialists in aerodynamics, electric systems, advanced lightweight structures and vehicle integration, the concept highlights Williams Advanced Engineering's expertise in accelerating ground-up innovations into demonstrable products available to its customers.
Vehicle efficiency has always been core to Williams – whether it be in Formula One or with Williams Advanced Engineering's customer projects. These technologies, and thinking around how to create a tightly integrated, light-weight chassis and powertrain package, have the potential to greatly increase the competitiveness of the next generation of electric vehicles. By making EVs more attractive to consumers, we can help accelerate their adoption and the air quality benefits they bring.
The FW-EVX represents a new direction for the business, as our own R&D team has developed the proprietary innovations and has submitted patents for a number of the inventions. We believe there is a high potential business opportunity here, and are excited to see where this could take us.
For some time, carbon fibre has been used in F1, aerospace and marine applications and appears to be making its way into vehicle manufacture. Where do you see the greatest opportunities/applications for carbon fibre in mass-produced cars?
Currently, the greatest uses for carbon fibre are in the high strength/stress areas, where the benefits overcome the associated cost penalty.
Currently, the greatest uses for carbon fibre are in the high strength/stress areas, where the benefits overcome the associated cost penalty. This translates into a number of specific areas of the vehicle, which leaves the challenge of combining these materials to work as a system. There is currently very little convergence in the automotive industry as to the best overall solution and it will invariably come down to a multi-material, multi-process solution.
What other trends are you seeing with respect to lightweighting using composites in vehicle manufacture?
At Williams Advanced Engineering we are developing our own patent pending composite processing technologies, 223™ and RACETRAK™, that are aimed at high volume, low-cost applications across sectors but particularly pertinent to automotive. We are developing these in response to the challenges our clients face in the road to electrification and the increased pressure on reducing the weight of the structure to counteract the weight of the batteries. As these are material processing technologies the benefits are as powerful outside of the auto sector and we are seeing increased interest from aerospace and wind energy too.
Can you envisage cheaper, easier-to-form alternatives to carbon fibre?
Carbon fibres, like metals, come in different grades and specifications and there is research ongoing around the more 'industrial' carbon fibres as well as in reducing the energy consumption in the manufacturing of the fibres – along with embedded CO2.
In terms of the use of magnesium in vehicle manufacture, what do you see happening there?
The benefits [of magnesium] are there if you wish to pay for them.
The specific strength/stiffness of metals is roughly comparable, i.e. the strength/stiffness per unit weight comes out roughly the same. Magnesium has a density of 1.6 g.cc-1, compared to 2.8 g.cc-1 for aluminium and 7.8 g.cc-1 for steel. The difficulty for magnesium is that the cost per MPa (unit of strength) is much higher for magnesium than aluminium or steel. The benefits are there if you wish to pay for them, and indeed there are opportunities for higher adoption of magnesium in vehicles as there is more pressure on the vehicle mass with electrification, but this also true for composite materials.