
Commercial vehicle exhaust systems are facing multiple challenges. Ever tighter engine emission requirements demand ever more efficient DPF and catalyst performance and this, in turn, requires ever more effective heat management. These systems have necessarily increased in size putting more pressure on overall packaging, with hot exhaust system components encroaching on systems that could potentially be damaged by heat. There is also a desire to keep heat in the exhaust to maintain turbocharger efficiency and response. Continuing just-auto/QUBE’s series of interviews, we spoke to heat management specialist Zircotec’s Group Sales Director, Graeme Barette, about some novel approaches that could address both issues.
How big is the challenge facing future commercial vehicle exhausts?
I think we have an unprecedented combination in which internal temperatures are being increased in order to improve emissions performance ahead of tighter future standards. At the same time, external temperatures have to be reduced to meet packaging needs and to meet safety legislation, recognising that hot surfaces create a fire risk; and exhausts are more exposed to pedestrians and drivers on commercial vehicles.
The scale of the problem is huge: internal temperatures in some cases will rise from 500 degC to as much as 700 degC, while the maximum external temperature, currently as high as 480 degC, could be mandated down to just 70 degC. Finding a cost-effective way to meet these targets has become paramount for commercial vehicle manufacturers.
Why can’t vehicle manufacturers just insulate the exhausts?
Heat management is easy if the only requirement is to reduce heat loss and you have enough space to install sufficient insulation. Unfortunately, space is a luxury that vehicle manufacturers simply don’t have, not even on commercial vehicles. Conventional insulation would typically need to be up to 70mm thick to achieve the thermal barrier performance required. There just isn’t the room for such a thickness in many applications, without re-routing the exhaust line and introducing knock-on effects that compromise other systems and overall packaging, to say nothing of the cost involved. Additionally, heat management now needs to be far more subtle and controlled to reduce warm-up times and ensure heat is delivered to key systems. We are approaching the point where there is only just enough high-grade heat in the exhaust gas to drive these systems, so a different approach is required.
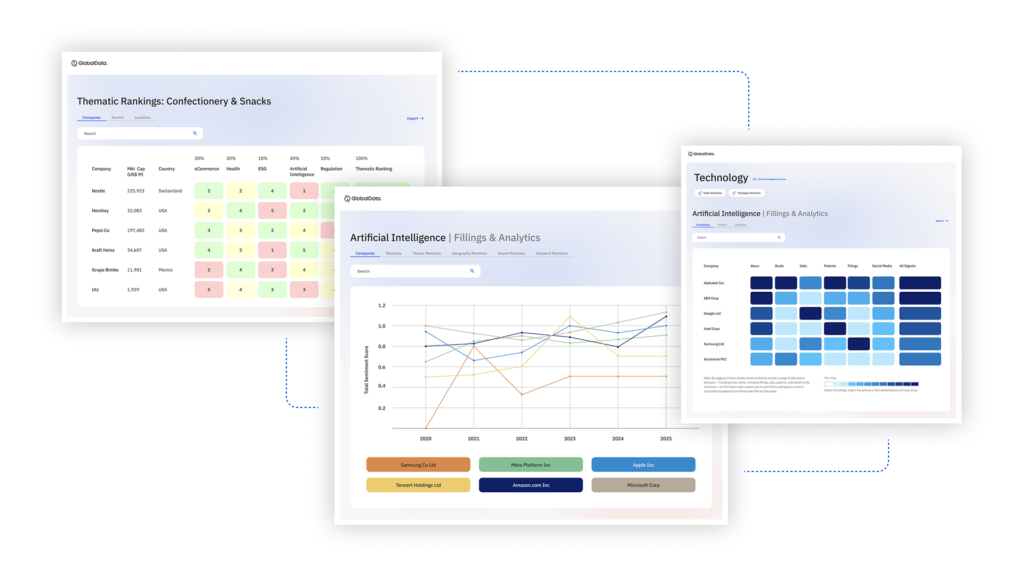
US Tariffs are shifting - will you react or anticipate?
Don’t let policy changes catch you off guard. Stay proactive with real-time data and expert analysis.
By GlobalDataSo what kind of approach is being taken?
There is no single ‘magic bullet’; we are developing a number of new and innovative approaches to suit each customer’s requirements. For example, one of our clients is aiming to maintain the exit gas temperature at no less than 87 percent of the temperature at which it leaves the engine (for efficiency reasons). To achieve this we have to analyse each individual component of the exhaust system.
We are looking at ways of reducing temperatures within the structure of the exhaust, including the exhaust manifold, thereby reducing heat transfer from the hot exhaust gas to the outer containment. This will help maintain exhaust gas temperatures and will potentially have a significant impact on cold-start and the time taken for systems to warm-up. It should also reduce the operating temperature of the containment structure, putting less demand on material choice. Even the metal exhaust clamps holding the system together can be a major source of heat loss; so we are working with a leading clamp supplier on ceramic coating options to reduce this effect.
Another key focus is on the after-treatment systems and thermal management in these areas to significantly improve clean-up efficiency. Our technology can be used inside and around the DPF and catalyst to increase the internal gas temperature and ensure heat is delivered and focussed where it is needed, whilst simultaneously reducing external heat transmission through improved thermal barrier performance. We are working with another of our customers on the insulated of a modular catalyst unit.
How can you overcome the packaging problems associated with thermal insulation?
We are investigating the use of our ThermoHold® based heat shield material with and without an integral conventional metal heat shield. By incorporating integral air gaps we have systems that can operate in different environments and orientations to improve thermal barrier performance. These heat shields can deliver significant heat protection, providing a highly cost-effective way to meet packaging requirements.
What about the exhaust manifold itself? What can be done to improve its thermal performance?
We are currently undertaking a vast research and development project alongside a major vehicle manufacturer and exhaust component suppliers. We are not at liberty to provide details, but two very different approaches are being considered by Zircotec, the aim being to include a ThermoHold® based heat shield inside the exhaust manifold. Prototypes have been produced with the Zircotec ceramic based material used and applied by the manifold supplier at their facilities. Early trials and the associated test results are very promising.
Is this challenge affecting the passenger car market, too?
Yes, to some extent. Again, the drive for efficiency is increasing exhaust temperatures and this is inevitability having a knock-on effect on the rest of the system and the components surrounding it. To add to this, space and packaging can be even more of an issue for passenger cars. Even so, we are seeing the largest demand coming from the commercial vehicle world.
Currently, the biggest part of our business on the passenger vehicle side is for coated manifolds; turbochargers; exhaust finishers; and coated motorbike exhausts. The initial drive was to manage heat and protect vulnerable components and surfaces near to the exhaust, but our coatings have increasingly become part of the vehicle styling and are being used for vehicle aesthetics in areas where resistance to salt water corrosion, abrasion, stone-chipping, sunlight and heat are more important. Our coatings have been proven to perform well and continue to look good in such environments, and are now being used for improved aesthetics by a number of vehicle manufacturers. In fact, we recently announced the company’s biggest contract, worth £1m, to supply a premium European supercar manufacturer with our coating.