
Designed as an environmentally friendly, carbon reduction showcase vehicle, the Renault Emblème has taken on the challenge of not only reducing its carbon emissions, but also to be able to be recycled once its time is up.
The Emblème sports a dual-energy electric and hydrogen powertrain, which aims to reduce CO2 emissions over its lifecycle, with the goal use case of battery for everyday use, and hydrogen for longer journeys.
Renault has stated that the Emblème aims to achieve unprecedented levels of decarbonisation throughout its lifecycle by using recycled, low-carbon, natural materials, manufacturing with 100% renewable energy, while promoting the widespread adoption of second-life and circular economy practices.
At a recent launch event hosted by Renault in Paris, Frankie Youd heard from: Pascal Tribotte, project manager, Renault Group; Ghislain Picard, electricity and electronics architect and Renault Emblème sound system expert; François Farion, design director, innovation and sustainability, Renault Emblème design & materials expert and Matthieu Lemonnier, vehicle architect, Renault Emblème expert.
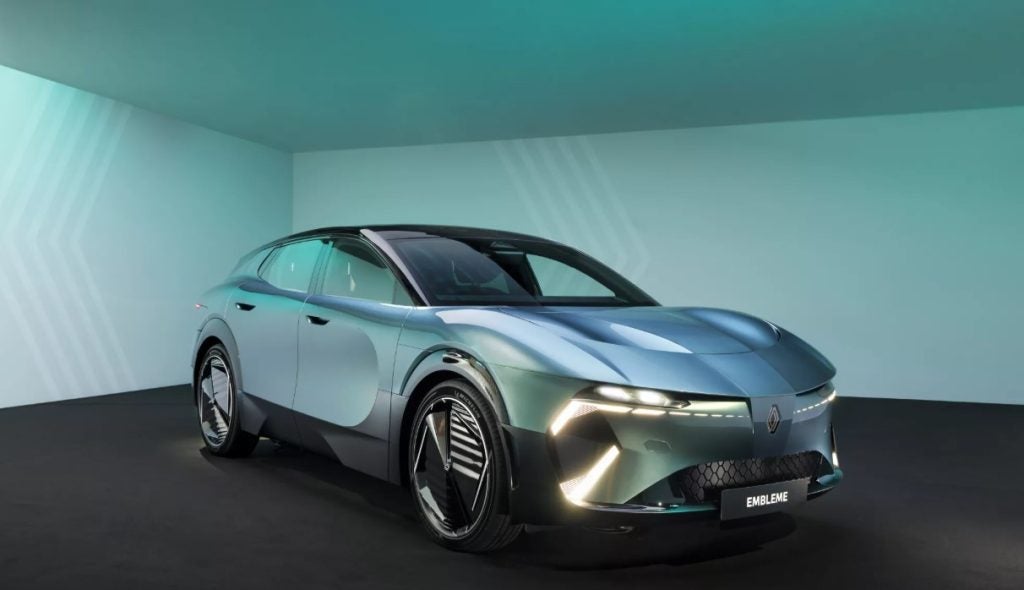
Just Auto (JA): What is the goal behind the Renault Emblème project?
Pascal Tribotte (PT): Our goal is to be carbon neutral by 2050; one step we are taking to achieve this is we will reduce our factory carbon footprint by 62.5%.
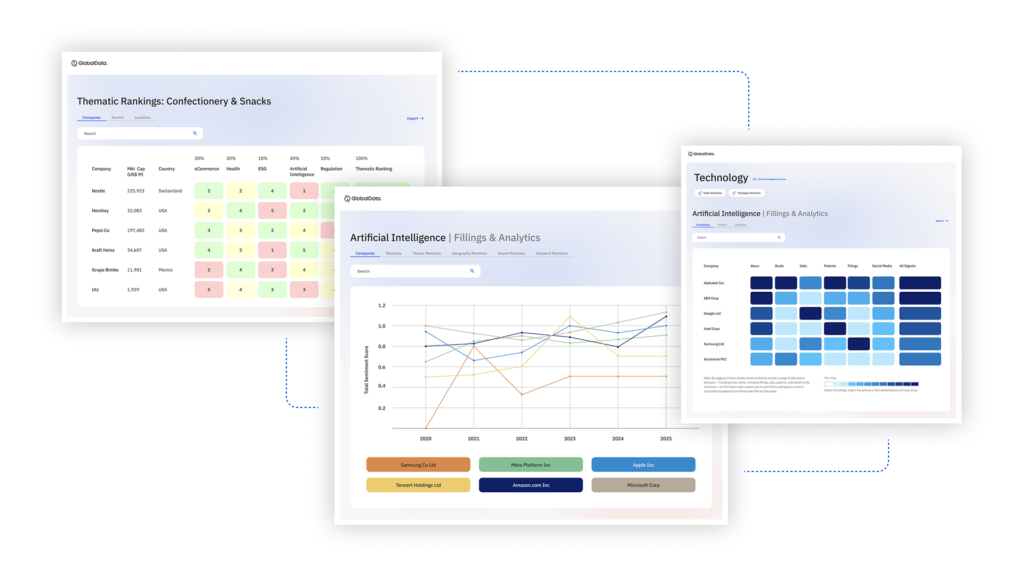
US Tariffs are shifting - will you react or anticipate?
Don’t let policy changes catch you off guard. Stay proactive with real-time data and expert analysis.
By GlobalDataWhen we speak about CO2 emissions, or CO2 equivalent emissions, it’s on the full lifecycle of the vehicle. We try to consider everything from cradle to grave.
The design or conception phase is very important, because we decide which kind of car we will make, if it’s electric or something else. We have the ‘use phase’, and the ‘end-of-life phase’ because when the vehicle is at the end of its life we need to recycle as much as we can and have as little as possible ending up in landfill.
The weight is important for a net zero car. Each kilogram of material has a carbon footprint, so with one more kilogram of material, the energy consumption of the car will be higher. Efficiency is very important.
We also decided for this project that we wanted a real car, with full recycling for net zero. This is why we created the project. It was designed in 2019. When we started, we had absolutely no clue about what was the right formula for net zero. In the first discussion the image that many people in the group had about the net zero car was a small car, or a very simple car, where we removed technology, where we removed the screens – so we decide to explore more.
We decided, after a while, not to compromise Renault DNA. We wanted this car to be fully enjoyable and have a lot of technology inside. We decided it must be a big car, a family car, which will allow you to do everything you do now; it’s a family car for daily use.
Could you discuss the thinking behind the powertrain set-up for the vehicle?
PT: There is hydrogen, because it makes sense for decarbonation. For a net zero car, there are only two ways to store energy: an EV battery, or a hydrogen tank and fuel-cell.
For everyday life, you would use the 40-kilowatt hour battery. The range of the battery is 200 kilometres on the motorway, and 300 kilometres for normal use around the city. For long trips, you can use a fuel-cell, and the fuel-cell will allow (with a full tank and the full battery) on the motorway around 500 kilometres. If you allow for one refuel it will be around 800 kilometres, and with two refuels it will be more than 1,000 kilometres.
For the energy management we did a full model of the car, utilising a digital twin, which comprised a new model of the hardware and all the software, in order to test a lot of solutions, and to refine all the algorithms in order to lower the energy consumption.
Could you explain the design of the vehicle?
François Farion (FF): This is a real vehicle; the prototype systems are up and running. We will start with the front face including active elements of the air inlet, which has two vents that extend behind the wheels, guiding air along the front doors – this allows for aerodynamics to be improved.
We have worked hard to make sure we have the best air passage between the bumper and the hood. It has a statutory front face, statutory bumper, to include the display logo and also the integration of the headlamps.
For the hood, it has automatic opening, which is very simple and easy to use for the customer, and we have 74 litres in this space.
On the side of the vehicle, we chose to use cameras for vision instead of mirrors for peripheral vision. The impact with this flush integration means we reduce the number of parts, and we reduce the blind spots.
We worked a lot on the wheels with our partners for the efficiency of the tyres and to achieve light-weighting.
We have also worked on an innovative door which is completely flush, more simplified than we usually do. We have a switch that opens the door very easily. With this simple design, we dramatically reduce the number of components.
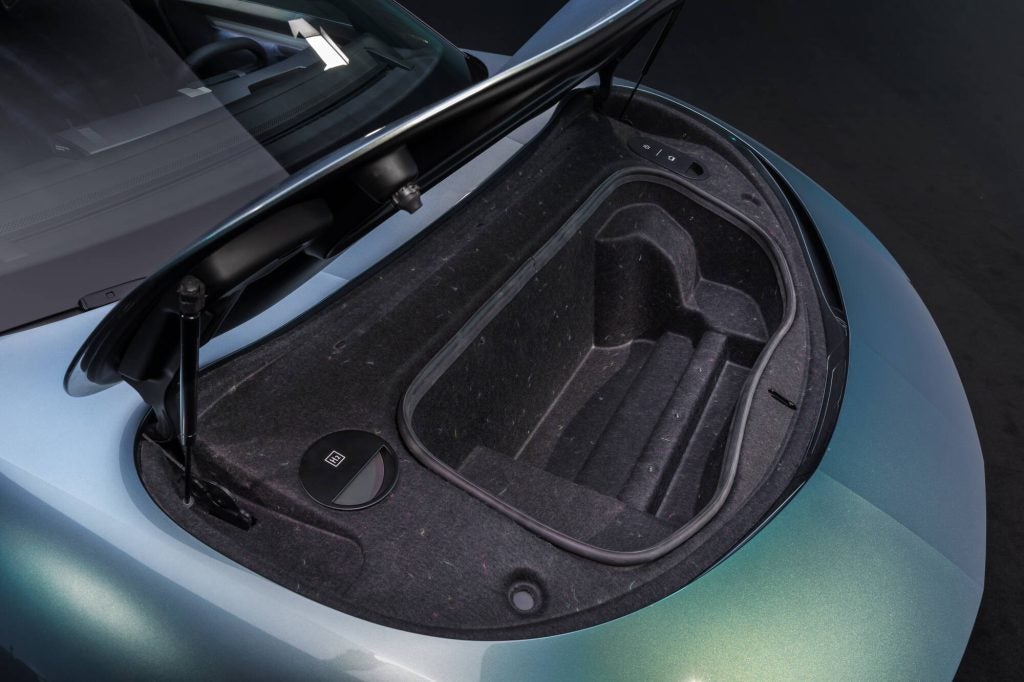
Could you discuss the recycled materials which are used on the vehicle’s exterior?
Matthieu Lemonnier (ML): The vehicle is low-iron and this is very important for the efficiency. For us to reach the carbon footprint goal in terms of the materials, we start with steel. Steel is about 70% of the weight of the vehicle, so it’s very important to work with that.
If we have stronger, thinner steel, we can reduce the weight of the steel sheet metal that we are using. That’s one area to improve. The second one is to change the way we make the steel. There is, of course, a possibility to make steel with gas and a blast furnace like we always do, but this is very carbon intensive. It’s about 2.3 kilogram of carbon for one kilogram of steel. If you do it with an electric arc furnace and you do it with green electricity, then you can go as low as 0.9 kilogram per kilogram of steel.
If we have stronger, thinner steel, we can reduce the weight of the steel sheet metal that we are using.
You can also include much more recycled steel inside. With a blast furnace, you can do 20% recycled inside, but with an electric furnace, you can go to 80% recycled inside. It means that you can dramatically reduce the carbon footprint, and again, this is on 70% of the weight of the vehicle.
We also wanted to have a lighter vehicle so the four doors and the hood are also aluminium. Aluminium is lighter, of course, than steel. We have a structure that performs on side impact and the structural elements required, but is also lighter than what we do today.
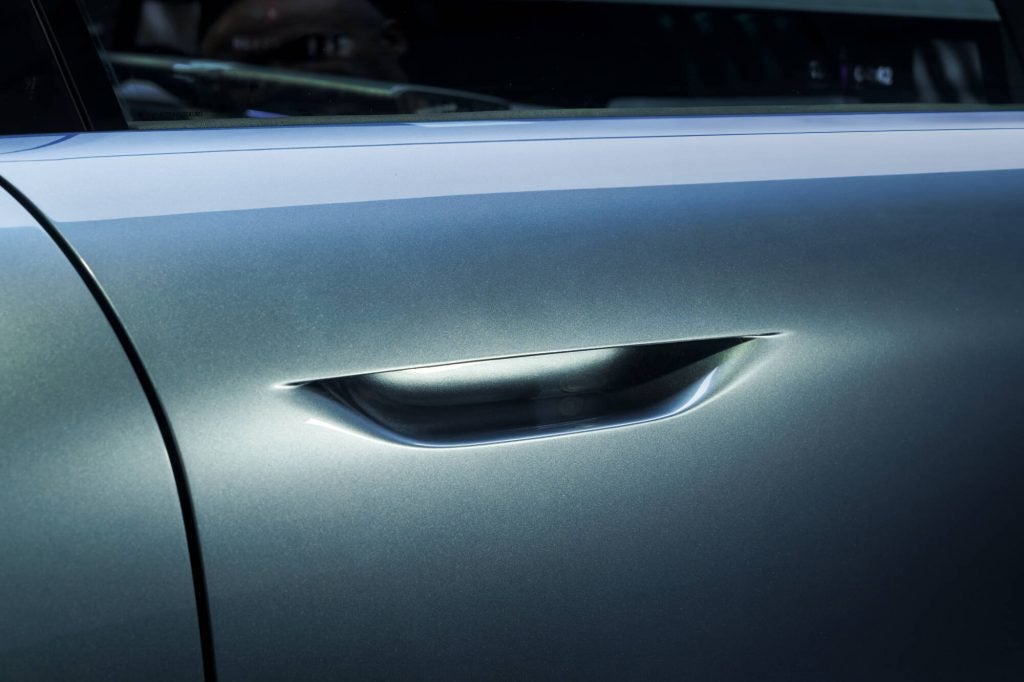
We also use recycled aluminium for this. This is important, because aluminium has a higher carbon footprint than steel. Typically, it’s around 10 kilograms of carbon per kilogram of aluminium. By using recycled aluminium, you can go down to one kilogram. It means that you divide by ten the carbon footprint on aluminium by using recycled aluminium.
The good news with aluminium is that there is no difference whatsoever in terms of performance between recycled aluminium and regular aluminium. This is what we use on the doors, but this is also what we use on the wheels.
The wheels are 22 inches. We use a 22-inch wheel to balance the whole body. This is a big car, it is a little bit narrower than usual, and this 22-inch wheel is only 16 kilograms, which is quite low for such a big wheel. Why? Because we stripped down everything we don’t need. You don’t see the wheel, what you see is the cover of the wheel. The cover of a wheel is also made with recycled plastic, 30% recycled plastic; the wheel by itself is 70% recycled. By doing this, we are able again to diminish the carbon footprint further.
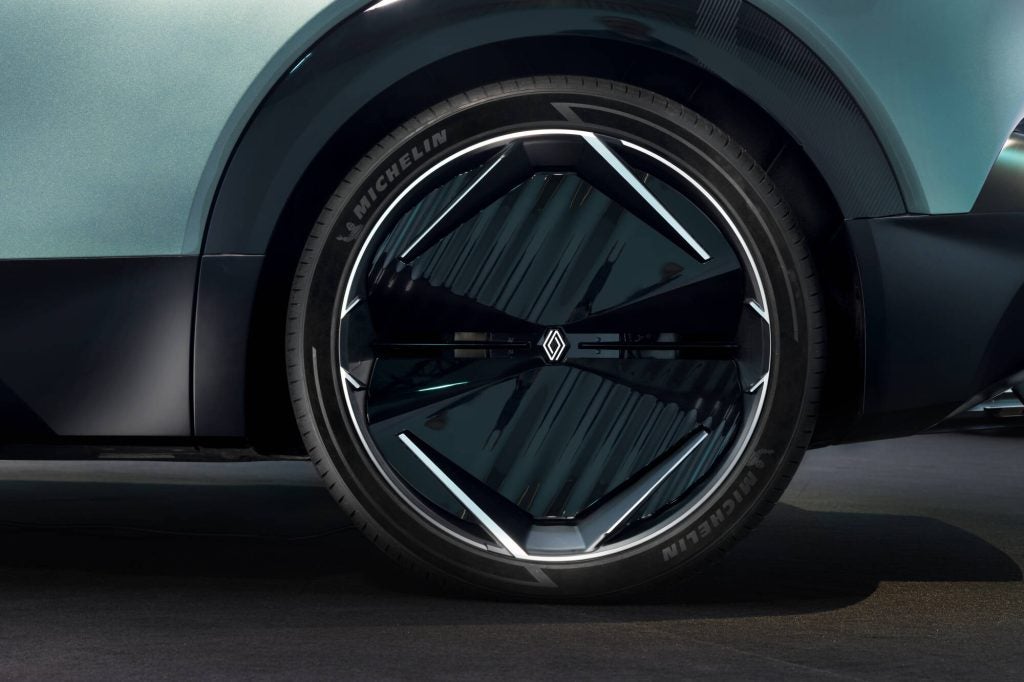
There was also work on the tyre, too, working with Michelin. That work was done to include about 30% renewable material in the tyre.
Finally, we used the whole surface of the roof to include solar cells. This was an unused surface, and we said you know what, if you put on solar cells is this a gimmick, or does it help? It helps, not a lot but it does help.
If you are in the south of Europe, it’s going to amount to an estimated 2% of the carbon footprint. If you are in the north of Europe or in a rainy area, it will be around 1% but it’s still providing 150 watts of power. This is not enough to charge your battery, but this is enough to activate a little bit of the radio, a little bit of ventilation and things like that.
Could you discuss the interior of the vehicle?
ML: For the interior we call it ‘open air architecture’. For the main display the concept is to push it as much as we can under the windshield to increase resource and optimise ergonomics, but also reduce the problem of accommodation and to reduce also the distraction of the eyes of the driver between the road and the display.
For the interior we call it ‘open air architecture’.
We gather the main information on one display. The display is on only when you want to continue to manage the different information, to manage the different applications. The display can be off when you are ready for that.
We have a compact steering wheel, which is more ergonomic. We have an upper storage which is closed with a butterfly concept, and is motorised, and we have a lower storage.
Regarding the seat, we worked a lot with the comfort of the seat; you can control the entire seat. The foam in the seat backs is bio-circular, which means it is made from biological waste.
There are two armrests on the side of the seats, and there is a footrest on the front console that allows the possibility to extend your legs. When you have three people on the back, it’s possible to cross the shoulders by having a different position between the central and the lateral.
When you are two people, you can align the three backrests to find your position and, as we don’t have any window, we have a very large headrest on the back.
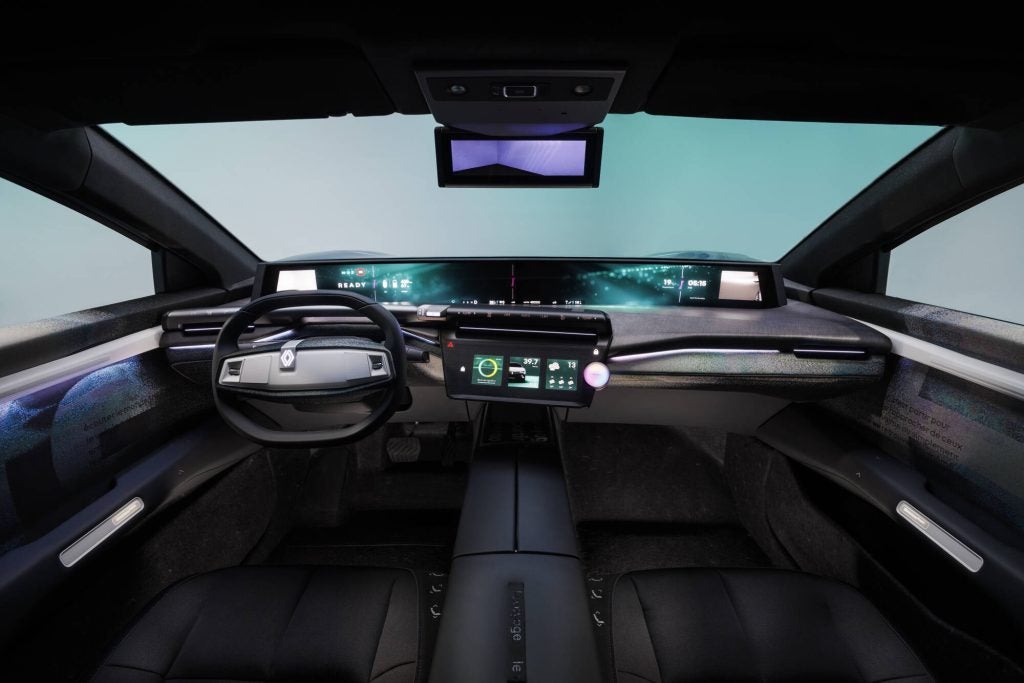
Could you discuss the recycled materials used within the vehicle’s interior?
FF: We went for the same type of approach on materials that we were doing for the exterior. Starting with the floor, as is in use now in many Renault vehicles, it is 95% recycled fibre. What we did, in addition, is that we took care of what happens to the floor at the end of the life of the vehicle.
This is a mono material floor. Usually, a floor is a mixture of PET polyurethane and latex, which means that it’s unrecyclable and it’s bonded together. What we did is use a mono material which is only PET. So at the end-of-life you can remove the floor as one item, put it in a recycle bin and recycle altogether.
This floor material was also used on many areas in the back of the seat. We also used it as a foldable part for the bottom of the doors. This floor is made with some of the fibres that are taken from the edges of a fabric. The fabric is made also with 100% recycled polyester. To do this, we actually trim the edges, and these edges are usually discarded or burned, and then what we did is that we took these fibres, and they are actually sprinkled, and these are the little colours that you can see on this on this door.
This fabric is also done in a way that we have no glue. When you have unassembled this part, the fabric can be removed without any glue and without any problem of incompatible materials.
Finally, we worked on the instrument panel. The instrument panel is made with linen, or flax. That is a plant that grows in Normandy; 90% of the flax in the world is grown there. It’s a plant that grows without the need for watering, or without the need for pesticides, and it absorbs CO2 when it grows. We take this plant, and we transform it, with the help of Forvia, for this instrument panel.
The trim by itself, is made with special weaving, so it means that there is no loss or no part that needs to be trimmed.
Could you discuss the customised design of the audio system?
Ghislain Picard (GP): Audio has not been forgotten. It is another partnership with Jean-Michel Jarre to create its own signature to provide the customer with specific and immersive sound inside our vehicles. The challenge was to do more with less. We have worked on several aspects.
The first one, we have reduced the quantity of components in the car when it comes to electronics and wiring. We have optimised the position of the loudspeaker. There are no remaining loudspeakers at the bottom of the door. Also, a loudspeaker has been put on the top of the trim to save space and to provide some space for storage in the door and to create internal volume.
We have a specific subwoofer design in the front in car cabin, which provides powerful bass directly into the car cabin. It’s creating an optimal acoustic configuration for the car and for that we have used a lighter and smaller speaker.
We are also using less software processing to optimise the sound.