Formerly part of the UK Atomic Energy Authority, Zircotec is now a fully independent organisation developing and providing an increasing range of thermal barrier and heat management coatings and products. Successfully used in motorsport, the coatings have offered light and robust heat management solutions for a growing number of OEMs such as Lamborghini. More recently the firm has been developing heat resistant coatings to allow composite materials to be used in high temperature environments. Matthew Beecham talked with Zircotec’s managing director Terry Graham about the company’s recent innovations.
just-auto: Zircotec underwent a management buyout around two years ago. How has the business developed since then?
Terry Graham: Zircotec had been owned a venture capitalist group for a couple of years prior to the MBO. Contrary to many people’s perceptions of venture capitalists, it was highly beneficial for Zircotec. They invested heavily to improve manufacturing capacity, increase brand awareness and investigate new markets. It was the latter that took us into the OEM world.
Could you tell us more about your OEM activity?
Our first OEM projects came about as a solution to solve existing heat issues on current cars. For example, in the case of the Koenigsegg, heat was causing damage to the paint on the engine cover. For Lamborghini, Zircotec’s first project was the Revènton, where our coating was the only surface treatment that met both the aesthetic and durability requirements. This experience and growing reputation has led to involvement with a number of other OEM projects We are now used on derivatives of the Gallardo and Murciélago as well as the first coloured OEM exhaust on the Ariel Atom V8 where durability and aesthetics are key.
How is the durability achieved?
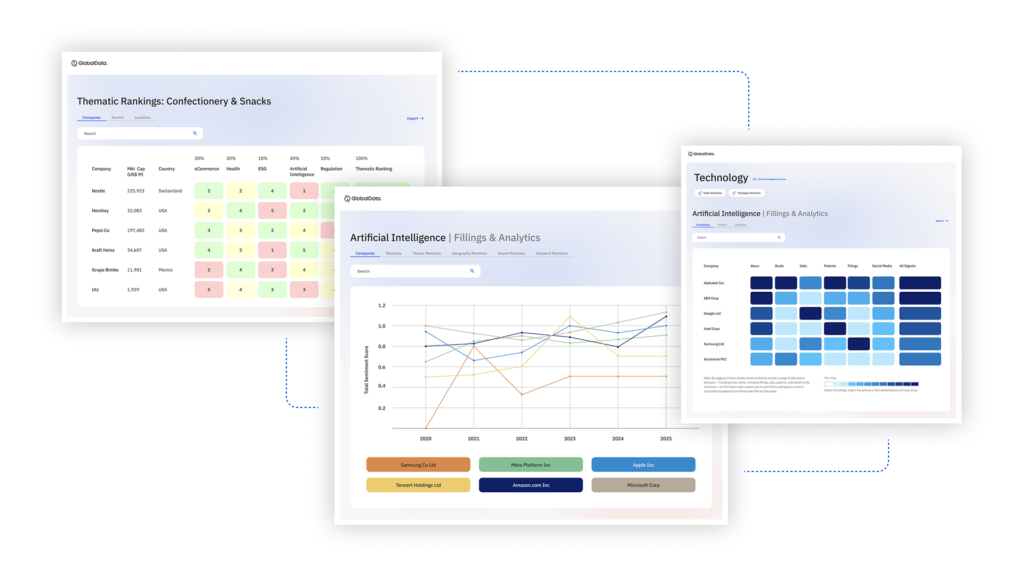
US Tariffs are shifting - will you react or anticipate?
Don’t let policy changes catch you off guard. Stay proactive with real-time data and expert analysis.
By GlobalDataMany people mistake our coating for a paint. It is not. We plasma spray our components using a plasma torch at around 14000°C initially a bond coat then top layers. We feed the appropriate feedstock, usually our own proprietary ceramic formulation for thermal management top coat into the plasma. This then impacts with the part being coated, in effect becoming welded to the part. It is this element of the process that enables us to offer a long lasting and durable finish that doesn’t crack.
I guess the process is more costly than painting though?
Yes but what we are now trying to do with the OEMs is to specify the coating early during the design packaging phase rather than a ‘distress’ purchase to solve issues once all hard points are fixed. This has, on more recent Lamborghini programmes, offered a weight and complexity saving by removing unnecessary heat shields. For the Murciélago, the coating helped contribute to an overall weight saving of 100kg over the normal Murciélago, with 33kg of the reduction coming from the new powertrain and exhaust system. We also know from testing that our coating can offer up to 50°C reduction in underbonnet temperatures and can offer the closer packaging of sensitive electrical parts nearer to heat sources with impacting on reliability.
Is this only really for niche cars or do you foresee applications on more volume vehicles than a Lamborghini?
This is something that’s been receiving more attention from us this year, due to an increasing number of RFQs [request for quotations] from component suppliers requiring small parts in higher volumes. In the summer we opened a new larger facility in Abingdon. This included a new spraying booth, dedicated robotised spraying for OEM applications as well as floor space for further expansion as we grow. We’ve recruited more people and increased the sales team to respond better to customer enquiries. We’ve also looked at the ceramic compositions and are developing a derivative we are now finalising. “Performance Diesel” is the result of research into coatings that offer thermal management but aesthetics are less crucial. This coating is significantly cheaper by 30 percent and offers the temperature reductions that will be attractive to OEMs. From our discussions, the pricing is in the right direction to be of interest to them!
Is there further development planned to satisfy OEM requirements of cost?
It is something that we are starting to work on. We feel that there is a requirement for coatings that, whilst offering some heat control, are primarily there for an aesthetic purpose. We are already progressing this type of product that and would welcome input from OEMs and tier ones as to specific requirements. We think we know how to strike the balance between durability and cost and in the coming months hope to have some test results to prove that.
Zircotec has long been involved in motorsport. Is this still the case with more OEM business and is it contributing to winning more OEM business?
Motorsport, notably F1 is still an important part of our business and we now supply around 80 percent of the F1 teams. Blown diffusers, an innovation for 2010, led to a requirement for teams to port 650-850°C gases into a composite floor to increase downforce. Composites tend to delaminate in high temperature environments but we have refined a version of our ceramic coating to prevent this. For some teams this has offered a huge performance gain. It has led to other innovations that will filter down to the OEMs in time; spraying metal coatings onto composites to protect against heat and wear for instance. We are able to apply a coating of molybdenum or aluminium onto carbon fibre. The molybdenum coating prevents wear so composite parts are lasting longer, saving money and extending service life. I also think that we are seeing the return of KERS [kinetic energy recovery systems] in F1 and later on the reintroduction of turbocharging. Both of these can benefit from increased efficiency and we are already seeing applications on the race cars for managing heat, wear and even EMC protection. Composites coating was launched to the OEM market earlier this year with a clear message that by applying the coating engineers could specify lighter composite materials in harsh environments.
Did this appeal to the OEMs?
Yes, to some of them. We will see a composite coating on a production car in 2011 to protect composites from heat and this will be coating a composite part as opposed to the heat source, say the exhaust. We also showed a ‘hybrid’ molybdenum-ceramic coating on Jaguar’s CX-75 concept car on the diffuser which was a nice link to the technology in F1. We now have to tell engineers this solution enables them to use a wider range of lighter substrates as they start to consider new materials for BIW [body in white]. We are aware of composite sandwich structures for next generation cars chasing weight reductions and it is these types of platforms that we want to be involved with to maximise their weight saving. It’s going to take some time for BIW and chassis engineers to consider composites but the trends point to this being the way forward.
As I understand the process, parts have to be sent to you. Won’t this restrict interest from OEMs particularly for larger body structures?
I think that will be true with higher volumes. At present we can manage large parts in our booths here in Abingdon but for volume introduction for OEMs in the US or Asia we’d have to consider licensing the technology to the OEM or Tier One to do the spraying at their facility. We have over 15 years’ experience of plasma spraying ceramics and could offer a turnkey solution of hardware and expertise. This could help pricing too with lower shipping and turnaround times.
Where else do you foresee the technology going?
We are running a development project to use a derivative of the coating as a braking surface for carbon rims on a bicycle. We’d heard that that braking on the carbon surface restricted riders to using cork pads and wet weather performance was unpredictable. This led some to switch to discs but there are weight and aero disadvantages. So we looked at coating the rims and got a professional rider to give us their feedback. It astounded them so we are taking this further and talking to wheel manufacturers and bike OEMs. I think it shows that there are lots of applications out there that we just don’t know about so we have to tell people what we are capable and discover these applications.