There have been some advances made to shock absorbers (dampers) which may be referred to as trends. To improve ride comfort without adding to cost, manufacturers are creating a longer shock absorber movement. Another clear trend in the shocks sector is integrating more electronics. Here, Matthew Beecham talked with executives of ZF about the challenges of developing vehicle suspensions for emerging markets, NVH improved dampers and adoption of electronic suspension technologies.
What are the challenges with developing vehicle suspensions for cars built for emerging markets?
- Adaptation to markets and to changes in the market.
- Take the technology from our home markets to the local markets, including adaptations to local requirements.
- Volume growth – but general global demand for low costs, light weight and CO2 reduction
- Different car models.
- Basic mobility requirement is key in those markets.
- Growing but diversified and customer expectations.
- Mobility and quality.
- The focus is on making mobility affordable worldwide.
- Supplier management needs to be synchronised, with a locally competitive supplier base.
The roads are clearly better in the West than they are in those BRIC countries. How does that feed through to the customer in terms of suspension ‘feel’ and driving dynamics?
Today’s chassis must meet the increased requirements for driving dynamics, safety, and comfort. Modern axle systems owe this high functionality mostly to complex structures with many components. Due to functional separation, the suspension allows for a targeted design of chassis-specific characteristics. Axle designs by ZF must therefore meet the most varying specific requirements. It’s not just about the vehicle type – from sporty roadsters to off-road, all-wheel-drive vehicles – but also about the individual driving feel of a model. Depending on the motorisation and load class, various different shock absorbers and springs are used, including especially adapted suspension arms (made of aluminium or steel). The suspension is indeed one of the most complex systems in a passenger car: It bears loads, compresses, dampens, steers, stabilises, brakes, and transfers power from the drive to the wheels – and thereby onto the road.
As a global player, do you see future suspension requirements differing or converging in the various markets?
Local development teams work together with ZF development teams in Germany. The technology is based on global platforms but adapted to local needs. An example is the improvement of the robustness which is achieved by using hydraulic rebound components inside the shock absorber. This is defined based on local needs together with our customer.
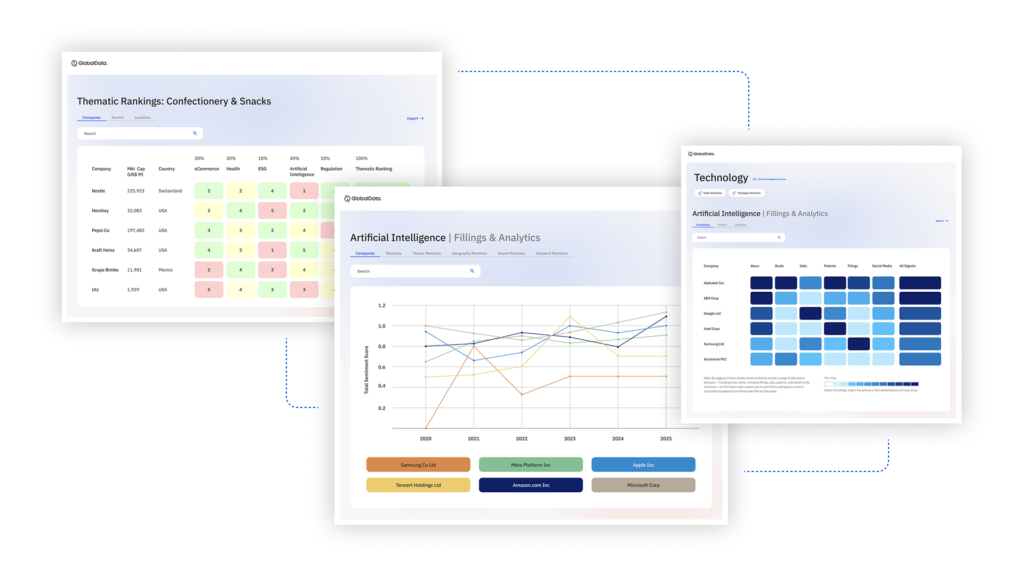
US Tariffs are shifting - will you react or anticipate?
Don’t let policy changes catch you off guard. Stay proactive with real-time data and expert analysis.
By GlobalDataHow is the adoption of electronic suspension technologies progressing?
We see a growing potential for mechatronic systems in the field of suspension technology. Based on the car connectivity, new information can be obtained and new tasks can be achieved with regard to suspensions.
Our CDC [Continuous Damping Control] technology is a perfect example.
Generally speaking, at an industry-wide level, how do you see the acceptance and growth rate of continuous damping technology by the OEMs?
General acceptance is already given to higher car segments, often in combination with airspring systems. In general, the penetration rate for CDC technology will grow, also in smaller segments. This will lead to new ideas with regard to structure and functionality. The 1XL CDC system is our answer for small passenger car and light commercial vehicle applications.
ZF’s electronic damping has been winning over vehicle manufacturers since its market launch in 1994 – and is still doing so with its fourth generation. The continued increase in CDC production figures illustrates this; 2011 marked the temporary record high with more than 2.2 million shock absorbers produced for the following customers: Alpina, Audi, Bentley, BMW, Ferrari, Maserati, Opel, Rolls-Royce, Mercedes-Benz, Porsche and Volkswagen. A total of around 14 million CDC systems have already come off the production line at ZF. Consistent expansion of the range has in particular played a major role for this success.
ZF expects an annual production of more than three million CDC units for passenger car applications by 2016. This does not include ZF systems for buses, trucks, agricultural machinery and motorcycles.
What impact is the drive to reduce vehicle mass having on damper design?
With lightweight solutions, we offer two main benefits to the car. On the one hand, the weight reduction influences the car’s fuel consumption and CO2 emissions in a positive way. On the other, the driving comfort is improved by reducing the unsprung masses of a chassis system.
I guess aluminium drifts in and out of favour with OEMs as the relative costs of steel and aluminium shift. Because of this, I suppose steel will remain the dominant choice for shock absorbers?
Cost competitiveness is always an existing challenge within our business. This also means that the acceptance levels of additional costs for lightweight designs are changing. We all have to keep the upcoming car CO2 regulations in mind. These will accelerate lightweight solutions in all material types. We are looking for functional integration and the right technology at the right place; this could be steel, aluminium, FRP or hybrid designs.
As vehicles become ever quieter, what advances have been made to your dampers to improve NVH?
The remainder of this interview is available on just-auto’s QUBE research service