Ride control is basically governed by a vehicle’s suspension system, including its shock absorbers (dampers) and struts. For the last decade or so, the high-end technical emphasis has been on developing dampers in which the damper rate can be varied according to the road conditions. Another clear trend in the shocks sector is integrating more and more electronics. Continuing just-auto’s series of interviews with major component manufacturers, Matthew Beecham talked with Rolf Heinz Rüger, executive vice president, chassis technology, and head of business unit Suspension Technology, ZF Friedrichshafen AG.
What are the main challenges facing shock absorber suppliers in general – and ZF in particular?
- Cost awareness of car manufacturers.
- Globalisation of car platforms with different requirements regarding functionality.
- Localisation: Global presence as supplier with local development and production activities. Installation of technical sales offices to consult customers locally. With 121 production sites worldwide ZF ensures an optimum regarding product quality and logistics.
Can you talk us through your shock absorber portfolio – how will you make each of these competitive?
Differentiation of the product portfolio in three main product lines has been done to offer car manufacturer tailored solutions. The BasicLine with uniform product specifications means a clear standardisation in development and production of twin-tube dampers and suspension struts. Whereas the CustomizedLine is based on a modular system and meets customer-specific wishes. The development work behind this line has produced stronger individualisation and a greater focus on vehicle adaptation. Finally, the ActiveLine covers all controllable damping systems. These systems communicate with the vehicle’s other safety systems; they continuously respond to current vehicle data and thus ensure that damping is adjusted to the actual driving situation. In each product line the development work is pushed on.
As a global player, do you see future product requirements differing or converging in the various markets? In what ways?
We see a high expectation of OEMs, especially in Western Europe but also in some emerging markets, regarding driving safety, dynamics and comfort. In some other markets it is necessary to fulfill best function and driving safety.
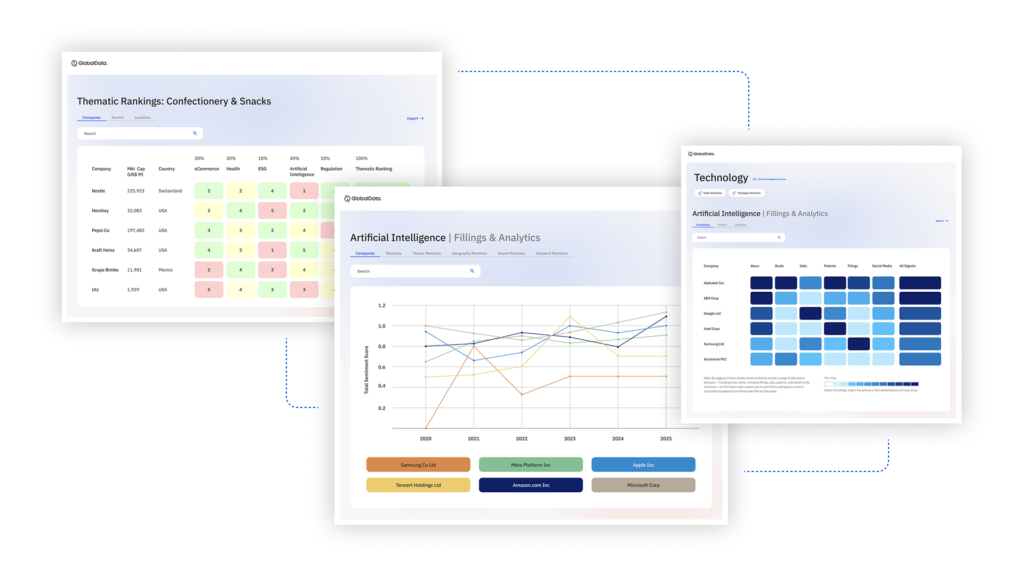
US Tariffs are shifting - will you react or anticipate?
Don’t let policy changes catch you off guard. Stay proactive with real-time data and expert analysis.
By GlobalDataElectronics for dampers has meant a quantum leap in terms of the level of stability and comfort for new vehicles equipped with this type of system. Yet the technology is still expensive compared with the conventional type. So is there a trend for active or semi active suspension?
There is a clear trend towards electronically controlled suspension systems, worldwide. This year, for example, ZF delivered the 12 millionth CDC damper [Continuous Damping Control]. This electronically controlled damping system has seen an enormous growth over the last three years. We are also able to offer different types of the electronically controlled system – with external or internal valve. The latest development is the CDC 1XL – a system especially for the rear axle of a compact car.
What are the perceptions of electronic suspensions at the OE level?
Electronic suspension systems more and more are gaining market shares and are penetrating lower vehicle segments as the customer benefit is obvious.
What drives OEs to adopt new electronic suspension technologies? Who have been the early adopters and who will be next?
OEs perform with these systems increased driving safety, dynamics and comfort. Passive dampers are clearly behind the performance. Another reason is the possibility to connect the safety car systems with the dampers. Integrating the sensor systems, control software, and control technology of the individual units into a system that works together can result in critical driving situations being identified and corrected much quicker than can be expected of the driver. There is increasing demand for innovative, electronically controlled technologies to be networked and integrated into vehicles.
What are the perceptions of electronic suspension from the consumer standpoint?
An increase of driving safety, comfort and dynamics. Also the possibility for individual driver’s set-up is relevant.
What is the impact of electric and fuel-efficient vehicles on shock absorber design?
The whole chassis design is influenced due to the electrification of the powertrain. For example, not only the increased weight due to battery packs but also the new weight distribution challenges [due to] the development of suspension technologies. One approach of ZF is to develop new lightweight dampers. Saving weight in the chassis has multiple advantages: Less weight directly reduces fuel consumption and CO2 emissions. And there is another advantage: If the share of unsprung masses is smaller, vehicle dynamics, comfort, and safety are on the rise.
To what extent has high strength steel helped in reducing damper weight? And I guess aluminium damper tubes can help reduce weight, too?
Lightweight design is one of the core areas of expertise at ZF. There are various mutually combinable “intelligent lightweight design” strategies to reduce damper weight. One way is to use lighter or alternative materials, such as glass-fibre reinforced plastics (GRP materials), aluminium, magnesium or high strength steel. Another option is to use finite element methods to optimise dimensions and component design. Thanks to expert utilisation of the latest methods and processes, such as cold-pressing lightweight components, ZF is a specialist in large-scale series production and strategic development projects. The third way to reduce weight is the integration of functions. The revolutionary lightweight suspension strut wheel carrier module demonstrates this approach.