Demands by automakers for more braking performance with minimal cost or weight penalties continue to drive manufacturers like TRW to come up with new ideas. Although advances in friction materials and caliper designs have helped improve braking performance, the main improvements in braking in recent years have come from electronic control, firstly ABS (anti-locking braking system), then ESP (electronic stability programme) and now brake-by-wire. In this interview, Matthew Beecham talked with TRW’s engineers about such braking system developments.
just-auto: What trends are you seeing in OEMs’ strategies with regard to electronic braking system functions?
TRW: Adding further functionality to the overriding building blocks of anti-lock braking, traction control and electronic stability control to enhance safety while reducing size, weight and cost has been a priority for a number of years now. As more data has become available regarding accident types and severity (for example, the increase in rollover accidents as higher centre of gravity vehicles entered the market), new strategies such as active rollover management through software were employed. Or when studying the severity of trailering accidents, the need for trailer brake stabilisation became clear.
More recently, the opportunity to use data from GPS or other infrastructure inputs can allow for features like curve prediction and corner brake control to work hand-in-hand to assist drivers in knowing when to brake and in helping with vehicle control when braking in a turn. There is also a trend toward implementing low speed collision mitigation braking systems combining camera or radar with electronic brake systems to assist the driver at urban speeds.
Another big challenge is alternative powertrain brake solutions. Unlike the traditional internal combustion engine – direct injection, diesel, hybrid electric and full electric powertrains supply little or no vacuum that can be used to amplify the brake force applied by the driver to actuate the vehicle hydraulic brakes. This requires a different actuation strategy and an electronic brake apply system that can supply high amounts of brake pressure in a short period of time for certain braking scenarios. When the OEM incorporates regenerative braking, the system must blend friction braking with regenerative braking, presenting a further challenge, as these two systems must perform seamlessly to the driver. TRW has developed a Slip Control Boost system in production on GM vehicles such as the new Chevy Volt which has its own hydraulic booster.
What are the most cost-effective electronic braking systems to implement?
How well do you really know your competitors?
Access the most comprehensive Company Profiles on the market, powered by GlobalData. Save hours of research. Gain competitive edge.
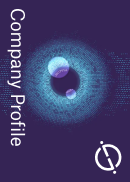
Thank you!
Your download email will arrive shortly
Not ready to buy yet? Download a free sample
We are confident about the unique quality of our Company Profiles. However, we want you to make the most beneficial decision for your business, so we offer a free sample that you can download by submitting the below form
By GlobalDataThe basic anti-lock braking system is still the most cost-effective system to implement as it does not add some of the sensors (steering angle, yaw, etc.) needed for full electronic stability control. In markets like Brazil where this has now been mandated and all passenger cars will have ABS by 2014, this is a viable option and is also still being fitted in other emerging markets.
Additionally, with the mandates for all passenger cars to have ESC in the western markets of Europe and the US, there is a continual drive for cost reduction. TRW has a lower cost version of its stability control system that eliminates the need for a pressure transducer and can help cut the cost of the system by five per cent or more. There is also a push towards electronic integration to eliminate the need for separate sensors and Electronic Control Units (ECUs). Among the strategies that TRW employs is the integration of the ESC and the Electric Park Brake (EPB) – a system we call EPBi or integrated EPB. The control software for the EPB unit is now included in the ESC ECU and thus eliminates the need for a separate control unit. We have also integrated sensors into our Airbag Control Units (ACUs) and this has provided OEMs with similar cost reduction benefits.
What are the challenges in reducing the cost of electronic braking systems?
There is always a desire by the vehicle manufacturers to reduce size, weight, complexity and part count, etc. – all while increasing the functionality of the system. This is a challenge as electronics and software engineers work to incorporate new features and functions – but instead of adding hardware that has a tangible cost – the vehicle manufacturers want less hardware at a lower cost with greater functionality. As these functions become more complex, they take more processing power and typically require more powerful microprocessor units – which of course add to the cost.
For suppliers, one of the important strategies to keep costs down is to maintain common bills of material, manufacturing equipment, and processes, etc. These efficiencies of scale allow for the units to be produced at lower cost.
After automated braking becomes mandatory, the pressure to introduce automated collision avoidance systems seems likely to increase. What are the technical challenges the industry must overcome?
Technically these systems have already been developed and proven through testing, although there is still a long way until more vehicles are fitted with such systems and performance in real world driving conditions takes place. The systems will continue to evolve as more data from the roadways show how the system reacts to a myriad of situations.
The demands for cost reduction for camera and radar systems that enable these technologies are already ramping up and will continue to do so – a bit of a chicken and egg scenario as more volume and scale are required to help drive the cost down. Furthermore, there is a learning curve for drivers to understand how the systems work and how they should interact with them.
Could you explain how your collision mitigation braking system works?
TRW’s CMB system uses a radar sensor to directly measure the distance and relative speed to objects in front of the host vehicle. If a potential collision is identified, a warning is triggered to alert the driver; this warning can be audible, visual or haptic. If the driver does not react to the warning and the system determines that a collision is likely to occur, a certain amount of brake pressure can be applied automatically to slow the vehicle and reduce the severity of the impact. If the driver does respond to the warning and depresses the brake pedal, the brake system will automatically provide maximum brake boost to slow the vehicle as quickly as possible and mitigate the collision. The technology is primarily designed for urban driving conditions including heavy traffic.
While the above type of braking technology has its merits, are there issues about the ability of drivers to accept and use an array of emerging technologies, such as radar-prompted braking?
Firstly, there is a clear requirement for more active safety systems such as radar enabled braking to help reduce or mitigate the number of fatalities on the roads. According to EU road safety data, fatalities have decreased over the last decade (mainly due to passive safety technologies) but are starting to flatten out. Therefore the industry needs to focus more on active systems in order to stop smaller incidents turning into larger accidents.
It’s important that drivers realise that as long as they are driving safely, such systems will not need to intervene – they are purely there as a safety net in case the driver is distracted or loses concentration for a second or two. To help drivers better understand and accept such systems, there is certainly a role for the industry and government organisations to play in order to help educate consumers on the benefits of such systems.
Is there a concern that the continual evolution of fool-proof cocoons discourages drivers from accepting personal responsibility and improving their driving skills?
The point of these systems is not to take away the driving experience but to provide assistance if a situation becomes dangerous or critical. We always emphasise that no system can overcome the laws of physics and that drivers cannot relinquish responsibility for vehicle control. According to the Vienna convention, the driver needs to have permanent and full control of the car at all times. Active systems are there to help when the driver isn’t in control.
How do you see the acceptance of advanced braking technologies in emerging markets?
The example of the Brazil ABS legislation shows that governments can and will take action to introduce important technologies to the marketplace.
TRW’s stance is that all drivers, passengers and other road users deserve to be safe. In emerging markets like China where road safety is a significant and growing issue, it is critical that drivers have advanced technologies and learn how to use or interact with them. A big challenge ahead is not just equipping vehicles properly but changing the mindset of vehicle drivers and other road users in understanding that the rules of the road are very important. TRW has launched and is continuing an effort to teach Chinese children basic safety precepts such as buckling seat belts and how to cross the road safely. The acceptance of technologies and the safe driving mindset will take time but ultimately should prevail.