Emissions legislation, weight, packaging, safety and cost are the main factors driving fuel tank innovation. Matthew Beecham talked to Albert Boecker, Product & Advanced Engineering Director, Global Fuel Tank Systems, TI Automotive about the supplier’s fuel system technology and what can be done about ‘fuel slosh’.
As we understand it, legislative mandates and rulings led by environmental concerns are the main technology and design drivers in the fuel system world.In terms of the automotive fuel tanks market, what are the big changes you see in the automotive industry?
There are a number of trends and changes pending in plastic fuel tanks due to the OEM vehicle response to emissions and fuel economy targets. Plastic fuel tanks continue to optimise for light weight, fuel slosh noise reduction, mounting stiffness, operating pressurisation and temperature insulation.
The transition to smaller fuel efficient vehicles is driving ‘flat fuel tank’ geometry which helps the OEMs to offer larger interiors and cargo space in overall smaller vehicle packages. In terms of packaging fuel system components, what trends are you seeing there?
The implementation for flat fuel tanks is primarily used in small Japanese vehicles only. The size of the fuel tank and application position is largely dependent on the specific vehicle fuel range, emissions level and other vehicle options such as electrification.
What is unique about your Tank Advanced Process Technology?
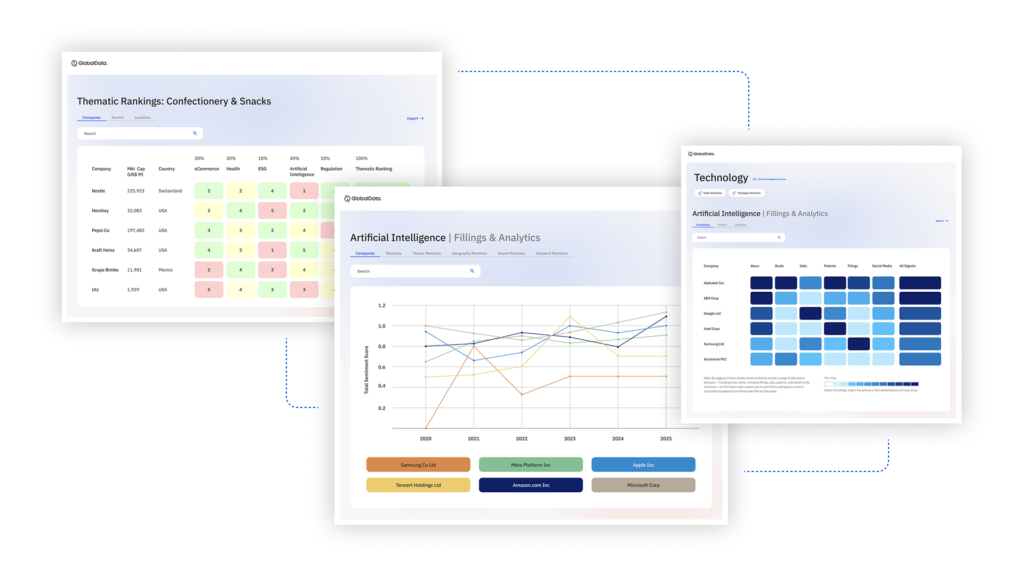
US Tariffs are shifting - will you react or anticipate?
Don’t let policy changes catch you off guard. Stay proactive with real-time data and expert analysis.
By GlobalDataTAPT is an adaptable manufacturing process approach to integrate components in a plastic fuel tank. The mould opens in the first stages of forming and separates the preformed shape along a designed seam. Tooling grippers are used for robot insertion of components. The mould then closes for optimised sealed pinch flange. This allows OEM vehicle applications to communise tooling and processes, develop complex fuel tank shapes, add slosh/emission/pressure features.
We understand that TAPT is on the Mercedes-Benz S Class. What are your ambitions for it to be applied to other OEMs around the world?
The remainder of this interview is available on just-auto’s QUBE Global light vehicle fuel tanks and delivery systems market- forecasts to 2030