Tenneco Inc is one of the world’s largest producers of emission control products. Its OE product ranges from the exhaust manifold to tail pipe. For the aftermarket, Tenneco designs and produces mufflers for virtually all North American, European, and Asian makes of light vehicles. In this interview, Matthew Beecham talked with executives of Tenneco Automotive about some observed trends in the exhaust sector.
just-auto: The current trend on gasoline engine, at least in Europe, is the downsizing linked with introduction of turbochargers. For example, a 1.6-litre North America gasoline becomes a 1.2-litre turbo gasoline. In what ways has this trend affected the exhaust system?
Tenneco: Since exhaust flow rates will remain at the same level for similar power, the catalysts are not going to be smaller. In addition, high low end torque for direct injection gasoline engines will continue to need specific noise, vibration, harshness (NVH) solutions.
The economic crises has led to a change in customer behaviour and switching to smaller and smaller vehicles. In terms of exhaust and catalytic systems, does that pose technical challenges?
Vehicles with smaller engines require the same NVH performance as larger vehicles which have already a high degree of technical/engineering expertise. We just apply this expertise to the smaller engines.
Although a lot has been said about the prospects for PEVs, the IC engine will be around for the foreseeable future. How do you see the powertrain market over the next 5 – 10 years?
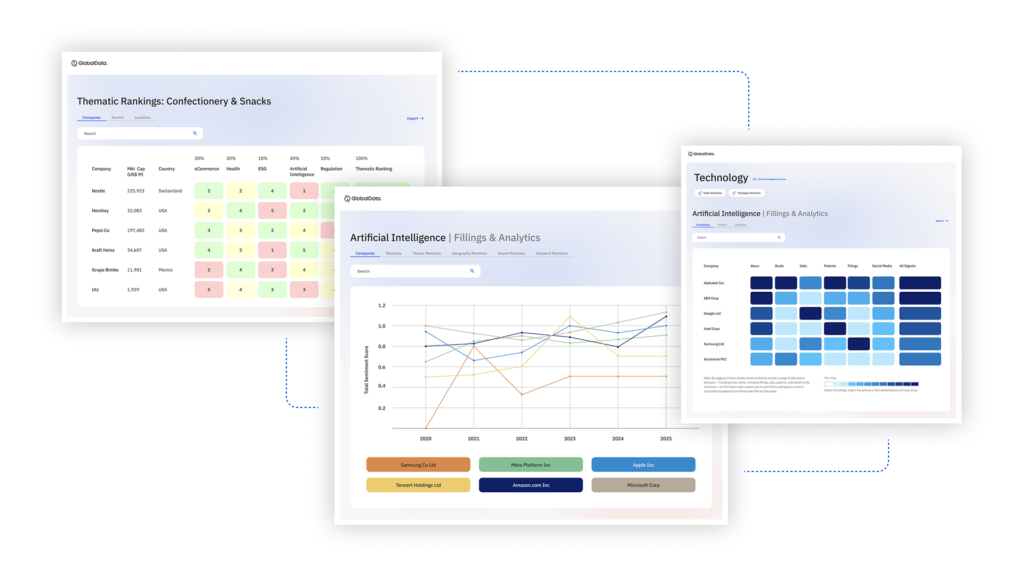
US Tariffs are shifting - will you react or anticipate?
Don’t let policy changes catch you off guard. Stay proactive with real-time data and expert analysis.
By GlobalDataThere will be some degree of hybridisation for larger engines. Smaller engines will probably be downsized and charged with direct injection gasoline engines whereas bigger engines will probably be mainly diesel.
Despite some people saying the IC could be in sharp decline in 15 – 20 years’ time, I guess there is still considerable scope for its development.
There will continue to be high demand for internal combustion engines for commercial vehicle and off-road applications.
As far as gasoline engines are concerned, after-treatment systems appear to be on a level although we understand that there is some development work underway to control thermal management. What do you see happening with respect to gasoline engine after-treatment systems these days?
Gasoline engines will increasingly require lightweight and low backpressure exhaust systems to help meet CO2 reduction targets. Furthermore, the engines will most probably be direct injection with requirements for particulate aftertreatment (number limit) as well as on NOx aftertreatment when engines are operated lean for optimum fuel economy. Another interesting trend could be exhaust heat recovery to re-use one third of the fuel energy that is otherwise wasted.
For some time, we seen how carmakers have paid close attention to exhaust sound in order to maintain and enhance its “brand”. How do you set about supporting the carmakers achieve the right note?
Carmakers are very keen on original sportive sound and we are working on active sound solutions. For example, more and more automobile manufacturers are requiring a typical sound pattern for a car or a platform, even a unique brand sound for a whole brand. Sound design is therefore becoming increasingly important for exhaust system development. The whole sound pattern, especially the tailpipe noise of the exhaust system, plays an important role in the subjective impression of the car.
There are two sound classifications: the limousines with a harmonic, quiet and discrete sound whereas for sports cars a more rough and powerful sound is requested.
Compared with the gasoline engine the diesel engine has, based on inner power driven processes, a minor sound spectrum because its harmonics and main orders are hardly audible and mostly attenuated by a turbocharger. For turbo charged engines, special concepts have been worked out in order to achieve a sporty sound. Connecting pipe resonance and muffler chambers are used for sound design.
The degree of freedom for sound design is mainly determined by the number and arrangement of the cylinders. In addition to the number of cylinders, tuning of the valve control timings represents an efficient power driven possibility for a sound design.
I guess because of the increasing cost and price volatility in the precious metal markets, this is forcing manufacturers to squeeze more performance out of smaller catalysts. What is happening to catalysts these days?
Coaters are continually improving their washcoats, leading to a reduction in precious metal (PGM) requirements. In addition, there are ongoing initiatives to replace the PGM with cheaper catalysts. SCR catalysts, for example, are PGM free. This applies to Tenneco’s hydrocarbon lean NOx system which uses silver instead of PGMs.
Is there a trend toward using multiple exhaust gas sensors in order to deliver the performance improvements and reduced catalyst size?
There is an increasing need for sensors to control aftertreatment products, including sensors for thermocouples, pressure, particulate matter (PM) and NOx. They are required to ensure the functionality and to enable the legally requested onboard diagnostic control. However, we do not anticipate a reduction in PGM content or converter size as a result of increased sensor use.
For some time, we’ve seen increasingly stringent emission legislation introduced leading to the exhaust after-treatment system becoming more complex, particularly for diesel engines. What lies ahead for diesel after-treatment systems?
This implies further improvement of NOx and PM aftertreatment products; integrated systems; increasingly user friendly and reliable DPF (diesel particulate filter) regeneration; service-free filters; exhaust heat recovery and low pressure exhaust gas recirculation.
Finally, in terms of developing increasingly complex exhaust systems, how do you manage the delivery of those systems yet keep lead time and costs under control?
Tenneco is introducing more efficient Resource Management Tools and performing more up-front simulation work in order to reduce development time.