Continuing just-auto’s series of interviews with tier one manufacturers of fuel injection systems, Matthew Beecham spoke to Stefan Seiberth, president, gasoline systems, Robert Bosch GmbH about market and technical trends in the gasoline direct injection sector.
In terms of market growth, what are your projections for GDI over the next 5 – 10 years? Can you see GDI becoming the dominant ICE?
The gasoline direct injection will for sure play a strong role over the next decade, as it is one of the key components for fulfilling future emissions standards. But we at Bosch also believe in the further growth of diesel, alternative fuels and of course electrification. For gasoline direct injection we predict a strong growth in the triad – Europe, North America and China. Approximately half of new European vehicles with gasoline engines will have direct injection by as soon as 2016. We are currently doing excellent business in Europe with gasoline direct injection. But in a few years, there will be lots of action in the US and China too. In these markets, the innovative injection systems are still largely restricted to imported vehicles. However, with automakers in China and the US facing tough new emissions legislation in the future, they will increasingly adopt the new technology. For example, we predict that one-third of newly-registered vehicles in China will be equipped with gasoline direct injection technology by 2020.
In terms of trends in injector technologies, what are you seeing at the moment?
For direct injection we see a variety of fascinating technical developments. We aim at making each car more economical and fun to drive. Bosch sees gasoline direct injection as a system rather than just as an injection process.
Let’s start with the most commonly known feature: higher pressure. This one pays off in terms of efficiency. As in diesel engines, in gasoline direct injection engines a higher pressure will – apart from other factors – result in a leaner burning process and therefore in lower emissions and lower fuel consumption.
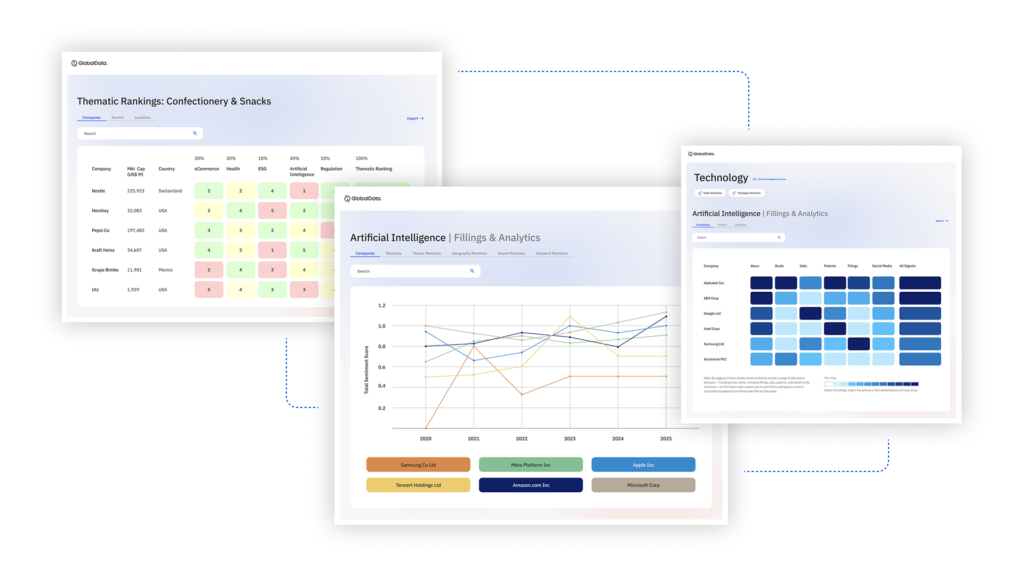
US Tariffs are shifting - will you react or anticipate?
Don’t let policy changes catch you off guard. Stay proactive with real-time data and expert analysis.
By GlobalDataSecondly let me mention our Scavenging technology. This innovative system approach eliminates the turbo lag by briefly opening the intake and exhaust valves simultaneously. This creates a dynamic flow between the intake and exhaust sides of the engine and increases the supply of fresh air in the combustion chamber. This fresh air purges the exhaust gas contained in the cylinder by forcing it through the open exhaust valve in the direction of the exhaust manifold. The increased exhaust gas mass flow generates up to 50 percent higher torque at low engine speeds, which counteracts the turbo lag.
And last but not least, we have laser drilling, which helps cut emissions. The gasoline is injected directly into the cylinder through five tiny laser-drilled holes. By drilling the five holes in the injection nozzle with different diameters, Bosch achieves the best possible control over fuel distribution in the combustion chamber.
What developments is Bosch doing with respect to injector technologies for alternative powertains?
Generally we see direct injection technology as a perfect basis for electrified engines, as it allows the construction of compact, downsized and nonetheless highly performing engines. These downsized engines can be combined either with a 48-volt hybrid, a strong hybrid or even a plug-in hybrid. Further, Bosch also develops innovative technologies for other alternative powertrains like Flex Fuel or CNG. At the moment, these rely on the established port fuel injection. Direct injection is also a technical option with these concepts, which is also being considered at Bosch.
To what extent does GDI particulate emissions remain a challenge for engine developers?
That depends on the individual circumstances of each engine developer. For Bosch I can say that we deal with several cost-efficient inner-motor concepts. Bosch components can do their bit to improve the combustion process. This includes a better spray-design through the optimization of the injectors, an optimization of the point of injection and higher pressure. On the way to Euro6c, Bosch focuses on the optimization of the whole system – which includes lower CO2-emissions as well as lower particulate emissions.
It appears that OEMs are slow to adopt gasoline particulate filters. Why is that?
The particulate filter has reduced the particulate emissions of diesel engines significantly. But car drivers know that this additional piece can add additional costs and may also reduce the efficiency of a vehicle. Again, for Bosch I can say that we deal with several cost-efficient inner-motor concepts.
I guess recent advances in electronic controls have brought HCCI to the precipice of workable reality. What is your opinion of how HCCI technology can meet the requirements?
Advanced combustion modes like HCCI are viable fuel economy measures and were enabled by the recent advances in engine controls and combustion sensing technologies. As with any new technology, the cost benefits not only need to consider the fuel economy, but also future feasibility when it comes to exhaust gas after treatment. Bosch is moving forward with development of controls technology, demonstrated by findings in the US department of energy funded project ACCESS.
In the longer term, I guess that stratified DI, alternative combustion systems and gaseous DI are all potential candidates for further CO2 reduction?
At the moment stratified DI remains a niche solution within the global market – although it has advantages when it comes to the thermodynamic aspects. It is right that all the systems mentioned above have the potential to reduce CO2 reductions, so they are all being considered as alternatives at the moment. However, we have to see which of these systems are suitable for the mass market in the end.
Whichever way you look at it, EVs remain expensive despite government grants being offered yet still give motorists range anxiety with just 100 miles between charges. What needs to happen to EV batteries to improve this situation?
Bosch predicts a mass market for electrified powertrains by 2020, when we predict about 2.5 million electric vehicles will be sold worldwide, as well as 6.5 million strong hybrids and 3 million plug-in hybrids. Until then, Bosch will improve the technology to offer batteries that have twice the energy density and cost half as much. We see several opportunities to reach this target – one way to further improve the energy density would be to optimise the materials used for the cathode and anode.
What needs to happen to make electromobility affordable? Presumably that includes things like standardisation of components?
The remainder of this interview is available on just-auto’s QUBE fuel injection research service