PFC Brakes develops and manufactures braking systems for motorsport, high-performance road, commercial vehicle and motorcycles. Matthew Beecham spoke to Peter Babbage, managing director at PFC Brakes Europe to discover how upcoming materials legislation is affecting the design of brake components for the commercial vehicle sector and how it is responding to ensure OEM and aftermarket customers can comply with the forthcoming legislation outlawing certain materials and how the technology could lead to lower running costs.
Could you explain a little more about PFC Brakes?
PFC Brakes, also known as Performance Friction, is a US company with headquarters in South Carolina and have been producing brake parts for over 60 years. We are best known for our motorsport parts, where we have won more championships than any other brake manufacturer in the world. Less well known is our activity in the OE and fleet sectors but in the US, PFC is trusted by both OEMs and some of the larger, key fleets. There are 40,000 police cars using PFC brake components in the US for example.
And where does PFC Brakes Europe fit into the PFC organisation?
We are responsible for sales outside of the US. This includes OE, aftermarket, CV, motorsport and motorcycle applications. From our facility in Banbury, UK we serve these markets stocking product and receiving weekly shipments from our manufacturing location in the US. We have enjoyed significant growth in the past 12-18 months, with new projects including being specified as the official partner for the Porsche Supercup. We offer sales and technical support to OEMs, race teams and individuals.
We understand that there is a raft of legislation for braking manufacturers to comply with in the future. Can you outline what these are?
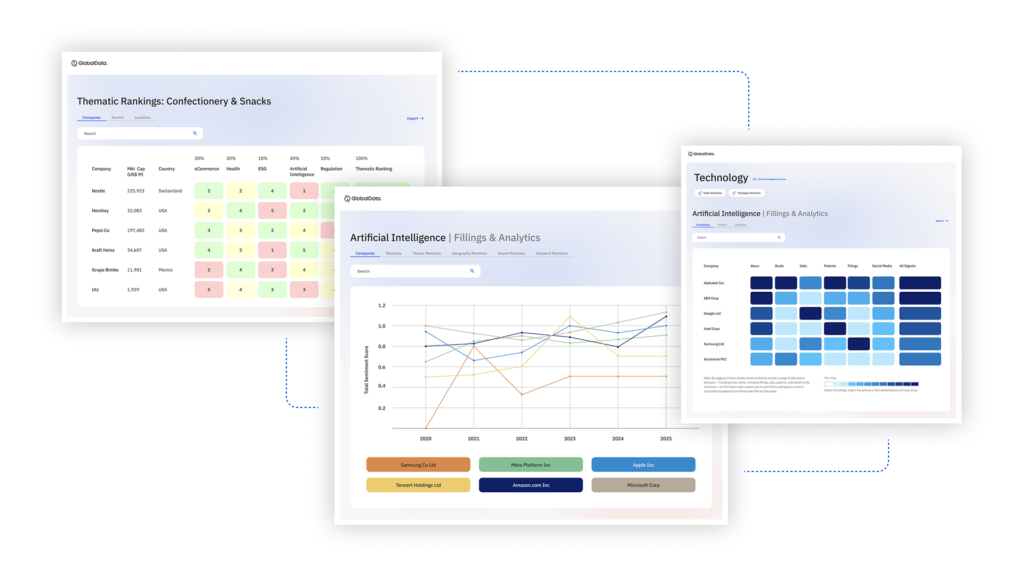
US Tariffs are shifting - will you react or anticipate?
Don’t let policy changes catch you off guard. Stay proactive with real-time data and expert analysis.
By GlobalDataHistorically, our industry had a record for using potentially hazardous materials, although PFC has never used these substances. Asbestos is a good example that most people are aware of. In March 2010, a number of States in the US passed legislation affecting many other materials, not just asbestos. In effect, that ruling will effectively ban the use of copper in brake pads by 2025 in California (Senate Bill 346) and Washington (Senate Bill 6557). It is a staged process; all brake pads must contain less than 5 percent copper content starting in 2021 and, if proven feasible, the legislation could virtually eliminate copper to less than 0.5 percent by 2025. In addition, brake pads manufactured after January 1, 2015 must not contain asbestos, chromium, cadmium, mercury, or lead. We expect that other States will follow suit. Copper legislation is already being proposed in New York, Rhode Island, and Oregon. You only have to look how catalytic converters spread from California and why brake OEMs should already be preparing for it.
This would appear to be a dramatic change. How is your industry coping?
In very different ways. On one hand there are organisations continuing to offer products containing these materials and seemingly content to continue to supply them. On the other, companies such as PFC Brakes are already offering solutions to ensure distributors and OEMs specifying pads for vehicles on sale in 2015 meet the legislation. PFC Brakes has, in fact since 2006, offered copper free brake pads and we already offer, today, brake pads that do not contain asbestos, chromium, lead, cadmium or potassium titanate.
Why is copper used by some OEMs and, if you are not using it, how are you solving the issues?
Copper was used by some manufacturers as a way of managing heat and noise. Friction materials often see relatively high temperatures, sometimes in excess of 500°C on the surface when in contact with the disc. This creates a fine powder that is released as a dust that could end up in the waterways. This was the concern in California for instance. PFC Brakes on the other hand, uses a proprietary brake pad material called Carbon Metallic. It is a multi-layer composite using carbon powders and fibres in a metallic matrix. This composition improves the thermal stability as well as the noise characteristics so you have a much quieter pad. In addition, PFC Brakes’ compounds have been proven to last longer too. Major fleets in the US such as Ryder and U Haul have demonstrated that they do last longer, saving money too. Crucially, longer brake life means less downtime and more time on the road for fleet operators. We have a number of trials with a range of fleets ongoing in the UK. These range from an ambulance fleet right through to bus operators. We expect to announce the results in the coming months, even to those loyal to a current brand today.
Do you find fleets loyal to brake suppliers or do they change regularly?
We find that the challenge is convincing the distributors that have the contracts with the fleet customers to change to us. The longer life our pads and discs offer means they require less frequent change and rather short sighted, some are concerned about the effect on sales. This frustrates both us and the fleet operator and with some end users, we are now selling direct. It’s another reason why we have been investing in our UK infrastructure to be able to supply more parts directly. We are disappointed by the position of some of the distributors but we are finding ways to deal with it.
Fleets focus heavily on fuel costs. Can brakes play a part there?
Yes, brakes can improve fuel efficiency and we have really strong data from customers in the US that brake technology can improve fuel efficiency. Originally developed for use in our motorsports range, PFC Brakes’ Zero Drag technology is a pad retraction system whereby a spring retracts the pad away from the disc, thus avoiding wear and drag. It offers more too; the increased stiffness of the aluminium caliper delivers less pedal travel and an improved response, as well as a significant reduction in vehicle weight, thus allowing a greater payload to be carried.
I can see how that can be advantageous but do the costs of the system make it worthwhile?
Absolutely, the PFC system not only saves on pad and disc wear but there are the fuel savings too. In the US, where we have the most data, the payback is less than one year, exceeding targets set by the leading fleets. We have evidence of fleets in the UK currently having to change brake pads every eight weeks; that really adds cost with time off the road adding to the complexity. Together with our brake pad compound technology and innovations such as Zero Drag, it is possible to make a difference to the bottom line.