Nexteer Automotive is a multi-billion dollar global steering and driveline business solely dedicated to electric and hydraulic steering systems, steering columns and driveline products for original equipment manufacturers. Its 6,200 employees serve more than 60 customers in every major region of the world with 15 manufacturing sites, six engineering and 14 customer service centers strategically located in North and South America, Europe and Asia. Nexteer Automotive’s customers include GM, Fiat, Ford, Toyota, Chrysler, and PSA Peugeot Citroen, as well as automakers in India, China and South America. In this interview, Matthew Beecham talked with Laurent Bresson, Nexteer Automotive’s executive director in Europe and executive director of its global sales and marketing operations.
just-auto: I’d like to start by asking you to talk us through Nexteer’s roadmap for its steering systems. I guess fuel efficiency, packaging, complexity, quality and, of course, cost considerations must all be taken into account?
The main evolution in steering is the switch to electrical power steering (EPS). There’s a real revolution underway. The pressure to increase fuel economy and reduce emissions is what is driving vehicle electrification and EPS is a key technology that is helping automakers meet new CO2 requirements. Removing a hydraulic steering system’s drag on the engine and replacing it with an on-demand electrically powered system reduces fuel consumption which corresponds to 5 to 6 grams of CO2 per kilometre. This can account for up to 25% of an automaker’s CO2 reduction target for 2015.
Nexteer Automotive already has the broadest portfolio of EPS architectures of any supplier and is the only EPS specialist with production experience in every passenger car segment and systems suitable for every kind of passenger car from A-segment city cars to luxury limousines and SUVs. We are in a strong position and we expect advances in our technology, combined with our ability to support global customers, to help manufacturers to introduce EPS in an even greater range of cars and light commercial vehicles.
The market wants more cost-efficient and reliable systems that are easier to package. There are still some quite large systems out there that are quite a headache to fit under the hood. Car manufacturers also want higher performance in terms of loads as they work to put the technology into larger vehicles where the fuel economy benefit is needed most.
Nexteer Automotive produces its EPS systems at highly automated facilities in best-cost locations. In Europe, 100% of our production already comes from best-cost countries. We have invested more than $40m in its Polish facilities in recent years – our factory in Tychy that supports the Fiat 500 and Citroën C3 is state-of-the-art. We have invested a similar sum in Mexico.
How well do you really know your competitors?
Access the most comprehensive Company Profiles on the market, powered by GlobalData. Save hours of research. Gain competitive edge.
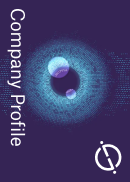
Thank you!
Your download email will arrive shortly
Not ready to buy yet? Download a free sample
We are confident about the unique quality of our Company Profiles. However, we want you to make the most beneficial decision for your business, so we offer a free sample that you can download by submitting the below form
By GlobalDataOur steering systems combine compact packaging, competitive costs, outstanding NVH quality and feel. We strive constantly to reduce complexity. A good example of this is the polyamide eccentric rack bearing that our engineers have developed. It replaces traditional yoke-style bearings that use a spring-loaded bushing. Doing away with the spring-loaded parts makes the steering system quieter, more durable and easier to package. It also reduces friction, improving steering feel.
Nexteer also takes a modular approach to its design, development and manufacturing; not all suppliers do. Regardless of the system architecture, we use the same building blocks: the same worm gear, basic motor design and electrical control module for all applications. This ensures that all our processes are highly standardised and stable. Our software engineers’ tuning of the system is what makes the difference, creating the features and functions that end-users want.
just-auto: In the early days of EPS, customers and reviewers criticised the poor steering feel, especially vagueness around the centre position. I guess these issues have now been cleared-up?
That vagueness around the centre position is the result of poor control of the play between the parts, but this is an issue that Nexteer has long since overcome. The clearance and friction between the system’s worm shaft and gear is critical.
To control this, most suppliers spring-load their parts, but these can then resonate and create NVH problems. Instead of adding mechanisms, Nexteer uses precise design and manufacturing processes. Our fine control of the tolerances and the mesh is a competitive advantage.
Advances in electronics in recent years also make it possible to introduce systems that can provide additional steering torque as necessary. They can take into account environmental factors such as side winds and road surface imperfections to deliver even better on-centre feel.
just-auto: As I understand it, Ford is increasingly using electric steering in its models not just to enhance driving comfort and improve fuel economy but open the door to driver-friendly features such as parallel parking assist. Could electric steering technology act as catalyst for a number of other driver-enhanced features? How do you see the market evolving?
There are a lot of benefits for drivers in pairing camera technologies with electric power steering systems. If you want to automate low-speed manoeuvres such as parallel or perpendicular parking, electric power steering is essential.
There is increasing demand for high-speed driver assistance too. Lane-keeping assistance, which uses a torque overlay from the electric motor, is just the first step in a direction that is leading us towards fully automated convenience and safety functions. Luxury manufacturers have introduced automated emergency braking and this will become mandatory in the next few years. If the car has electric power steering, then it will be eventually be possible to introduce evasive steering manoeuvres too.
All this creates a lot of additional software development work for the OEM, however. Nexteer has kept its software development in-house and this will be a considerable advantage, allowing OEMs’ own software engineers to focus on functions that are more visible to their customers.
just-auto: I guess EPS systems are pushing hydraulic steering-assist systems off the road. How do you see the hydraulic steering sector evolving over the next few years?
Nexteer has decided to focus on EPS for good reason. The general trend is that vehicle systems are electrifying so that any energy consumption is on-demand and fuel consumption is lower. And people want more electronic functions that make driving easier and safer – the precise control and swift response that these require make EPS essential.
It’s safe to say that the role of hydraulic steering will diminish steadily in the coming years. It still has a slight unit-cost advantage over EPS, but its efficiency penalty is a disincentive. The recycling of the fluids is a headache too.
just-auto: If EHPS systems are a bridging technology, the question is how long do you define that transition period? Will that period reach into 2015 or 2020 or will it end in two years time? I guess it depends on the platform that you have been introducing that technology?
That’s really a question for manufacturers who can better explain why they might use the technology. Electro-hydraulic power steering systems use an electric motor to drive the hydraulic pump, which drives a conventional steering gear.
Of course in the past our engineers experimented with using electric motors to power the hydraulic pump, but we discovered that we didn’t need to compromise.
When the basic mechanical design is sound, using the electric motor to drive the steering gear gives you more direct steering feel and packaging is easier. If you then combine a modular approach to the development with best-cost manufacturing, the cost, efficiency and functional benefits of an EPS system are greater no matter what the application or segment.
just-auto: What is the interest in EPHS systems for hybrid vehicles?
We are registering no significant interest in electrically powered hydraulic steering electrically powered hydraulic steering for hybrid vehicles. The people with whom we speak at the 60-plus vehicle manufacturers around the world are far more interested in EPS.
For those developing hybrids and electric vehicles, we’re seeing particular interest in our column-mounted EPS systems. They have exceptionally low NVH characteristics, operating at less than 35db – considerably lower than the industry average of 40db.
Most manufacturers are looking for technologies that can work on platforms that produce hybrid and non-hybrid variants. The packaging requirements are tougher and the greater range of front axle weights tends to favour EPS because fine-tuning the steering feel is far simpler than a hydraulic system. Sat in the passenger seat of a prototype vehicle with a laptop in a few minutes our engineers can make changes that would take a hydraulic steering systems engineer months.
just-auto: Is there an appetite for expensive EPS in emerging markets such as Eastern Europe, India and China? I guess in terms of functionality then I would presume that that there is. However, I would imagine that you have to consider the robustness of the application and the workshops in the different emerging markets and whether or not electric components might be a challenge for the workshops. How do you see this application being used in emerging markets?
Cost is obviously an important factor in such markets. The situation there is quite volatile – vehicle portfolios and emissions regulations are changing rapidly, especially in China. Consumers there want the latest technologies and the same comfort and fuel economy that the rest of the world enjoys – we expect the conversion to electrical power steering to occur more quickly than in Europe.
The development of low-cost EPS will be a key factor in the evolution of power steering in emerging markets. Requirements in some emerging markets are lower than in Europe, which allows us to develop smaller, lower cost motors.
We have a technical centre in Shanghai and manufacturing facilities in China that will start production of EPS in significant volumes there by the end of this year. A lot of our growth is driven by the expansion of global OEMs there. They want the same performance in terms of cost, quality and service they get in other regions. Nexteer is well positioned with a global development infrastructure and local production.
just-auto: Some analysts estimate that by 2015, we could expect the European steering market to see fitment rates of 25-30% HPS 55-65% EPS and 5-10% EHPS. How do you see the market growing over the next five years?
The next five years are going to be a period of transition. The A-segment has already converted to EPS. There’s still some growth potential in the B-segment and there will also be a second wave of conversions in the C-segment. The transition will be slower in the D and E segments and in SUVs. It will take some years, but it will happen.
It’s hard to make precise predictions for 2015. Ford recently announced that EPS would be on 90 percent of its vehicles by 2012. The technology’s total market share is unlikely to be so high, even by 2015, but it’s really just a matter of time.
The drive to increase fuel economy and reducing emissions is driving vehicle electrification and EPS will become the steering technology of choice in the next decade. Automakers are increasing the number of driver assistance systems such as lane departure warning, parking assistance and speed-sensitive steering. EPS is the key to giving vehicle platforms the flexibility to add these technologies.
just-auto: As we see it, steer by wire is still an advanced technology with limited application potential. Sure, you can prove and realise all sorts of advanced features with it but to bring it into the vehicle will cost the OEM an immense amount of money. So I guess the question here is: will the end customer be willing to pay for it if he/she could get nearly the same functionality with an AFS and EPS combined?
You’re right. The challenge with steer-by-wire is the need for obsolescence in the system. If you must fit a back-up system, you soon lose the packaging and cost advantages of steer-by-wire. I don’t see why the end-user would be willing to pay a premium to make packaging easier for the manufacturer. The benefits that they will be prepared to pay for come from linking EPS to other vehicle systems via the software functions that we can add.
One alternative theory is that car manufacturers could use EPS systems’ torque overlay functions to provide active or artificial, instead of a natural return in their steering. This could help them to take a more simplified approach to chassis development, where they spend less time on the architecture and the fine-tuning of the wheel and caster angles, resolving the issue in the software. OEMs haven’t explored this yet, but they will in time.
just-auto: What is next for steering systems? We’ve seen how your EPS system has become very popular among automakers. Technically speaking though, what’s in the pipeline, i.e. next generation?
Nexteer invests 8% of its revenue straight back into R&D and has some very exciting developments in the pipeline. Some are incremental improvements: we are rolling out a thermoplastic coupling, for example that we have developed to improve the NVH performance of our systems. And we have developments that will significantly improve our systems’ cost, torque density and packaging. I can’t go into details, but they will help manufacturers improve dynamics, feel and refinement as they meet challenges such as the introduction of electric and hybrid vehicles.
just-auto: Are there other approaches being developed that use advanced electronic techniques? What about rear wheel steering perhaps supplemented by ultra-capacitors coupled with improvements in sensors, power and control?
Unlike other EPS suppliers, Nexteer Automotive electronics and software development is entirely in-house, and this represents a major competitive advantage for us. We’re also the only steering supplier with complete integration of its systems, which gives us optimal control of the overall system and lets us be more responsive and better able to fulfill our customer’s needs.
It also allows us to develop and apply additional safety and comfort features such as Lane Keeping, Park Assist or Pull Compensation. We’re developing functions that take advantage of more sophisticated electronic architectures such as Flexray, but the bulk of our electronics expertise still centres on individual applications.
And because our software development is modular, just like the hardware we’re continuously feeding the lessons, ideas and functions developed for new applications into our base system. It means that with each project, our EPS improves, the speed of development increases a little and the end-user experience gets better.
The idea of adding technologies such as rear-wheel steering to improve the user experience on some models is attractive, but our priority is to help manufacturers to get the set-up right for the base model, faster and more cost-effectively. As they introduce the technology on a greater range of vehicles, that’s how we can be most useful.