Acoustics in vehicles used to mean stuffing as much insulation as possible into a door panel to make the interior quiet. But now, of course, the accent is on making a statement about a car’s quality. In this interview, Matthew Beecham talked with Matthias Kroll, managing director of the Isolite Group about some finer points of thermal and acoustic insulation for a variety of car parts.
The European Union is calling for more stringent limitations on the noise emissions of motor vehicles. What is the current and future potential of high-temperature insulation systems with regard to acoustic insulation?
Depending on the method used, the current potential of acoustic insulation is between one and four decibels per vehicle. Using a fully acoustic method, we can even achieve a reduction in noise emissions of up to six decibels. Here, all the components containing hot gases as well as the facing of the engine are equipped with acoustic insulation. Of course, a further reduction of more than six decibels is a question of cost too. However, thanks to new manufacturing technologies and changes made to the perforation of the lining, we have the ability to design an improved acoustic insulation with less effort. We can thus offer modern insulation solutions at a reasonable cost.
In addition to the acoustic insulation, thermal insulation plays a crucial role, for example with exhaust gas aftertreatment. To what extent do insulation systems support the reduction of harmful NOx emissions?
For thermal insulation, we have developed the REF-ISO fibre skin technology. By systematically admixing colour pigments, we can vary the reflective and insulating properties of the insulating skins. In addition to protecting the surrounding components by means of heat absorption, the fibre skins reflect the heat radiation back into the exhaust gas stream. In this way, the optimum operating temperature is reached more quickly. As a result, both fuel consumption and NOx emissions are reduced. In terms of diesel vehicles equipped with an SCR catalytic converter, all of the components up to the urea injection are insulated. This leads to an increase in exhaust gas temperature of about ten percent compared to non REF-ISO coated insulating skins.
How much future potential do you see in thermal insulation solutions in terms of emissions reduction?
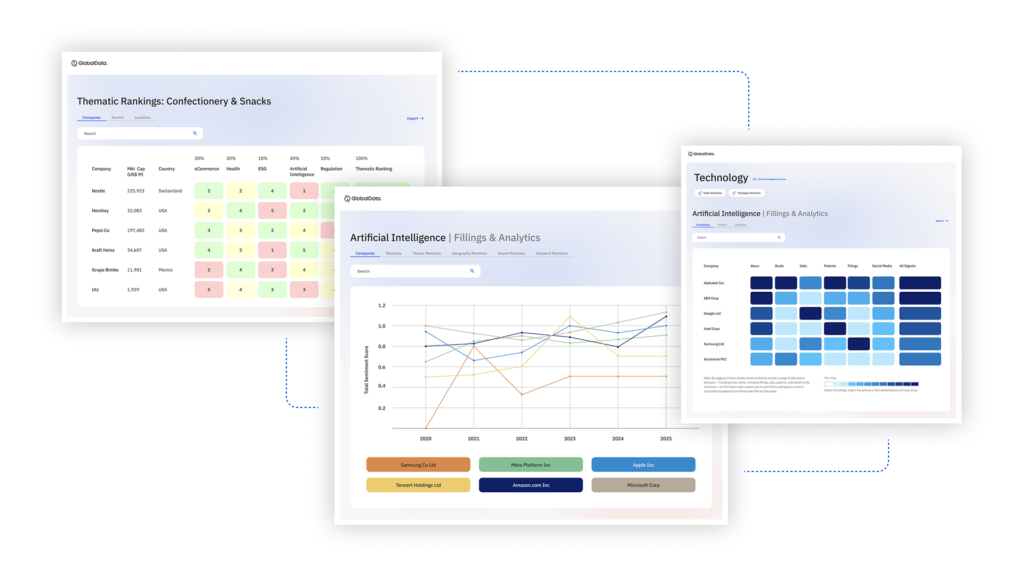
US Tariffs are shifting - will you react or anticipate?
Don’t let policy changes catch you off guard. Stay proactive with real-time data and expert analysis.
By GlobalDataWe distinguish between primary and secondary measures. Secondary measures are related to the protection of the surrounding components while primary measures keep the exhaust energy inside the exhaust gas stream. Our fibre skin with REF-ISO coating, which is mainly used with diesel-powered vehicles, is the state-of-the-art technology at present. In a recent project, we were able to reduce fuel consumption by 3.5 percent and reduce NOx emissions by 20 percent. However, we still see further potential for reducing emissions by means of modern insulation systems.
Which other applications apart from the exhaust system are possible and reasonable? What about acoustic and thermal insulation of the entire engine block, for instance?
In the course of a project concerning engine encapsulation, we came across the insulation of components containing hot gases. Encapsulation of the entire engine led to overheating of the engine. For this reason, we started focusing on the exhaust system, and we spotted the acoustic potential by using the insulating skins as a noise absorber too. The surface has been provided with a micro perforation which effectively absorbs the acoustic energy. The thermal and acoustic insulation of the components containing hot gases, including the turbocharger and the entire exhaust system, is a reasonable and cost-effective alternative to the encapsulation of the entire engine block.
How do you achieve an insulation which is as precise as possible?
Depending on the design of the outer liner (metal-like outer sheath) – i.e. diameter and position of the void – we can precisely adjust the insulation, thus adapting its thermal and acoustic properties according to each customer’s specific demands. Omitting particular sections is also possible. For instance, the underbody is a critical area in terms of penetration by moisture. By positioning the void at the right place, i.e. at the top or bottom of the perforation, we can precisely and individually adjust the frequency range that needs to be absorbed. In addition, our patented manufacturing technology allows each insulation product to be adjusted customer-specifically, thus ensuring an insulation which is optimal at all times.
Isolite XP is a new technology. What are the characteristics of this material?
Isolite XP is an advancement based on a silicate fibre skin insulation which also has acoustic potential. The specific characteristic of the material is its volume increase of about 30 percent when first heated. Due to this “popcorn” effect, more air can get inside the insulation body, and this decreases the thermal conductivity and supports the thermal effect. In addition, the outer liner gains an excellent inherent damping thanks to expansion, leading to a significant increase in the material’s overall acoustic performance. The main benefit of this for the customer is optimised insulation at no additional cost and with a shortened production time.
How do you achieve the high and durable temperature resistance of the insulation materials?
Since 1978, Isolite has been developing insulation systems focusing on internal use in the fields of aerospace, industry and power plant construction. As a result, we can draw upon an extensive expertise and a diverse selection of materials with high-temperature insulation solutions. For example, these materials are used for the internal lining of gas turbines. In addition, the insulation systems are applied to the low-pressure turbines of Airbus (A318/A380) and Boeing (757/767) as an internal insulation system. We are currently the market leaders in the automotive field as well as aerospace and industry in terms of internal insulation system solutions. Of course, the products meet all applicable standards, such as ISO/TS 16949 in the automotive sector or EN 9100 in the aerospace sector.
As we understand it, you currently offer both permanently installed solutions (integralliners) and blankets that can easily be disassembled and reassembled at the respective component part directly on the OEM’s assembly line. What are the benefits of the blankets compared to the integralliners, and how do they differ from each other in terms of acoustic and thermal properties?
Integralliners are the ideal solution in terms of heat protection and thermal preservation. Here, the exhaust gas component parts are supplied to us; we apply and weld the outer liner and then forward the isolated component part just-in-time to the OEM. However, the increasing relocation of production, for example to Mexico, makes this process increasingly unprofitable. To allow us to continue offering cost-effective solutions, we have developed the blanket construction. The blankets are adapted to the component part in question at our plants in Ludwigshafen or Greenville only once. The final blanket design then allows the assembly of the blankets directly at the OEM. For this purpose, we provide automakers with a complete mounting device that can be integrated into the existing assembly line. This “full service” contributes to cost savings because the component parts can be insulated on site without any negative effects on their thermal and acoustic insulation characteristics.
The integral pipe is a complete solution comprising component part design and insulation. You speak of the effects of synergy in this context; can you tell us more about that?
If we look at production costs, it definitely makes sense not only to insulate components containing hot gases but to take over the entire design of these components. As a result, the customer gets a tailor-made and perfectly insulated component from one source, which of course helps to save costs. In a recently completed reference project, we achieved cost savings of EURO 5 per component part thanks to the effects of synergy. This represents a total cost reduction of about ten percent.
When talking about the car of the future, the majority of automakers focus on the silent and emission-free electric drive. Are you prepared for this development?
For more than 15 years now, we have been actively participating in research projects in this field. For example, a battery needs an effective thermal insulation. We are currently working on projects concerning the acoustic insulation of electrically driven engines too. In addition, our insulation systems are already in use in both hybrid vehicles and fuel cell vehicles. Effective thermal and acoustic insulation solutions will thus be necessary with future powertrain concepts too.
Your headquarters in Ludwigshafen on the Rhine in Germany were expanded last year. In addition, a new manufacturing and distribution facility has been opened in the US. What is your future growth strategy, for example regarding the emerging markets of China or South America?
The remainder of this interview is available on just-auto’s QUBE research service