New types of contingency planning are required if expensive supply chain failures are to be avoided. just-auto talked with Brad Brennan, managing director of Evolution Time Critical, a leading emergency logistics specialist who has been analyzing this new challenge. Here, Brad recalls how his company has carried out some “hairy jobs” over the past year to keep certain vehicle assembly lines running. When all else fails, he says, it’s a combination of rigorous planning, local knowledge and creativity.
just-auto: Emergency Logistics is a rapidly developing area. How do you define it?
Brad Brennan: If a vehicle manufacturing line has to be stopped because of a shortage of parts, the cost can be up to €1 million an hour. Often the only option is to get the parts there on time, and occasionally that takes a minor miracle. That’s what we do in emergency logistics. Some of our clients have exceptionally well managed supply chains, with failure rates as low as 0.2 percent. We work within that 0.2 percent, getting the components to the line on time when every conventional technique has failed.
just-auto: That sounds like an impossible task. How often can you meet the required timescales?
Brad Brennan: According to our own statistics, in 2009 we delivered within the agreed timescale for 99.6 percent of commissions. Generally it is only exceptional factors such as weather or ‘acts of God’ that prevent us from meeting our schedule and we always discuss progress with our clients 24/7 so the manufacturer can plan accordingly. When we say we will meet a challenge, we really do. We’ve done some hairy jobs in 2009 and always kept the line running.
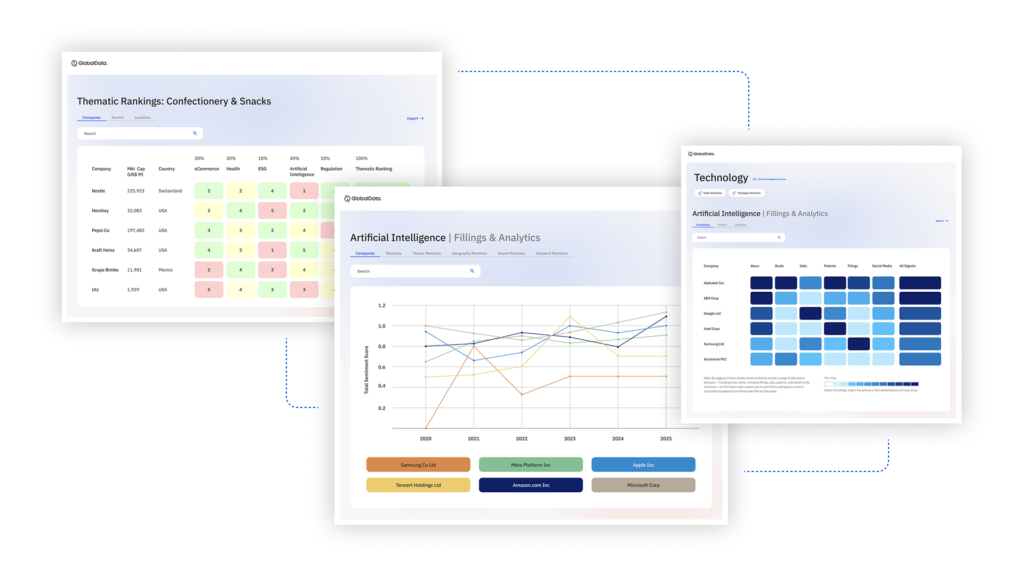
US Tariffs are shifting - will you react or anticipate?
Don’t let policy changes catch you off guard. Stay proactive with real-time data and expert analysis.
By GlobalDatajust-auto: You have said that supply chain failures are currently at record levels despite manufacturing volumes still being relatively low. Why is this?
Brad Brennan: We have clear evidence that failures are being caused by increasing production volumes pulling on already highly lean supply chains, working across infrastructures that are often also pared to the bone. Inventory reduction means that even small failures are now critical and increasing route consolidation (fewer ‘milkruns’, but each covering more pick-ups) means that the impact of failure is often more wide ranging. Shortfall volumes can be substantially higher and often cover several product types, which changes the type of solution needed.
Failures are also being caused by the unfortunate closure of some component suppliers and the related need to establish new suppliers. We have been asked to help transfer work in progress and production machines to new locations with just a few hours notice, often covering many thousands of miles.
just-auto: How can vehicle manufactures reduce the number of supply chain failures?
Brad Brennan: I’d say that vehicle manufacturers are generally very good at preventing failures. Considering how lean and how extended their supply chains are, their robustness is a considerable complement to their logistics staff. What they do need to look at is contingency planning, and this should go right back to their supply chain strength analysis.
just-auto: Have the requirements for contingency planning changed?
Brad Brennan: Yes, very much so, but our experience is that although the requirements have changed, in practice the vehicle manufacturers and first tiers are relying on contingency planning techniques that are no longer sufficiently robust to provide guaranteed on-time delivery. The issues I have highlighted mean that supply chain strength analysis has to be much more rigorous, looking for new types of failure with a different level of impact. They should then take another look at the types of contingency solution they are relying on.
One of the biggest problems is a scenario we call ‘second level failures’, where the planned emergency solution cannot be implemented. Asking one level of ‘what if’ is no longer enough because in today’s highly leaned infrastructures we can’t rely on the fall-back solution always being available.
just-auto: Can you give an example?
Brad Brennan: We recently solved a problem for a manufacturer who had identified an issue with a large quantity of components needed to maintain production. They had tried to implement their traditional contingency plan of air charter, but that day all the spare capacity in the region had been booked by a vehicle manufacturer with a pressing ramp-up problem. The only solution they had been offered was to wait for an aircraft to reposition from an airport several hundred miles away after completing another delivery, adding a further four hour delay.
just-auto: In a situation like that, what do you do that a normal express delivery service couldn’t?
Brad Brennan: It’s mainly a combination of rigorous planning, local knowledge and creativity. Our analysts are available 24/7 and will start implementing a solution within 15 minutes of getting the call. It might involve finding someone who can open a warehouse at the weekend, or knowing a small private airport where a light plane can be chartered and customs cleared quickly. Knowledge of local business practices is also important, particularly as low-cost manufacturing is moved further into regions where commercial practices and infrastructure are still developing. And we always prepare several steps ahead, having a light van or a helicopter waiting, or a local language speaker standing by in case there are issues to resolve.
To solve the second level failure in the example above, the Evolution team agreed the arrival rate of product needed to maintain uninterrupted production and implemented a dual-mode solution to contain the overall cost. A light aircraft was available at a smaller airport, so this was immediately chartered to carry a small batch of components that would increase the time window available for the main shipment to arrive. A double-manned truck was then organised to deliver the balance of the shipment.
just-auto: Suppliers often say that they could be more effective if they were more tightly integrated with their clients’ planning. Do you feel the same?
Brad Brennan: Some of our clients are making significant savings by integrating emergency logistics with their lean strategies for the simple reason that the better your contingency planning, the bigger the risk you can take with inventory reduction and supplier strength. Similarly with infrastructure knowledge. Recent consulting projects include providing expert opinion on regional transport suppliers, the development of plans to support the transition between component suppliers, and the identification and elimination of supply chain weak links.
I also encourage vehicle manufacturers to look deeper into their supply chains. We are receiving an increasing number of commissions from first tier companies who can’t make deliveries because they can’t get components or materials from their suppliers. Making a high level of supply chain analysis available to these businesses could help to avoid these situations, or to resolve them more quickly and with less cost.
just-auto: What are the characteristics of your business that have helped make it successful?
Brad Brennan: I’d point to two areas. First, we have a nine year focus on the automotive industry, which gives us knowledge and insight that is of significant value to our clients, helping us to find solutions that may be overlooked by less specialist providers. Second, we are creative, using that knowledge to develop often quite unusual solutions.
We are also financially very stable, which gives our clients confidence and allows us to implement solutions that might require significant up-front payments. When emergency logistics is your last option, the most reliable solution has to be a provider that can always deliver the best service without any financial constraints.