Dow Automotive Systems is a provider of polyurethanes, elastomers, films, fluids, adhesives, emissions solutions and acoustic-management materials to the global transportation industry. That includes supply to OEMs and Tier 1 suppliers for automotive applications in interior, exterior, under-the-hood, body-in-white structural, acoustic and thermal management, and powertrain. Here, Matthew Beecham talked with Eugenio Toccalino, Director of Strategic Marketing, Dow Automotive Systems.
A clear trend for decades has been for lighter weight cars. Could you talk us through an example technology / process offered by Dow that helps OEMs achieve that weight reduction?
At Dow Automotive Systems, we have many different technologies that enable significant lightweighting in series production. For example, our structural adhesives have enabled structural/crash durable assembly of metal structures since the 1990s. [Our] Betamate structure adhesives enable OEMs to down gauge sheet metal; combine dissimilar materials without galvanic corrosion and with increased durability; and improve noise, vibration, harshness, ride and handling.
With this technology largely established in the OEM body shops and repair environments, we see now a significant growth of room-temperature-cure structural adhesive for the assembly of composites or dissimilar materials.
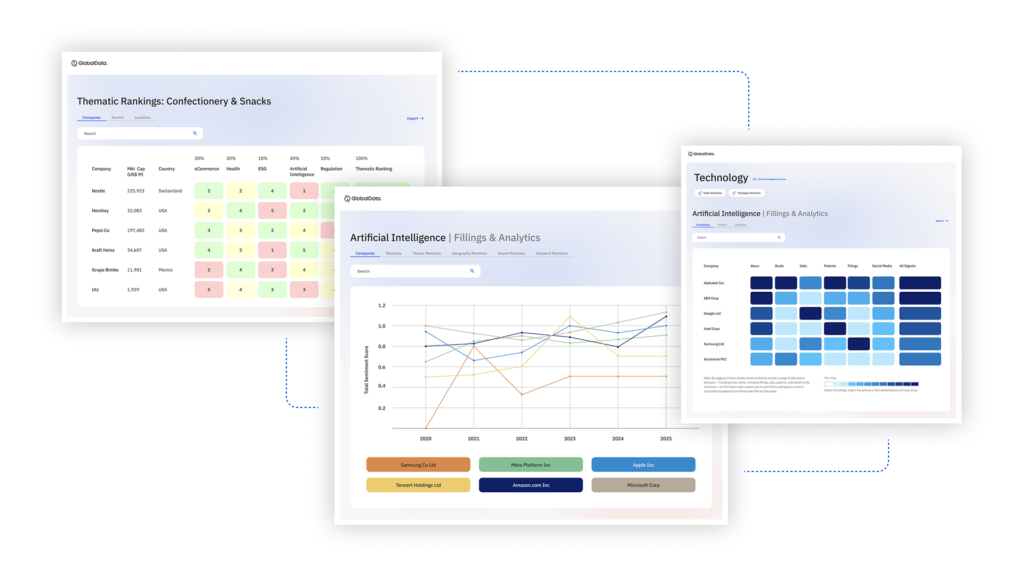
US Tariffs are shifting - will you react or anticipate?
Don’t let policy changes catch you off guard. Stay proactive with real-time data and expert analysis.
By GlobalDataWe also offer a formulated thermoset resin that is specifically developed for carbon fibre impregnation and capable of <2min cycle time even for large and complex part production via resin transfer moulding process. We are very familiar with the challenges and opportunities that exist throughout the production process and have developed products that work well together to support mass decompounding which facilitates the lightweighting of an entire vehicle rather than just a few select areas. All of these technologies can be used alone, although the maximum benefit comes when we can work at the interface to ensure the most durable assembly with minimum or no pretreatment.
We know that under-the-hood trends require high-performance, cost-effective thermoplastics. Downsized engines, reduction of overall car weight and increased importance of electro mobility has brought about this trend. Could you draw on an example of the way in which Dow can support this trend?
The powertrain dynamics favor smaller displacement-direct injected-turbo loaded combustion engines, increasing energy density and therefore driving up temperature and shifting the noise towards higher frequencies. Beyond common interior acoustic solutions, there is a more marked trend towards acoustic insulation placed directly at the source. To address this trend and support a more quiet and comfortable driving experience, Dow Automotive is formulating low density/high productivity Specflex polyurethane systems with specific acoustic/temperature and chemical resistance for engine compartment applications like hoodliners or valve-engine covers.
To what extent are bonding solutions – such as direct bonding with silicone – taking over from conventional fastening applications such as fixing screws?
The use of adhesives to achieve robust assembly continues to become an alternative to conventional fastening technologies. Already, all direct glazing is possible through elastic adhesive solutions complemented by specific surface preparation and adhesion promoter technologies like cleaners, primers and activators. Our Betaseal glass bonding systems are modified to enable panel or dissimilar material assembly in the trim shop (room temperature cure) and are key for the aftermarket (e.g. glass replacement).
We mentioned already the continuous growth of structural assembly in body, trim and repair environment driven by lightweighting, stiffness/NVH/durability and corrosion requirements, turning adhesives not only into an advantaged, but an essential solution when it comes to dissimilar material assembly (management of corrosion and differential coefficients of thermal expansion.).
We are seeing increasing applications of alternative powertrains such as LPG (liquid petroleum gas) and CNG (compressed natural gas). In what ways have you developed high performance materials for these applications?
Dow has developed and commercialised specific Voraforce resin grades for filament winding of lightweight CNG pressurised tanks.
In what ways has the US shale gas revolution put pressure on Europe’s polymers industry?
A clear signal is the reopening of the discussion around the need to objectively assess shale gas exploration and extraction in order to maintain and secure the competitiveness of the investments in Europe. These discussions are coming from coming from some of the highest representatives of the chemical industry.