In this interview, Matthew Beecham talked with Steve Kiefer, vice president Delphi and president Delphi Powertrain Systems and Prasad Kadle, director of advanced engineering, Delphi Thermal Systems about the clever ways in which Delphi designs its systems to ensure that CO2 is affordable.
In terms of fuel injection, I believe that Delphi is using a solenoid diesel fuel injector as a route to reducing the cost of risk by improving technologies rather than introducing new technologies. Have we got that right?
Steve: Yes. If I can start by talking a little about our diesel common rail offering. Delphi does have servo-solenoid and direct acting piezo based products in the marketplace today. Using our solenoid products, we aim to solve the fuel economy, emission and performance equation at the lowest possible cost. And we see the opportunities for a very high performing solenoid based injector to become the optimal solution.
How do you do that?
Well, our heritage is as a systems supplier. We design all of our products with the total cost of vehicle integration in mind. That means we are designing, for example, our common rail injection system such that our common rail, injectors, high pressure pump, controls and software are an integrated solution where innovative thinking can lead to both performance improvement and cost reduction.
Why is that important?
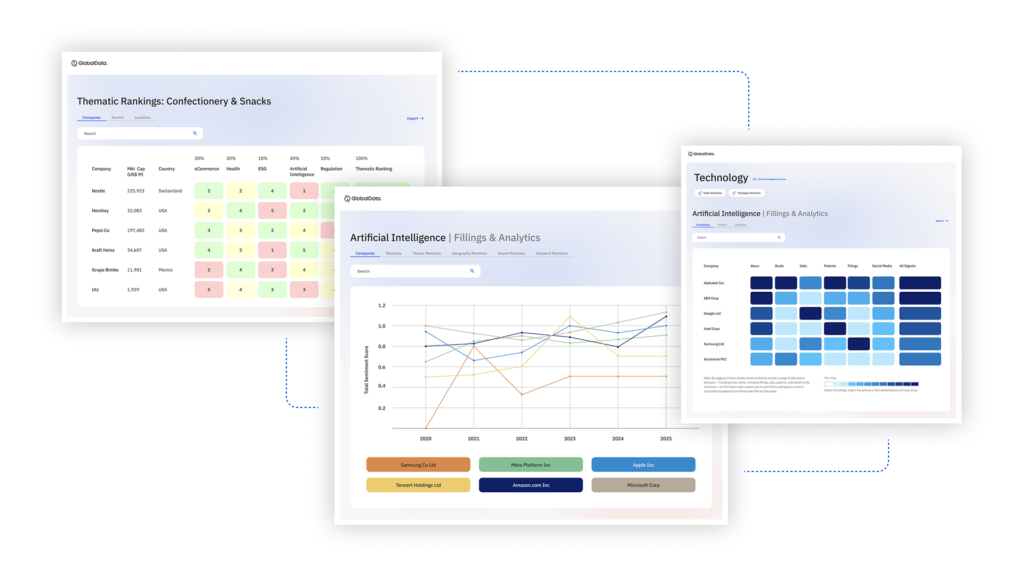
US Tariffs are shifting - will you react or anticipate?
Don’t let policy changes catch you off guard. Stay proactive with real-time data and expert analysis.
By GlobalDataI guess that’s typical of most of our competitors but I think we have several innovations that set Delphi apart. In essence, with our expertise in electronics, software and high performing electromagnetic systems, we have developed a very high performing solenoid injector. In other words, a solenoid with fast opening and closing to achieve an affordable package with response times that are equivalent to a conventional servo-piezo system.
Most of our offerings use high pressure common rail systems based on solenoid injectors. We advertise it as the fastest solenoid in the marketplace which is suitable for Euro 6 although we believe it has opportunities for emission standards beyond Euro 6.
Am I right in thinking that Delphi has developed a new high pressure fuel pump which, although the pump itself is quite expensive, allows the system to be substantially simplified? Could you explain how that works?
You have got it right. I would call it a high value pump. It is actually referred to as our DFP6 pump which is currently in production and I would say it is a Euro 5, Euro 6 solution that is high performing and compact in the sense that it is easy to package. It also really reduces the cost and complexity of the overall system so although the component may be a little more pricey than the lowest cost solution, the overall system cost can be significantly lower and of course the performance will be higher too.
In addition, we have some derivatives of our unit products for medium duty and heavy duty markets where we’re helping engine designers move to common rail without changing the architecture of their cylinder heads.
Another area that we would like to talk to you about is the role of electronics and software control. I believe that Delphi has looked at how putting more intelligence into software you can reduce development times and increase flexibility. Is that correct?
Yes. When a customer buys a complete system from us, our system software has modelbased controls which shorten the development, calibration time and cycle times to put those products into production. We then weave in some clever and innovative ways to control our injectors in order to get more performance out of the hardware through innovative software. Let’s take, for example, our injector specific characterisation that we use in diesel to highlight the point. Here, we characterise each of our solenoid injectors at the manufacturing plant with a fuel calibration curve that’s programmed into our controller. This allows us to tolerate some level of variation across our injectors but the engine will never see that variation. So basically the controller absorbs it because the device has been calibrated with a flow curve for each unique injector. That is a production feature we offer to help improve performance of the overall system using our products and software.
In terms of downsizing engines, we believe that Delphi provides the fuel injection system for the VW Polo 3 cylinder Blue Motion car. I guess this is an example of an affordable car with low CO2 technology?
We are very proud of that application. It was introduced with our Delphi solenoid common rail system. And, for a time, was the lowest CO2 vehicle in the European marketplace at 87 grams of CO² per kilometre.
In terms of Stop-Start systems, I believe that Delphi is developing a Phase Change Material Evaporator that aims to keep the cabin of a start-atop vehicle cooler for longer, which we could see on the road in 2014. I guess this is another example of ways in which to reduce the cost of CO2 reduction?
On technologies such as start/stop, EGR, turbocharging and injection systems, Delphi has become the enabler. For example, on a start/stop system, the generator starter is the device that allows the start/stop but of course there are several engine management functions that are required to efficiently and cleanly restart the engine so that the driver barely notices the event. These functions are part of our engine control and fuel injection strategies.
There is also the challenge of allowing the engine to be in the off mode during stop-start operation and not impact the comfort of the passenger compartment. That is the evaporator you mention that Prasad can comment on.
Prasad: The evaporator is a very neat device and we believe it is the only one of its type that will fit in an existing packaging volume, so saving on modifications to existing structures. When a stop-start system stops the engine, the traditional engine-driven air conditioning compressor stops too, allowing the cabin to warm-up. This can be solved by using an electric pump compressor, but that is an expensive solution and may require the fitment of a bigger and heavier battery. Our solution is to integrate a phase change material into the evaporator so that when the compressor is stopped, this material absorbs heat to keep the cabin air cool. Careful positioning creates a thermal siphon, so circulation is provided without a separate pump.
Also, there is a notice of proposed rulemaking by the EPA which gives a credit of 2.9 grams of CO² per mile for start/stop for passenger vehicles and 4.5 for light duty trucks. That has led to a lot of customers wanting start/stop. [Our solution would] be a great enabler for that because if you do not have cooling you have to start your engine again just for the cooling.
Steve Kiefer is now head of GM Powertrain.