In this interview, Matthew Beecham talked with several colleagues from Continental’s hydraulic brake systems business, namely Dietrich Golz, Uwe Hendrich, Uwe Bach, Steffen Gruber and Michael Vogt.
j-a: What are the forces driving innovation in foundation braking for passenger cars and light trucks?
Continental: The objective for Continental’s development engineers is to develop lighter and low-drag braking systems using traditional materials but employing state-of-the-art development and manufacturing methods. Also, customer requirements regarding comfort are increasing rapidly.
One means of saving weight when designing brake components is to replace the materials used so far, such as cast iron or steel, with lighter materials, such as aluminium, other light alloys or even plastic. However, the use of alternative materials is currently restricted to aluminium since extremely high demands are made of these materials. During its life, a brake will be operated several million times, subjecting it to great pressure; the material is also exposed to moisture and road salt and so far only cast iron, steel and aluminium have shown that they are able to cope with such demanding conditions.
More efficient design techniques and intelligent lightweight construction can produce slimmed-down components without limiting their functionality. Specialised CAD software makes it possible to optimise component structures on the computer. Without the need for time-consuming trials using costly models, it is possible to achieve components of maximum strength but, at the same time, of the lightest possible construction. A good example is the 2FNR-Al aluminium brake calliper housing whose shape the development engineers have been able to improve using these state-of-the-art simulation and topology optimisation methods. Despite bigger recesses and reduced wall thicknesses, meaning less material is required, the redesigned housing provides the same degree of stability as the tried and tested model, but still weighs 440g less than its initial weight of 4,185g.
Brake pad back plates can also be slimmed down to some extent without limiting their functionality. The standard metal thickness used so far is 6.5mm throughout. But this is only necessary over certain areas of the plate where the greatest stresses occur. In some places, the optimised back plates are only up to 4mm thick with reinforcement provided in areas particularly subject to stress, and this can lead to the weight being reduced from 424g to 300g. For a pair of brake pads this is a not inconsiderable weight saving of roughly 250g.
How well do you really know your competitors?
Access the most comprehensive Company Profiles on the market, powered by GlobalData. Save hours of research. Gain competitive edge.
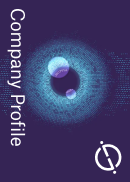
Thank you!
Your download email will arrive shortly
Not ready to buy yet? Download a free sample
We are confident about the unique quality of our Company Profiles. However, we want you to make the most beneficial decision for your business, so we offer a free sample that you can download by submitting the below form
By GlobalDataIt does not always have to be aluminium or another light alloy in order to reduce weight. An outstanding example is offered by the brake pistons, currently going into series production, and manufactured using a new process. In this process, patented by Continental, the pistons installed in the brake calliper’s hydraulic system are no longer cast or turned, but are press-formed from a 3.5mm thick circular metal blank. A total of 15 metal-forming steps convert the blank into a very thin and light, but equally very stable, brake piston which not only weighs almost 25% less than its cast predecessor but also delivers production cost advantages.
Tie-rod design brake boosters have already proved their worth. Compared with conventional brake boosters, tie-rod brake boosters – significantly more stable due to their integral steel tie-bolts – produce a 30% weight reduction. Transferring the principle behind the tie-rod design to aluminium – a development which has already taken place – produces a further weight reduction of 25%. But even with the present steel design, depending on the size and shape of the brake booster, the weight savings in absolute terms are between 150g and 1,150g – that’s a lot of CO2 saved over a vehicle’s life and an important milestone towards reducing global CO2 emissions from vehicle fleets in the years ahead.
j-a: Are those drivers the same for every car segment?
Continental: The drivers are more or less the same, but due to its high cost, aluminium is the material of choice for luxury-class vehicles, for example in a new aluminium-fixed calliper brake which our chassis and safety division has developed for a top-category premium vehicle.
But also this premium segment is meanwhile under price pressure.
j-a: To what extent do those drivers change when looking at the developing regions, such as India? For reasons of low cost and ease of maintenance, I guess the developing regions still use drum brakes. Is that correct?
Continental: Looking at the actual situation, this is correct. But considering future programmes, we believe that requirements and specifications for product development, for instance in China and India, will become the same level of requirements as already established in the specifications used in the world market.
j-a: To what extent is there a focus on providing flexible technology platforms that save time and cost for low- and medium-volume applications?
Continental: The need for flexible technology platforms is not new. But with the growing number of global platforms the importance of using worldwide existing technology platforms becomes more and more important.
Therefore our design is based on an existing construction and family kit of worldwide available and well-known components that gives us the best combination of costs and function. The target is to assure product scalability from entry car to premium class.
Because of the modular design and scalability of all the chassis and safety division’s products and systems, and with development centres and production sites throughout the world, we can react to the widest range of customer and market requirements. Our aim is both to equip small and compact vehicles with life-preserving safety and assistance systems and to install safety products in less expensive cars intended for the world’s growth markets.
j-a: In what ways do hybrid and electric vehicles change future braking system requirements?
Continental: Working in conjunction with a hybrid drive, [Continental´s Regenerative Brake System] system allows energy recovery during braking. The basic concept and the components of conventional brakes are broadly kept the same.
The generator function contained in the vehicle’s hybrid drive initially takes over the braking function and converts the braking energy into electricity to charge the battery. Only when the deceleration is not sufficient are the conventional brakes activated via the Regenerative Brake System. The SBA [Simulator Brake Actuation] simulator conveys optimum pedal feel to the driver at all times. The system is ideal for all hybrid vehicles as well as electric and fuel cell vehicles. Regenerative braking makes use of a pedal-feel SBA. This brake actuation system is based on tried-and-tested components of the hydraulic brake and offers many of the advantages and additional functions of brake-by-wire technology. While the brake command is transmitted ‘by wire’ from the pedal angle sensor, the pedal feel simulator generates optimum pedal feel. The hydraulic unit then generates the brake pressure required for the deceleration. A convenient safety circuit provides backup in the event of a malfunction.
j-a: In terms of brake disc materials, in what ways have these materials advanced over the past five years?
Continental: Continental has developed and delivered brake discs in various designs and materials or material combinations. Weight reductions up to 53% and a heat capacity more than two times higher compared to common grey iron series rotors are possible. But the remaining costs for such specific materials offer only the possibility to use them in high performance vehicles.
j-a: I guess there is a practical limit to braking performance, set by the ability of the tyre contact patches to transmit the forces involved without sliding. However, I guess advances in tyre design mean that limit is now potentially very high, at least on dry road surfaces. Is that throwing the onus very much back to the braking system developers? How will tomorrow’s brakes perform?
Continental: Having a higher maximum friction available means potentially higher hydraulic brake pressures and force levels during extreme braking manoeuvres. From system design view this can be countered by selecting appropriate wheel brake components, e.g. with bigger wheel brake cylinders. From component design view this must be countered by considering higher forces in the calculations of strength and durability, and therefore in the wheel brake design. Even the hardware and software parameters of the so-called hydraulic/electronic control unit of the brake system can be adapted to achieve the required performance.
Therefore Continental is usually requesting such boundary conditions like tyre information already in a very early project stage from the vehicle manufacturers for consideration in the full brake system design and to meet the performance targets safely.
It should not be forgotten that tyre design is always a compromise out of several attributes like dry/wet grip, rolling resistance, wear, noise, etc. Therefore it is not expected that the maximum tyre/road friction level will further increase in huge steps; a moderate continuous improvement seems more probable.
Continental Corp is a major supplier of brake systems, systems and components for the powertrain and chassis, instrumentation, infotainment solutions, vehicle electronics, tyres and technical elastomers. The company currently employs 130,000 people at 190 locations in 35 countries. The Chassis & Safety division of Continental AG is involved in the fields of active and passive driving safety, safety and chassis sensorics, and chassis components. This division develops and produces electronic and hydraulic brake and chassis control systems, sensors, driver assistance systems, airbag control systems and washer systems as well as electronic air suspension systems. The company’s hydraulic brake systems business designs, develops and manufactures callipers and discs, drum brakes, brake hoses, boosters, tandem master cylinders, electric parking brakes, pedal modules and brake pressure regulators.