One of the factors driving brake system innovation is the need to provide very fast and precise brake control without introducing drag. Yet there are different forces driving innovation for each car segment. Continuing just-auto’s series of interviews with leading brake manufacturers, Matthew Beecham talked with engineers at Brembo about such influences and technical challenges in developing brake pads and discs.
What are the forces driving innovation in brake friction materials for passenger cars? And are those drivers the same for every car segment?
All of Brembo’s research and development activities can be related to a single ‘friction system’ concept, which permeates the specific qualities of each division and business unit. According to this concept, each component (calipers, discs, pads, suspensions) is complementary to the others in optimising the braking function (the ‘friction system’ as an element that integrates all of the components), which is constantly improved in all respects, not merely in terms of pure performance but also of comfort, duration and aesthetics.
Last but not the least is Brembo’s focus field on environmental issues. That means new solutions designed to use the brake system in order to help reduce vehicle consumption and consequent CO2. For example, the development continues on new light disc concepts, particularly through the study forms, materials, technologies and surface treatments that could meet the requirements of new generation vehicles (electric and hybrid), with particular attention to the environmental impact characteristics (CO2 and particulate emission).
The joint development with innovative friction materials, complying with future legislative limits and designed for these types of disc, is extremely important. Brembo can be considered to be the only manufacturer with the in-house expertise for this type of development.
As we understand it, Brembo has developed a high performance, light weight brake system for Ferrari, known as the Extrema. Could you tell us what distinguishes this brake system from others?
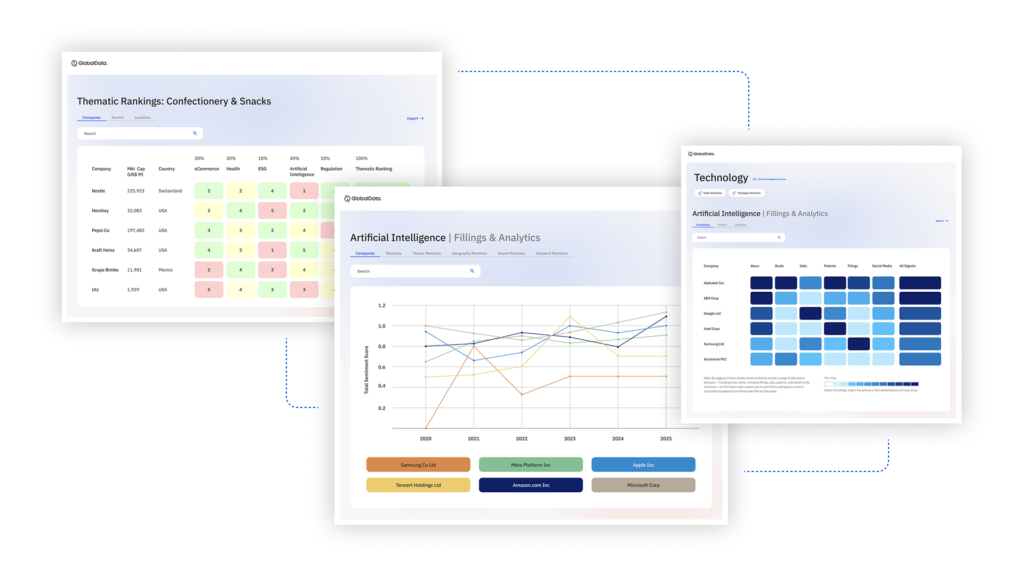
US Tariffs are shifting - will you react or anticipate?
Don’t let policy changes catch you off guard. Stay proactive with real-time data and expert analysis.
By GlobalDataThe new Extrema Brembo caliper has distinctive traits that derives from a more minimalist approach in design, appearing decidedly more exposed and hollowed out than its predecessors. An aggressive and innovative look that translates, first and foremost, into a significant reduction (more than 3 kg) of non-suspended weight and a better feel through the pedal, with less power absorbed than hitherto (10 percent reduction).
The newly designed caliper also improves ventilation, with the result that brake fluid temperature is reduced by more than 30°C.
Whilst the front wheels have a six piston caliper and the rear wheels a four piston type incorporating the electric parking brake, the two calipers are visually identical. Viewed from the side, in effect, there is no discernible difference.
For the first time in the new Extrema Brembo caliper, the electric parking brake is incorporated directly in the caliper. Thanks to mechatronics, which enables a close interrelation between different disciplines of mechanics, electronics and IT, Brembo has produced an electronic control unit and control software that manages the parking brake.
In what ways is Brembo helping OEMs to provide very fast, precise brake control without introducing drag?
A lot of activities have been done on these items with an optimisation of the shape of the calipers in order to increase the stiffness. This new design has a direct positive effect on residual torque. In parallel we have been working on friction materials and optimising some solutions on the piston side to have additional positive contribution. A ‘0 residual drag’ situation is now possible on passenger cars.
Although brake system specifications are expanding, development time-scales are not. To what extent is that a challenge for Brembo’s engineers?
Virtual and experimental simulations of all the working conditions for brake system is the way to solve this problem. Brembo is investing a lot in new facilities and tools for structural, CFD, NVH, robust design simulation and testing (new dyno benches, roller chassis dynamometer benches etc).
As we understand it, one of the main engineering challenges in any braking system are to withstand the extremely high temperatures involved, to remove the very large amount of heat generated during hard deceleration, and to minimise the weight of the braking units. Is that correct? And how can you achieve that?
This issue is very important for all cars, especially for the super sport ones, but also for more common vehicles. CFD [computational fluid dynamics] is becoming a useful methodology for the design of foundation brakes components integrated in the full vehicle. Aerodynamics depends on car shape and it has a direct effect on capabilities of the system to dissipate heat. In case of super sport cars, special components – such as air ducts and thermal insulators – have to be used. Brembo experience in racing applications is important for this item.
We are seeing automakers showing a preference for front disc and rear drum brakes on most A and B segment cars while most C segment and above vehicles tend to have four wheel disc brakes. How do you see the further application of disc brakes across these lower segments?
In Europe most of the C segment cars already has the brake disc on the back instead of the drum. As Europe represents a trend for the automotive industry, we will probably see more and more the use of this component also in other markets.
So how does that compare to the situation in emerging markets?
For the emerging markets, the technological level of the cars produced is not yet so advanced, so the use of the drum is still much widespread. However it will not take so long to have on these cars the brake disc on the rear, because of all for the needed safety requirements and to obtain the homologation in other markets.
Demands for more performance with minimal cost or weight penalties are pressurising brake system designers to come up with new ideas. To what extent are you seeing greater use of, say, carbon ceramics in disc brakes?
The carbon ceramic brake discs, for their technology and performances, are fitted on the best super sport cars in the world. Consequently, production is still contained [with] high costs. Over the next few years will see an increase of the applications. But for the large-scale production it will still take time.
With weight reduction in mind, to what extent are you seeing greater use of aluminium in disc brakes?
The remainder of this interview is available on just-auto’s QUBE research service