Motorsport specialists, BERU F1 Systems has developed new wiring technology, the so-called Wire in Composite (WiC), which aims to protect wiring assemblies from damage, vibration and environmental impact. In addition, the technology permits designers to improve packaging by laying wires securely side-by-side as opposed to a traditional bundle. Matthew Beecham talked to John Bailey, managing director, BERU F1 Systems, about the company’s proprietary Wire in Composite (WiC) technology.
just-auto: Could you talk us through BERU F1 System’s stage of development with regard to its WiC? What’s in the pipeline? What other solutions in this area are you currently working on?
John Bailey: Wire in Composite is a concept that dates back to my time in Formula 1 (F1). I wanted a wiring harness that could be securely attached to the bottom the chassis, offering better packaging, lower centre of gravity and improved durability. I also wanted something that looked good, which is critical in F1. I knew what I wanted to achieve but the project never started. Then I moved to BERU F1 Systems.
Having a harness facility and composite facility here allowed me and the team to experiment and create a concept. We started out in June 2006 with an initial prototype part. We needed to prove the technology would work. After this, the next challenge was to uncover applications outside of motorsport. We instigated an awareness campaign, highlighting the benefits; improved package, reduced vibration, increases in security, etc. In addition, we wanted to demonstrate that the technology worked in a functioning vehicle.
The project to create a wiring harness for Jaguar’s C-XF concept car showed that it could be used as a functional part as well as being highly aesthetic. This has further stimulated interest to the point where we have three research programmes across automotive and aerospace industries. We have solved the technical issues and our focus is now on improving the manufacturing capability, from a volume point of view. We will have a new composites building complete by the end of 2007, housing a new, larger autoclave. We are equally looking at different composite materials to offer more bespoke solutions or cost reductions.
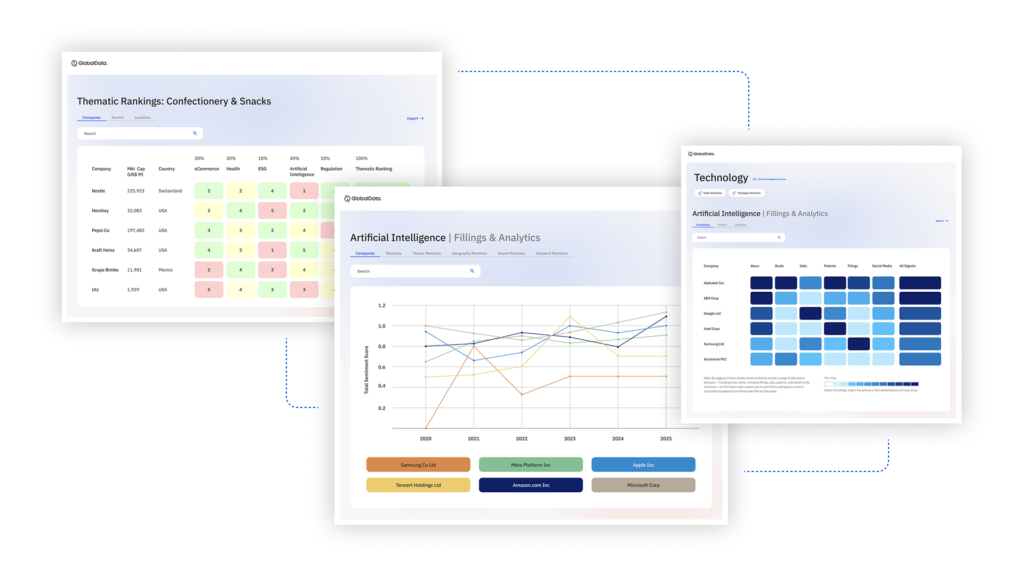
US Tariffs are shifting - will you react or anticipate?
Don’t let policy changes catch you off guard. Stay proactive with real-time data and expert analysis.
By GlobalDataj-a: How does it work?
JB: The WiC process completely encapsulates wiring by laminating it between composite materials. Parts can be built to virtually any shape or form offering the ability to incorporate sharp bend radii without the risk of strain or chafing found in a conventional harness. Highly versatile; even different wire gauges can be incorporated in a single composite component. The most complex element is the termination of the connectors, an area where much of our IPR [Intellectual Property Rights] exists.
j-a: What are the benefits?
JB: There are many advantages. Firstly durability. The wiring harness becomes inert and now has superior protection from chemical ingress, accidental damage, weather and heat. It also cannot be tampered with so there is a security advantage.
Secondly, package space reduction. Wire size can be reduced significantly due to the protective nature of composite and good weight savings are achieved. The harness can be moulded into just about any shape thus allowing designers to fit in any space.
Thirdly and of increasing interest as we develop the technology further, the wiring can be incorporated into composite structures and thus reduce the number of parts required to build a vehicle. It can become a structural element, reducing weight. From a manufacturing point of view, [the use of] fewer parts means that inventory can be rationalised, and build time on the line is also reduced as a result of this. As the wires are no longer attached separately, we can also reduce refit times, simplifying maintenance. Composite materials can be coated with a thermal barrier coating allowing WiC to be placed into some very harsh areas like under-bonnet or the HVAC system.
Finally, EMC is very easily addressed without huge expense and weight in screen bundles. Our testing in this area is offering a further advantage we hadn’t considered was going to be so strong.
j-a: Where else in the vehicle is the WiC used? What are the possibilities for its use?
JB: We cannot disclose current projects but the scope is limitless. Anywhere where space or the environment offers restrictions. From sessions we have had with vehicle designers and engineers, the technology offers a step change in thinking about harness routing. Just using it to replace existing runs will not provide all the advantages. Engineers should approach harnessing using WiC with a completely open mind. Now wiring can reliably run closer to hot components or in transmission tunnels, even through harsh liquids or with very sharp radii. The rule book has been torn up. I foresee the interior as a major area. Door modules, roof linings could all benefit from smaller, lighter wiring bundles that don’t rattle and occupy a smaller space.
j-a: When we think about the conventional wiring system architecture, presumably adding a device means adding a new wire. Or does it? Are you now seeing more and more inter-connects, which is basically protocol-based? What are the implications?
JB: I think this depends on the architecture. It is possible on most infotainment architectures to communicate with the same fibre-optic ring but these units still need power so generally more devices does inevitably mean increased wire. We do have some wireless technologies in our portfolio; tyre pressure monitoring for example.
j-a: Has the traditional wire harness loom had its day?
JB: I believe so but will take another 30 years to happen, I guess. We realise we have significant work to do in evolving the process to cope with volume production but it is very possible.
j-a: While cost pressure is surely driving the industry to more creative solutions, what other factors are driving changes in the vehicle electrical and electronic distribution systems market?
JB: Power drain and the need for higher voltages. The need to make everything lighter in an effort to reduce consumption and satisfy programme demands for lower component weights.
j-a: Although wireless systems are still costly, do you see it as playing a major role in the future?
JB: I think so. The rate of development in this area is amazing and I see this being something that will evolve exponentially going forwards.
j-a: How do you see the outlook for flat flexible cables as an alternative to conventional wire harnesses?
JB: The flat flexible solution does offer some of the package benefits of WiC but cannot compete on robustness so is a halfway house. They also have bend radius and connector restrictions that limit appeal.
See also: RESEARCH ANALYSIS: Review of electrical and electronic distribution systems