UK-based Automotive Insulations are specialists in the design and manufacture of acoustic and thermal insulation materials. Established in 1966, the company made parts for the original iconic Mini but went through challenging times when the MG Rover Group went into administration in 2005. However, a management buyout in 2006 signalled a turnaround in the company’s direction and fortunes. As manufacturers of components that reduce noise, vibration and harshness (NVH) in vehicle engine bays, interiors, underbodies and exteriors, demand for their products remains strong as automakers increasingly seek quieter and lighter vehicles. Here, Matthew Beecham talked with MD Jim Griffin about the company’s work in thermal and acoustic insulation.
The European Union is calling for more stringent limitations on the noise emissions of motor vehicles. What is the current and future potential of high-temperature insulation systems with regard to acoustic insulation?
There has been a rapid rise in temperature requirements for several exterior applications as engine designers now try to utilise smaller engines to achieve higher power output. Looking to the future, we anticipate that this increase should continue to bring higher heat requirements within engine bay and powertrain applications.
Could you give us an example of an OEM you have worked with?
We do work with JLR on their award winning Evoque SUV. We use a material developed in-house known as Xlite which is designed specifically for use in electric, hybrid and lightweight vehicles. Xlite acoustic absorbers weigh very little – up to 70 percent weight reduction in some applications – and are mouldable and weldable. Using a mismatch of coarse and microfibre structures allows the absorption of high levels of sound across all frequency ranges. The acoustic absorbers are used in the Evoque’s engine bay, interior cabin and boot.
In addition to the acoustic insulation, thermal insulation plays a crucial role, for example with exhaust gas aftertreatment. To what extent do insulation systems support the reduction of harmful NOx emissions?
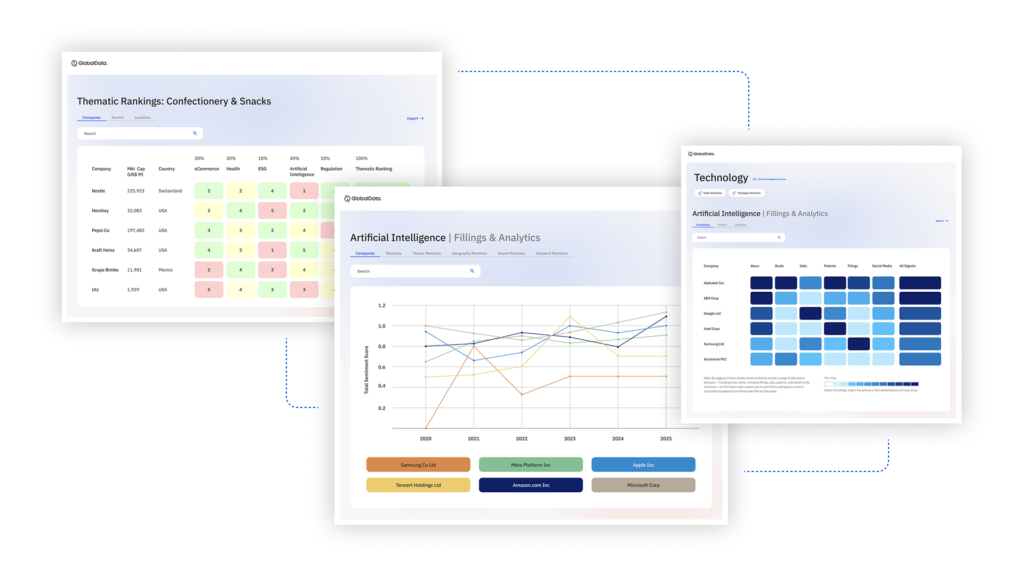
US Tariffs are shifting - will you react or anticipate?
Don’t let policy changes catch you off guard. Stay proactive with real-time data and expert analysis.
By GlobalDataAutomotive Insulations has developed high performance lightweight acoustic and thermal solutions to reduce overall component weight such as Xlite. This in turn keeps vehicles in line with current refinement standards whilst significantly reducing the weight of the insulation systems. Thermal insulation systems manage temperatures within the engine bay of vehicles which allow designers to run engines hotter without the potential thermal issues they may usually face.
How much future potential do you see in thermal insulation solutions in terms of emissions reduction?
We are currently experiencing a large push towards the development of lightweight high performance insulation systems which will help to minimise required power output, all whilst maintaining vehicle performance and refinement.
Which other applications apart from the exhaust system are possible and reasonable? What about acoustic and thermal insulation of the entire engine block, for instance?
Acoustic and thermal insulation is currently fitted to many automotive engine covers, under trays, bulkhead and bonnets. We have seen an increase of acoustic and thermal technology which is used in engine bay areas, but not directly onto the engine block.
How do you achieve an insulation which is as precise as possible?
We achieve precise vehicle refinement through rigorous product testing and a high level of production design for fitment. We also ensure tight tolerances within the manufacturing processes which ensure the part seals to the vehicle body where required. In addition, some of our customers set vehicle sound pressure level targets and interior sound quality targets. This in turn sets material performance requirements.
When talking about the car of the future, the majority of automakers focus on the silent and emission-free electric drive. Are you prepared for this development?
We have been working on this development for some years now. The electric vehicle testing that we have conducted has shown a reduction in powertrain, intake and exhaust noise, but a higher level of tyre and wind noise. These are potentially perceived as the most irritating issues for customers. By naturally achieving a reduction of interior noise levels in some vehicles, less acoustic insulation needs to be fitted. However, this can sometimes result in a higher degree of exterior sound, creating the sense that the vehicle is less refined – also giving rise to some instances of poor customer feedback. In summary, insulating an electric vehicle presents a very different set of challenges to insulating a diesel or petrol combustion engine vehicle.
We understand that Automotive Insulations recently opened its first factory in Germany. What is your future growth strategy for overseas markets?
The remainder of this interview is available on just-auto’s QUBE materials research service