Since being rolled out by the Sumerians in around 3500 BC, the wheel has been constantly re-invented, writes Matthew Beecham. Styling flexibility, reduced weight and high quality are just some of the requirements automakers expect from their wheel suppliers today. To enhance wheel appearance, Alcoa has developed Dura-Bright technology, now available for its automotive forged aluminium wheel customers. The first to launch in Europe is Audi on its new A6 model. Alcoa’s David Yates puts a good spin on Dura-Bright and how Alcoa Wheel Products is forging a growth business in Europe.
just-auto: We all know Alcoa for its expertise in aluminium and, in particular, developing lightweight vehicle structures. Yet Alcoa seems to be involved in other automotive applications. What is Alcoa involved in and what are you responsible for?
David Yates: On a broader scale, Alcoa is the world leader in the production and management of primary aluminium, alumina and fabricated aluminium. In the wheels business we are lucky to benefit from all of the innovation brought to us from our primary metals business and also the technical centre in Pittsburgh, the largest of its kind in the world. Alcoa also supplies lightweight aluminium spaceframe technologies, structural castings, subassemblies and modules to the automotive industry. Personally, I focus on developing the commercial activity of our forged wheel business in Europe.
Implementing a forged aluminium wheel, instead of a cast wheel, can contribute to an immediate and significant saving in weight, improvement in performance and handling and, most importantly a direct reduction in CO2 emissions. Our design team can reduce wheel weight by as much as 30 percent compared to a cast wheel.
The CO2 emission targets of 130g/km will come into play in Europe in 2012. This is a tough target for all and, as I believe, OEMs have some distance to cover to meet the targets mandated in the future. OEMs are working hard to meet the challenge and there is an increasing realisation that fitting forged wheels can form a part of the solution. Changing to a forged wheel can be the fastest and lowest cost way of saving significant amounts of weight without compromising the design of the car.
just-auto: We have seen that over the past twenty years the average size of a family car wheel has grown substantially. How is Alcoa Wheel Products helping OEMs in the compromise between size and weight?
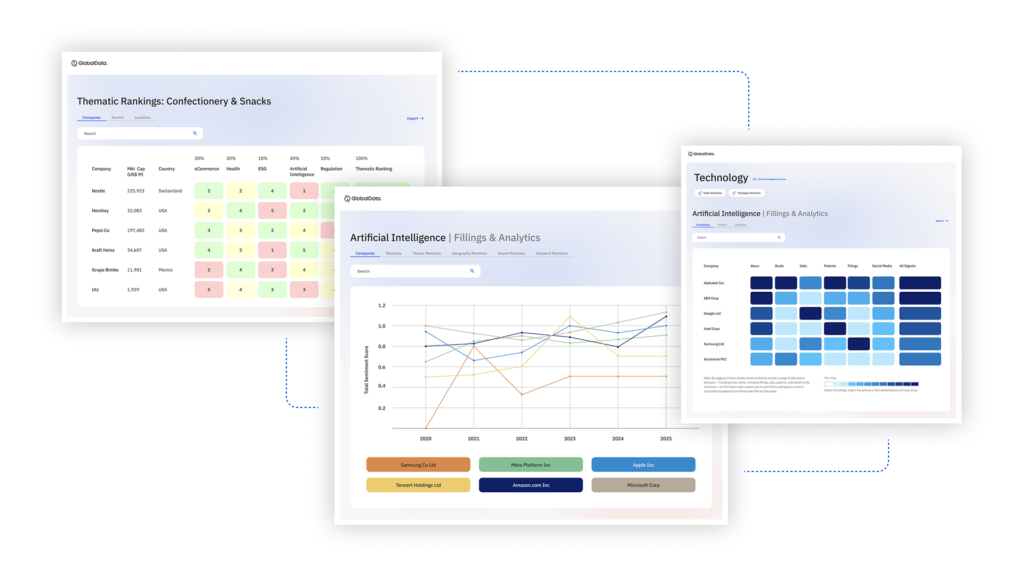
US Tariffs are shifting - will you react or anticipate?
Don’t let policy changes catch you off guard. Stay proactive with real-time data and expert analysis.
By GlobalDataDavid Yates: Wheel designs have been a focal point in car styling for many years. As a result, in the last decade conventional cast wheels have become larger and, thus, a lot heavier. Alcoa’s forged aluminium wheels are much lighter allowing the OEM to have a larger wheel without adding weight. In fact, our forged wheels are usually lighter than the smaller cast wheels they replace. This not only reduces weight but also helps to reduce the mass moment of inertia, giving engineers more options regarding braking and suspension. In addition, a lighter wheel will reduce un-sprung weight on a car, increasing vehicle performance and feedback to the driver on steering and braking.
just-auto: So how much lighter is a forged wheel compared to a cast wheel?
David Yates: Our engineers have found that an optimised forged wheel can be up to 30 percent lighter than its cast wheel counterpart. However, we have saved 31kg by converting to our forged wheels. It is not always so much but, say, a weight optimised 19-inch forged wheel should be at least 3-4kg lighter than a similar cast wheel. The cumulative result could be up to 20kg if the spare wheel is forged too.
just-auto: How are the weight savings achieved?
David Yates: Forging is the process of forcing a solid billet of aluminium between forging dies under extreme pressure to form a wheel. As the metal is never molten the grain flow remains consistent through the entire wheel giving far greater strength than a cast wheel.
This superior grain structure allows us to extract material making it much lighter than a comparable cast wheel whilst retaining the durability and test performance required by our OEM customers.
just-auto: So is there a higher price to pay?
David Yates: The manufacturing process for forged wheels is higher than that of cast wheels. However, the benefits obtained from our forged wheels outweigh the premium attached to them. Adopting forged wheels can be the fastest and lowest costs method of extracting so much weight from a car. Plus, it requires little involvement from the OEM as we usually undertake most of the work.
Additionally, a single tool can potentially create many different styles, reducing the customers’ capital costs significantly. From style freeze we can be producing series wheels in as little as five months, allowing a quick and easy fix for refreshing a car.
just-auto: Alcoa Wheel Products is about to launch Dura-Bright technology. Could you tell us more about that?
David Yates: Our customers have stated that the discolouration of wheels is one of the most common complaints by consumers. This is caused by brake dust and other particulates becoming trapped in the clear coat applied to wheels. Once this happens this dust can never be cleaned off and the wheels will always look dirty. Dura-Bright technology eliminates this problem making the wheel completely resistant to dirt, brake dust, oil and road grime. Additionally, the wheels are very easy to clean and have superior corrosion performance and so stay looking great for a long, long time.
It has taken a long time to develop but is now proving to be one of the most exciting technologies out there. Last year we won a PACE Award from Automotive News for Dura-Bright proving that this is an industry leading technology.
Our first customer in Europe is Audi, which has just released an 18-inch wheel with Dura-Bright technology for the new A6. We are in discussions with most premium and performance OEMs about Dura-Bright.
just-auto: Can Dura-Bright technology benefit the fleet manager?
David Yates: Dura-Bright technology has been tested and available through commercial fleets in North America for several years. Fleet managers have relied on the nearly maintenance free benefits of the wheel surface treatment to always have their vehicles looking good. Now Dura-Bright is available for car OEM programmes it extends the benefits to these customers. A dirty vehicle used for work purposes can reflect poorly on the driver and the company. Dura-Bright technology allows for easy cleaning and maintenance and the wheels will stay looking good for a long time.
just-auto: You mention life cycles. On the macro-scale, how can an organisation such as Alcoa be eco-friendly?
David Yates: Aluminium is greener than ever and can be recycled endlessly with no degradation. Alcoa pays close attention to alloy chemistry to ensure consistency of materials for optimal product properties. In addition, innovations like easy to clean Dura-Bright technology reduce or eliminate the need for harsh chemicals and cleaning products previously required by vehicle owners and fleet managers.
As well as material benefits, Alcoa has twice been named as one of the most sustainable corporations in the world in the “Global 100” ranking of the top role models in sustainable business practices at the World Economic Forum in Davos, Switzerland.
just-auto: Alcoa has only recently entered the wheel market in Europe. Can you mention any other projects?
David Yates: We recently supplied the Lamborghini Reventón, where Lamborghini required Alcoa’s expertise to develop a very lightweight, high performance wheel with a unique appearance. We are working closely with AMG and have already launched a wheel on the CLK63 Black Series. While inventing the forged aluminium wheel in North America over sixty years ago, Alcoa only started supplying forged wheels in Europe around two years ago. We are now working with most of the premium and sports car manufacturers all having programmes that will launch soon.