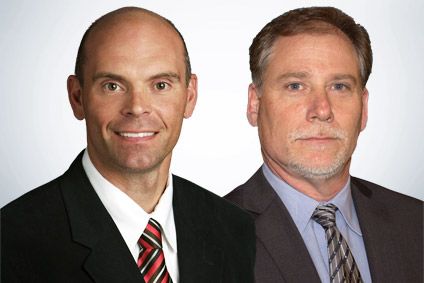
By outsourcing front-end modules (FEMs), automakers are able to reduce the number of operations on their assembly lines, simplify their supply chains, reduce modular weight and improve the ergonomic aspects of the assembly process. Magna Exteriors, a wholly-owned operating unit of Magna International, is among the global market leaders of FEMs. To learn more about how the market is shaping up, we spoke to Rob Selle, Global Product Line Technical Director, Magna Exteriors and Mark Pilette, Global Product Line Technical Manager, Magna Exteriors. In addition to FEMs, Magna Exteriors' portfolio of products includes liftgates, door modules, exterior fascias and trim, active aerodynamic systems, running boards, sealing, trim and engineered glass.
Could you give us a summary of Magna's FEMs business?
Rob Selle: Magna has a history of producing FEMs over the last couple of decades. Magna has produced millions of modules, and we currently produce a wide range of front structural components to complete assembly modules that include headlamps, sensors, fascias, grilles and active aero content, for many OEMs globally.
Is that active aero, the active shutters that we see?
RS: Yes. Active shutters are a big part of that. We also produce an active front air deflector. This is currently not part of the front end assembly, but we do have enquiries from OEMs looking at us anchoring that into the assembly.
Is the active grille shutter still expanding in North America?
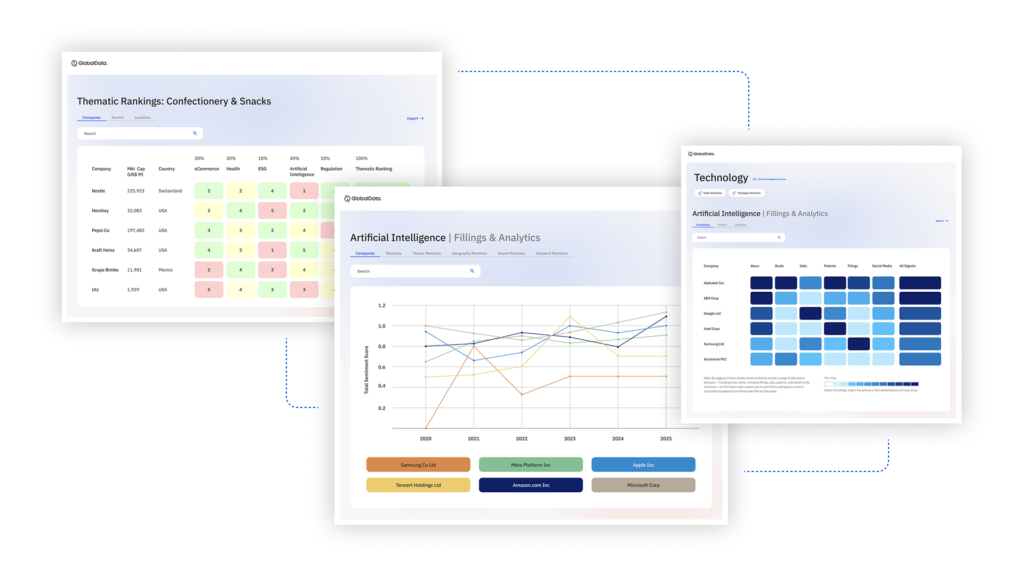
US Tariffs are shifting - will you react or anticipate?
Don’t let policy changes catch you off guard. Stay proactive with real-time data and expert analysis.
By GlobalDataRS: It comes two-fold. Obviously, it benefits fuel economy, and on the EV market it benefits range by reduction of aero drag on vehicle, so there is a significant benefit to putting it on there. But also, the government provides credits to the OEMs by having some of these fuel economy devices on the vehicle.
Who are your customers?
RS: We have a very wide range of customers globally. We ship to the North American OEMs and we ship to the European OEMs, and even provide content in the Asia-Pacific market.
For a supplier of FEMs, what does taking on that responsibility mean?
RS: As a full-service supplier, we are responsible for complete engineering, So we have to balance between engineering a front end assembly that affects the vehicle performance and appearance, and the complexity and quality management of the supply base. The way you would think of it, this is a structural component that's on the front of the vehicle which is a critical part of the vehicle both from an appearance standpoint and a functionality standpoint. So it requires a significant amount of responsibility from a design integration standpoint. Also, the management of all those complex components coming together from a tolerance, how they fit, how you manage the gap and flushness of these components. So you ship in a module that is quality, both in terms of performance and appearance, to the OEM.
Is colour matching FEMs still considered an issue?
RS: It's not as much of an issue as it was years past. Harmonization of colour is something we have mastered as an industry and is no longer a significant issue.
In what ways can Magna add value when assembling a FEM?
RS: We can offer a significant amount of value through production assembly tolerance management, along with our process and standards. If you think about this complexity, there's a multitude of components, and each component has its own tolerance. How we integrate and manage those components together so they all fit correctly and maintain gap and flushness is a critical part of the assembly value add.
We also have a deep understanding of part functionality. Magna is not just an assembler. We design and integrate. Hence we have a deep understanding of the functionality interface of these parts. This allows Magna to design products, assembly equipment and processes that improve the overall fit and function of FEMs by aligning to the OEM build variations.
To what extent is supplying FEMs for EVs any different from ICE cars?
Mark Pilette: As we see more EVs – and ultimately EV/AVs entering the market – there is an opportunity due to their unique architectural requirements, that FEMs could provide structural support for the sensors that may be included, such as RADAR or even LiDAR. We will need structural support for those ADAS features, and the FEM can certainly offer that. Ultimately, the EV platform may be a bit different, but the architecture requirements will still need, or potentially could need, a FEM.
What is the next stage of responsibility?
RS: I see the next stage of responsibility as expansion of functionality found within the vehicle front assembly. OEMs and suppliers are balancing integration of key design function capabilities and serviceability repair cost. You can't make this front assembly so integrated that when you're in an accident or you have an issue and you have to service something you have to buy a whole new FEM. So, it is a complexity balancing act that the industry is going through right now of this expansion of sensors, LiDAR and RADAR into the front of the vehicle and where they're placed. We have a number of different design solutions we present to the OEMs that enable us to adjust our course of design and execution to what meets their needs best.
Material-wise in FEMs, what are you seeing?
RS: OEMs are always seeking a higher strength:weight ratio material, however, the component has to meet durability standards. Those durability standards keep increasing also on the vehicle side. As I talked about earlier, this is not just a bolt-on part. It's part of the vehicle structure, so the components have to meet a high durability standard, but they also want lightweight and structural stiffness with it. We do investigate a multitude of materials. For example, we continue to develop nylons and polypropylenes that have carbon fibre blend. We also consider lightweight reinforcements that are overmolded or part of the assembly based on OEM application needs. The trend is not specific to any one solution; each OEM is adapting as they see fit for their application, balancing cost and performance, and there is also a level of comfort the OEMs have with what they are able to simulate and validate before they go into vehicle testing. The OEMs need to have a comfort level that their CAE analysis is correlating to the solution you're producing, so the adaptation of some of these more exotic solutions is a little slower than what we thought we would see in the past due to the OEM confidence level. But with that we do see more and more expansion in material needs.
MP: Getting back to what we were talking about with EVs, because airflow needs are different for EVs versus ICEs, we see potential for integration panels that may replace grilles. These panels could incorporate decorative features as well as functional features, such as those sensors mentioned previously. I think the evolution of FEMs could include, especially on an EV or EV/AV, this type of integration panel.
In what ways have your FEM designs changed to take account of the pedestrian protection regulations?
RS: I would say the pull is obviously much stronger in the European region, but as more and more content and functionality is added to the front end of the vehicle, vehicle design practices have to evolve to follow and allow for protection zones and clearances to meet these regulations. It's a challenging balance of design of high-performance rigid structures and maintaining a level of compliance to meet these regulations.
Is there anything else you want to add?
RS: I would just add that Magna is one of the best positioned for the future market with its broad-based capabilities. We are a rare supplier that has both the ability to do electronics, structure, component integration, and even industrial design all in-house. We are a full-service manufacturing supplier that can partner with any OEM and produce a solution that meets their needs. It's a great company to work for and it provides so much opportunity and diversity.