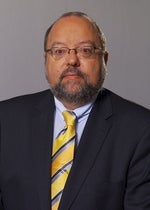
Ian Henry spoke recently with Udo Schwerdel about Continental's recent entrance into the turbocharger market.
Continental is a new entrant to the turbocharger market: can you tell us something about the background to this decision and why the company decided to enter a new market?
Actually we had been working on developing turbochargers back in 2006 when we were still part of SiemensVDO. Continental did not take over the business until 2008 but when it did, it quickly saw the potential for the company in this market. We had originally seen potential here because we were working on fuel injection systems for some of the first downsized gasoline engines and this had brought us into contact with turbochargers. We could see that as the market moved to more and more downsized engines, there would be growing demand for turbochargers.
You have focused on turbochargers for petrol engines; why is this?
The market for diesel engine turbochargers is well-established and while we could move into this segment in the future, for now we see a lot of potential for our technology in the petrol segment of the market. The gasoline turbocharger-market is by far the fastest growing segment within the turbocharger industry.
Can you give us an idea of the potential of this market?
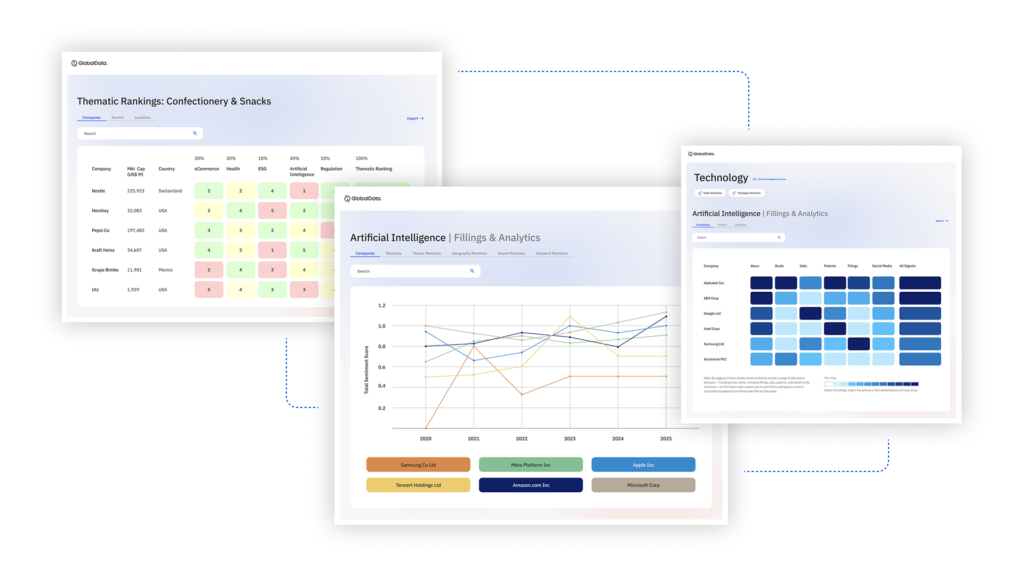
US Tariffs are shifting - will you react or anticipate?
Don’t let policy changes catch you off guard. Stay proactive with real-time data and expert analysis.
By GlobalDataWe see currently average growth rates for gasoline turbochargers worldwide of more than 20% per year.
Where are your turbocharger plants located?
We use the Lahr plant in Germany, which is part of the Schaeffler side of the business and we have also opened a dedicated turbocharger plant at Turtnov in the Czech Republic. We will have a further turbocharger plant located in China opening late 2015 and we are considering a plant in the NAFTA region although there has been no definite plan or date confirmed here.
Will you open more plants in the future?
We will certainly expand internationally in order to support our customers, especially in Asia.
Your turbocharger for MINI includes an aluminium housing; this was an industry first – can you tell us more about using this material?
Yes, the aluminium housing is a first for the automotive industry. Generally the industry uses cast steel or cast iron. Steel alloys use a lot of chrome and also nickel and nickel is a expensive element. The nickel content of some alloys can be as high as 35% so if we can find a means of using a cheaper material we will. This is why we looked at aluminium, although aluminium presents its own challenges as well.
What are these?
Typical turbocharger temperatures for gasoline engines now are over 1000deg C, but aluminium melts at 650deg C. So, to prevent the housing from melting we have had to use a water jacket cooling system which we developed in association with BMW. Furthermore, the mechanical properties of aluminium are very different to those of steel. Aluminium tends to creep at very low temperatures which has to be considered in the simulation processes.
That sounds complex and expensive?
It is really complex. In 2008 already we started with some basic work towards aluminium turbine housings. So when discussing the specific application with BMW we were not starting from scratch. However the fact that the engine was designed with this planned technology from the beginning so this made the development process easier than it would have been if we changed the material part of the way through the programme.
Which engine and vehicles use this turbocharger?
We deliver this to the three-cylinder 1.5L litre engines used on the Mini; the same engine is now also used on the BMW 2-series (Active Tourer).