
Torque vectoring is an often heard term, rarely seen computer-controlled system used on cars to deliver just the right amount of power to each wheel in order to improve road grip, stability, handling and performance. GKN Driveline’s solution, known as Twinster, is available on a number of cars, including mainstream executive models like the Opel/Vauxhall Insignia. As advanced torque vectoring systems are likely to appear on an even wider range of vehicles, just-auto/QUBE spoke to Ray Kuczera, Senior Vice President of Engineering, GKN Driveline.
What makes GKN’s torque vectoring solution different from the rest?
Torque vectoring generally refers to any system that is able to send precise amounts of torque to individual wheels, principally in the context of over-speeding an outside wheel in a corner to increase the yaw rate, helping to steer the vehicle.
Competitors’ torque vectoring systems typically use multiple sets of gears either side of the differential to achieve only very low levels of over-speeding, or they apply braking on the inside wheel in a corner to achieve a similar effect. The former is an overly complex option, while the latter wastes energy and can slow the vehicle down.
“The Twinster is unique in that it replaces a conventional differential with twin clutch packs that adjust the torque delivery to each wheel.”
GKN Driveline’s Twinster torque vectoring solution is unique in that it replaces a conventional differential with twin clutch packs that adjust the torque delivery to each wheel. There is no additional gearing or superimposed planetary gear sets, so it is far simpler solution for torque vectoring, as well as being more compact than conventional rear differentials – yielding significant packaging advantages.
GKN’s software sits on a dedicated ECU, and is able to update the actuation 500 times per second to provide quick, accurate torque control. The system continuously varies the pressure at each clutch pack, so they adopt controlled states between fully open and fully locked.
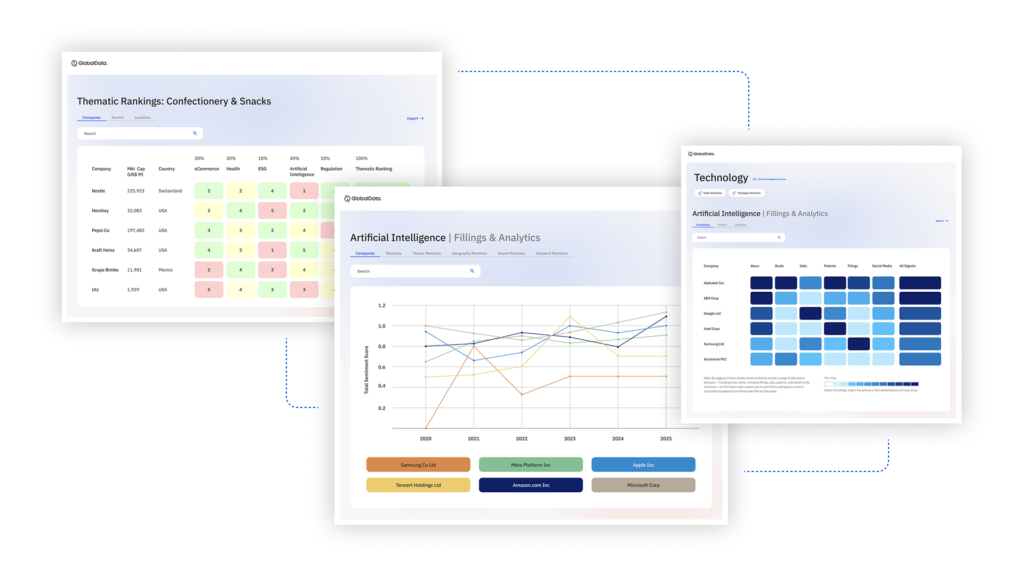
US Tariffs are shifting - will you react or anticipate?
Don’t let policy changes catch you off guard. Stay proactive with real-time data and expert analysis.
By GlobalDataWhat are the prospects for torque vectoring in mainstream vehicles?
Early forms of torque distribution, by brake force control or by limited-slip differential, have appeared in a variety of mainstream vehicles already. However, in reference to ‘true’ torque vectoring and GKN Driveline’s Twinster module in particular, its range of passenger car applications demonstrates its broad potential for future mainstream vehicles.
Twinster’s debut was in the Range Rover Evoque, and subsequent variants of the system have appeared in the Lincoln Continental and MKZ, the Ford Focus RS, Cadillac XT5 and the Land Rover Discovery Sport. The most recent application appears in the all-wheel-drive (AWD) variants of the new Opel Insignia and Buick LaCrosse.
“We anticipate that the volume and variety of mainstream vehicles featuring torque vectoring will increase significantly in the future.”
We anticipate that the volume and variety of mainstream vehicles featuring torque vectoring will increase significantly in the future. The precursor to this growth is the steady increase in demand from new car buyers for AWD technology.
AWD light vehicle production volumes are forecast to grow by 24% by 2022, and GKN’s unique torque vectoring technology is poised to take advantage of this increase by offering manufacturers a less complex yet more efficient AWD solution.
GKN is the only supplier able to develop and produce complete all-wheel drive systems with torque vectoring in-house. The company’s global engineering team provides local support, using vehicle integration, hardware and software expertise to accelerate the time-to-market and help brands deliver the best possible driving experience for their customers.
In what ways does torque vectoring make hybrid vehicles more efficient and dynamic?
Plug-in hybrid electric vehicles (PHEVs) are excellent candidates to showcase the benefits of torque vectoring systems. When a hybrid version of a vehicle is developed, it can often add a significant amount of redistributed weight, requiring revisions to the car’s calibration to mitigate the shift in mass. Torque vectoring technology can be used not only to compensate for the added weight, but to deliver more engaging driving characteristics.
Hybrid vehicles that use an electric drive motor for primary drive will be transmitting a significant level of torque through the wheels, and torque vectoring can help to manage that. Furthermore, the onboard eDrive systems in many hybrids can provide inherent benefits, offering on-demand electric drive to control and modulate torque vectoring technology more precisely, with the ability to deliver exact outputs to individual wheels. GKN has already revealed its eTwinster prototype system, which integrates torque vectoring AWD into an eAxle module, helping to deliver next-generation mobility, handling and efficiency.
What are the opportunities for torque vectoring in pure electric vehicles?
The dynamic characteristics of conventional ICE vehicles can be indirectly tuned by adjustments to the chassis limits, the distribution of weight and the response of the suspension. However, the dynamics of pure electric vehicles may be calibrated directly by tuning the parameters of the electric driveline itself.
Torque vectoring effects can be significantly enhanced by this feature of pure electric cars, where the direct drive of the e-motor allows for much finer and faster control of the vehicle’s responses. These rapid feedback loops and exact adjustments to the driveline, in turn, enable a more stable and precise driving experience.
Furthermore, given the significant levels of torque being transmitted to the driving wheels of a pure electric vehicle, torque vectoring for vehicle stability represents not only an opportunity but will likely be a necessity in the future.
Who else is interested in your technology and what are its prospects for integration in other vehicle platforms this year?
We cannot say which manufacturers have enquired about our technology, or which vehicles it will next appear in. However, we can reveal that we have developed a brand new torque vectoring system that will be shown later in 2017, and that it will be demonstrated in a model from a vehicle manufacturer not currently associated with any GKN Driveline electrified or AWD systems.
Are there easier, simpler ways of achieving the same thing that torque vectoring delivers?
There are a variety of systems that enable torque to be redistributed, but no other method can balance the imperatives of stability and response like torque vectoring. Furthermore, whereas other systems often act passively, GKN’s Twinster module anticipates torque requirements by monitoring inputs such as acceleration and steering angle, and actively calibrates a response before it is needed.
To produce purer performance and driving feel, true dynamic torque vectoring should also always increase the torque delivery to an individual wheel, rather than reduce its motive force. Systems that feature so-called ‘torque vectoring by braking’ are only able to deliver a limited number of the benefits of true torque vectoring. They imitate parts of the system, but do not deliver the capability.
GKN’s solution, in particular, is uniquely customisable to suit a variety of vehicle brands and model lines. For example, with the Ford Focus RS, the GKN development team applied a truly bespoke combination of new gearing ratios and control algorithms to over-speed the rear wheels, helping to create a mainstream performance vehicle with unprecedented driving dynamics.
What are your predictions for vehicle electrification by 2025?
“By 2025, our Chinese joint venture, Shanghai GKN HUAYU Driveline Systems, will be producing over 1 million eDrive units per year.”
In April this year, GKN Driveline announced a clear vision for its eDrive technologies. From 2018, China will start to become a global production hub for GKN’s state-of-the-art electrified drivelines, when production of its latest eDrive technologies commences at its joint venture facility in Shanghai. The country is the world’s fastest-growing market for electrified vehicles, and by 2025, GKN forecasts that its Chinese joint venture – Shanghai GKN HUAYU Driveline Systems (SDS) – will be producing over 1 million eDrive units per year.
As automakers increasingly seek to offer plug-in hybrid technology on their small car platforms – where packaging space is at a premium – GKN expects to see a surge in demand for eDrive systems that are simpler to package and assemble.
Is there anything else you would like to add?
With advancements in platform and engine sharing, and a shift to more electrically-supported driver inputs and feedback, the way a car drives is becoming ever more reliant on innovative driveline technology and software programming to differentiate models.
Systems such as Twinster can provide a genuine USP in a vehicle sector, while state-of-the-art software controls can effectively produce brand-aligned driving experiences. The latter in particular will become increasingly important for manufacturers, as they seek to ensure their new cars stand out from the crowd.