
Continuing just-auto’s series of interviews with tier one suppliers, Matthew Beecham spoke to Stéphane Martinot, marketing director of Faurecia Emissions Control Technologies about its exhaust heat power generation system, investigation into thermoelectric generators (TEGs) and how it helped Ford hit the right note on the Mustang.
Could you tell us about some of the technologies that Faurecia highlighted at this year’s Detroit auto show and your message?
At the 2016 Detroit Auto Show (NAIAS), Faurecia presented a number of innovations for emissions control technologies and exhaust solutions: the highlights include Exhaust Heat Power Generation (EHPG), first introduced at the Frankfurt Motor Show [IAA] in September 2015, and the Resonance Free Pipe (RFP).
Faurecia has developed the world’s first system to convert exhaust heat into electricity for hybrid cars and horsepower for commercial trucks. Using the principle of Rankine cycle, the Exhaust Heat Power Generation (EHPG) system employs a heat exchanger placed in the exhaust flow to produce pressurised steam that powers a turbine. The turbine’s shaft can be attached to a truck’s gearbox to turn the wheels, or it can be coupled with a generator that creates electricity to be stored in the battery of a hybrid vehicle. As a result, these vehicles rely less on their gasoline or diesel engines and significantly reduce emissions.
Faurecia’s focus on lightweighting to improve fuel economy incorporates virtually every system inside, outside and under the car—even the exhaust pipe. Faurecia’s new Resonance Free Pipe (RFP) contributes to this goal by eliminating the need for small silencers, known as resonators.
Resonators inside tailpipes break long sound waves to reduce unwanted frequencies. RFP™ eliminates these long waves without resonators by venting acoustic pressure at the optimum point in the exhaust system through a micro-perforated material. While most of the exhaust gas continues to exit the system through the tailpipe, this very minute venting of treated exhaust gas allows for a simpler system design that provides 1.8 to 5 kilograms of weight savings in a more compact package. RFP can potentially be used in any light-duty vehicle.
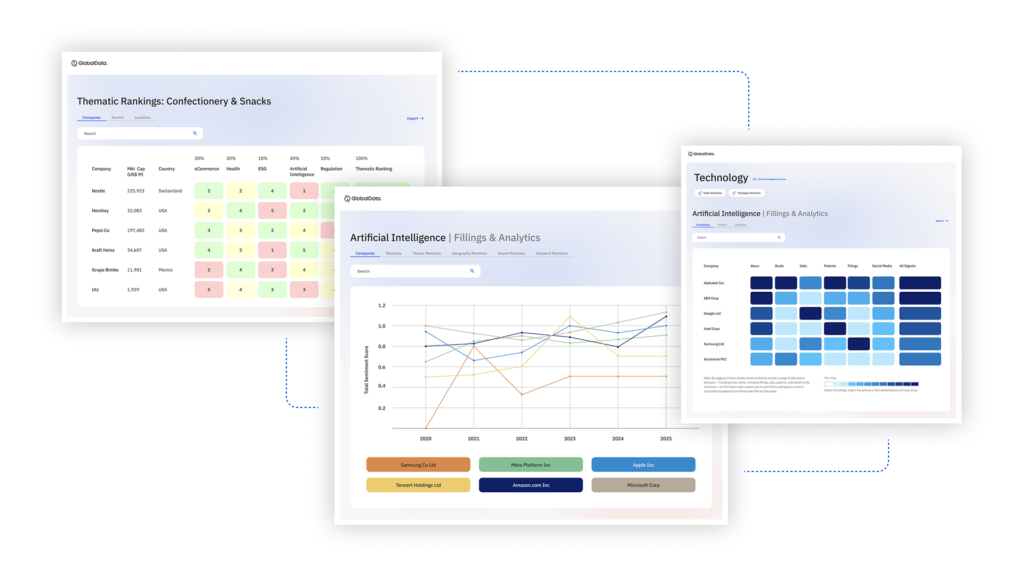
US Tariffs are shifting - will you react or anticipate?
Don’t let policy changes catch you off guard. Stay proactive with real-time data and expert analysis.
By GlobalDataFurthermore, at the Shanghai Auto Show (April 2015), Faurecia introduced the world’s first Gasoline Particulate Filter for gasoline direct injection (GDI) engines, for passenger vehicles, removing small particles to improve air quality and meet tight environmental standards.
Could you comment on how developments in aftertreatment are affecting the choice of engine management strategy?
To improve air quality the emission regulations are continuously improving everywhere in the world. Introduction of Tier3/LEVIII in the USA, China 6 level in China and RDE regulations in Europe are also combined with a precise roadmap for CO2 reduction in all these regions.
For both gasoline and diesel powertrains the new challenge becomes a simultaneous reduction of harmful gases emissions and fuel consumption (CO2 emissions). In the past it was more a trade-off, emission reduction were often reduced at the cost of higher CO2.
For gasoline engine, the introduction of turbocharged downsized GDI engines has brought a large improvement in fuel consumption with around 15 percent gains, but at the same time creating new challenges with higher particulate emissions. The growing adoption of Gasoline Particulate Filter technology in the aftertreatment system matches such a challenge and ensures low level of particulates emissions.
Similarly for diesel engines, the improvement of the combustion system has led to very low exhaust gas temperatures. The aftertreatment system needs however high temperatures to be efficient as soon as possible after engine start-up.
The development of Selective Catalytic Reduction (SCR) compact mixer like Faurecia SCR BlueBox, in combination with SCR-Filter (Integration of SCR function on the DPF filter) makes an optimised integration of the aftertreatment system possible. The complete aftertreatment is coupled directly to the turbocharger, with early light-off and a good efficiency on the whole operating points of the engine. The temperature management is then improved for both fuel consumption and emission control especially for effective NOx emissions reduction.
We have heard it said that the last remaining major challenge for powertrain engineers is to do something about recovering the 30 percent of fuel that disappears as hot gases down the exhaust pipe. What can be done about this?
Automotive drivetrains use fuel to power vehicles which produces a tremendous amount of heat, one-third of which is lost through the exhaust system. That wasted heat can be a valuable resource, however. For a number of years, Faurecia has produced exhaust heat recovery systems that capture exhaust heat and use it to warm vehicle interiors, allowing hybrid cars to switch to their electric mode sooner. Now, Faurecia has developed the Exhaust Heat Power Generation (EHPG), a system to convert exhaust heat to electricity and power [see more below].
I guess one solution is a thermoelectric generator (TEG) which can use virtually any heat source, including waste exhaust heat, to produce electricity using the thermoelectric effect. Given the infancy of the TEG market, there are a number of unknowns. But, in general terms, how do you foresee the market acceptance for TEGs in Europe?
Faurecia also is investigating another method of converting waste heat to electricity. The thermo-electric generator, or TEG, uses the Seebeck effect to transform heat to electricity with no moving parts.
The TEG consists of an array of semiconductors on a substrate that produce an electrical current when a temperature differential is applied to them. Cold water from the vehicle’s cooling system lowers the temperature on one side of the array while exhaust gases heat the other side. This heat gradient causes the semiconductors to release electrons that flow from the hot side to the cold side until an equilibrium is attained. By maintaining the difference in temperatures between the heat source and heat sink, the current flow is sustained.
The TEG can be used on both hybrid, and non-hybrid vehicles to furnish additional electrical power. Its yield is much less than that of EHPG, producing up to 400 watts of power from exhaust heat. However, it is even more compact than EHPG; it can yield a fuel savings of 3 to 4 percent at its peak; and it enables vehicle designers to incorporate a smaller alternator—or even none—to recharge the battery, thereby saving on weight.
The TEG is expected to first be available after 2022, once its efficiency and cost factors are optimised.
When we last spoke [October 2013], you mentioned that Faurecia has been developing energy recovery technologies, including those based on Rankine and thermoelectricity. Could you tell us a little more about this and the stage you have reached?
For several years, the industry has been able to recover exhaust heat to help in warming vehicle interiors, but EHPG is the world’s first system to directly convert exhaust heat to electricity and power.
EHPG produces power that can be used to directly drive trucks or to extend the use of electrical power in hybrid vehicles. EHPG harnesses the principles of Rankine cycle to convert heat from exhaust gases to electrical power. In much the way electricity is generated in power plants, EHPG employs a heat exchanger (evaporator) located in the exhaust flow. The thermal energy in the pipe is transferred to a so-called working fluid.
The resulting pressurized steam powers an expander, which could be a turbine. The expander’s shaft can be attached to a truck’s gearbox to turn the wheels directly. In hybrid passenger cars, the expander is coupled to a generator that creates electricity, which is stored in the vehicle’s battery. After steam leaves the expander, it moves through a condenser where it is converted to liquid again, transferring its residual heat to the vehicle’s cooling system. Finally, a pump pushes the liquid back to the evaporator, creating a closed-loop system.
In both applications — mechanical power for trucks and electrical power for hybrids — the vehicles consume less fuel, and therefore hydrocarbon emissions are reduced. In trucks, overall fuel economy improves by 5 percent or more, even taking into account EHPG’s additional weight, and the system can produce 10 to 15 kilowatts of mechanical power, reducing the power and fuel demands on the vehicle’s engine. Using EHPG would mean saving around 20,000 liters of diesel fuel — or 40 full tanks — and avoid 50 metric tons of CO2 over a truck’s lifetime. EHPG is estimated to pay back its cost in just two years in the form of fuel savings.
In passenger vehicles, a smaller EHPG system generates 1 to 2 kilowatts of additional electrical power, adding to the electricity stored in the battery and thereby delaying the need to switch to the gasoline drivetrain. In hybrids EHPG nets a fuel economy improvement of about 7 percent. Moreover, EHPG is expected to reduce CO2 emissions by 9 g per km, which would sum up to 2.5 metric tons less CO2 over a hybrid vehicle’s lifetime.
EHPG works like a power plant, but in this case Faurecia has adapted the technology to the highly specific challenges of cars and trucks, such as size, power, weight, etc. That is the real innovation.
Initially, Faurecia anticipates applying EHPG to long-haul trucks, which travel for long distances at stabilized speeds. EHPG systems should start appearing on these vehicles in 2020. Shortly thereafter, we will begin production for new hybrid passenger cars.
In developing EHPG, Faurecia overcame a number of challenges:
The system has been equipped with an ECU-controlled by-pass valve to ensure the cooling system does not become overheated in high-power conditions.
EHPG must be integrated and packaged so that it can be mounted close to the engine’s exhaust to take advantage of the hottest gases.
The current system uses water/ethanol as the operating fluid, but Faurecia also is exploring other substances, such as an organic fluid, as well as possibly using a piston in place of the turbine.
EHPG is designed specifically for new vehicles and is not a retrofit solution because of the integration constraints that have to be addressed from the beginning of the vehicle’s development.
For some time, we have heard about automakers creating the right note using the exhaust of certain models. Could you talk us through Faurecia’s contribution to the Ford Mustang’s exhaust?
Because of downsizing, turbo-charged gasoline-powered sporty vehicles have a different problem—too much irritating noise, and not enough sporty sound character. For these vehicles, Faurecia has developed the equivalent of a noise-cancelling headset for the exhaust system.
A speaker is mounted near the exhaust tailpipe to manage a full range of frequencies and, through an algorithm integrated into the ECU, produces a frequency that is close to the exact opposite of that which is generating the noise at any given moment. As the driver throttles up or slows down, the ECU constantly monitors the noise frequency and changes the sound that the speaker generates to keep the opposing frequencies in sync. The result is that most of the frequencies cancel each other out, leaving the exhaust noise at a very low, but still audible level.
Once the aggravating noise is canceled, the ECU uses the same speaker to generate a more pleasing and appropriate sound in its place, just as it does for Dynamic Sound Generation more especially for diesel engines. The variety of sounds that can be emitted from the speaker are limitless, but in practice the system creates an engine exhaust sound that enhances the image of the vehicle. For example, a Mustang fitted with an in-line four-cylinder turbo-charged gasoline engine could acquire a sound signature close to the six-cylinder upper model, while still differentiating itself from the later. The system could even be used for hybrids to cancel out the exhaust noise when the gasoline-powered engine is running.
The auto industry is currently evaluating and implementing the most effective ways to use Dynamic Sound Generation and Dynamic Sound Cancellation. In many instances, the algorithm will be integrated into the vehicle’s engine ECU; in others, a stand-alone ECU module could be used to modify the sound, communicating with the engine ECU. Faurecia is prepared for the full scope of sound design options, from ECU to speaker and canning.
Faurecia’s first Exhaust Dynamic Sound Generation system will kick-off on the 2018 model year of several carlines of a premium German customer.
As we understand it, Faurecia is using a technique called brazing to make exhaust pipes that are .8 mm thick compared to the 1.2 mm pipes produced by MAG welding. Could you comment on some other ways in which the megatrend for lightweighting has influenced your exhaust designs?
The remainder of this interview is available on just-auto’s Global light vehicle OE exhaust & emissions aftertreatment systems – forecasts to 2030