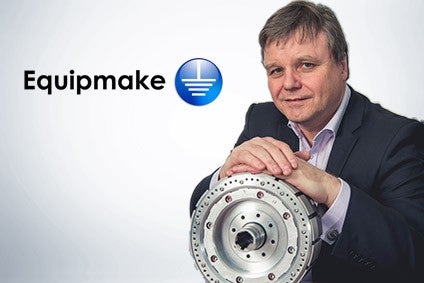
UK-based electronics R&D specialist, Equipmake, has developed what it claims to be the world’s most power dense electric motor for automotive, marine and aerospace applications. Using technology first applied to F1, Equipmake’s founder, Ian Foley, was the man behind the F1 KERS hybrids in 2009 that were so successful for Williams. We caught up with him to learn more about the business and its technologies. The company’s current projects include the Ariel Hipercar and an electric bus project.
Could you give us some background to Equipmake?
Equipmake is an electric powertrain specialist, providing everything from high-performance motors to power electronic systems all the way up to complete electric vehicle (EV) drivetrains. The company stems from my career in motorsport. Back in the 1980s, I started out at Lotus Engineering, where I was developing the very first active suspension systems. Following a short time at Benetton, I then went back to Lotus working in F1 on active suspension and then endurance racing. I’d always wanted to run my own company, though, and while race engineering for Jan Lammers at Le Mans (after we’d changed our third gearbox during the race) I suggested to Jan that I develop a paddleshift gearbox and set about building my own. That was how Equipmake started.
That gearbox went on to be used by most of the Le Mans grid and it was a natural progression for me as a motorsport engineer. In the early 2000s, Equipmake was doing research into electric motors and flywheels as we knew that F1 powertrains were going to go hybrid. The FIA was preparing to mandate ultra-capacitors for this technology, but we proposed the idea of a flywheel, which they liked. Several F1 teams then got in touch who were keen to develop the technology further. Because we were a start-up, that was a bit overwhelming! We didn’t want to bite off more than we could chew, so we decided to work with one highly-respected team: Williams.
The resulting hybrid flywheel system went on to be used to great success by Porsche and Audi in endurance racing. There were applications for the flywheel technology outside of motorsport so Williams Hybrid Power was formed, with me as managing director. Successful though that was, the yearning to be my own boss never really left. The high-speed flywheel developed for the Williams programme was effectively a composite electric motor, so I revived Equipmake with the aim of using some of the expertise I’d developed in electrification and applying it to a new design of motor.
Could you tell us about your spoke motor, APM200? What have you done differently?
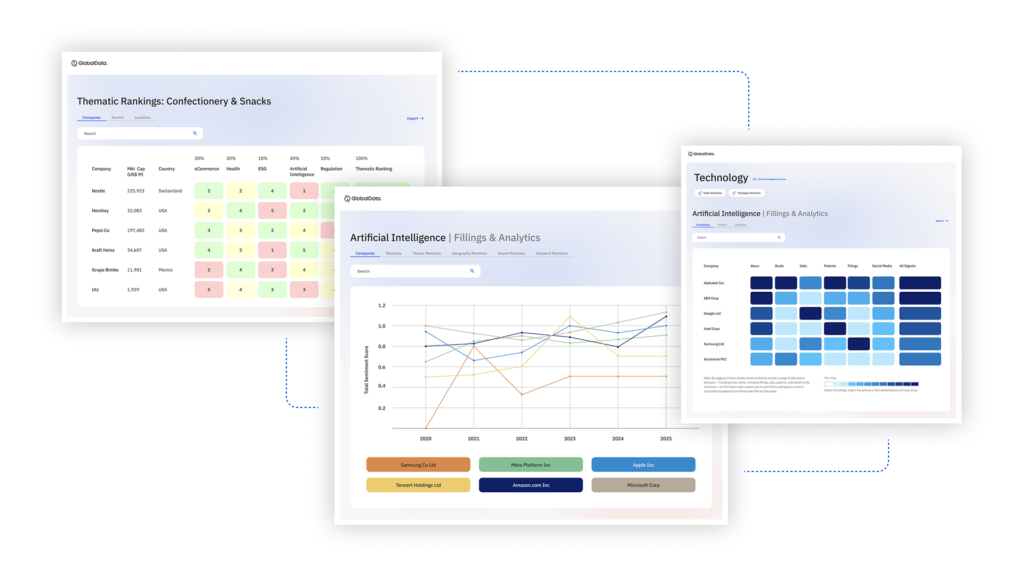
US Tariffs are shifting - will you react or anticipate?
Don’t let policy changes catch you off guard. Stay proactive with real-time data and expert analysis.
By GlobalDataThe magnets are arranged like the spokes of a wheel, which makes the best use of the magnetic flux and offers a huge cooling advantage.
The spoke motor is an ultra-compact, high performance permanent magnet motor. We believe it is the most power and torque-dense motor in the world. The magnets are arranged like the spokes of a wheel, which makes the best use of the magnetic flux and offers a huge cooling advantage. The APM200 is also smaller and cheaper to make than a standard motor.
It differs greatly from other systems. Conventional motors have magnets arranged in a V-shape in laminations around the hub. Toyota’s Prius has run with this design for more than 20 years and, effectively, everyone’s gone with similar versions ever since. The problem is cooling.
It’s hard to get coolant close enough to the magnets to keep them in their operating zone under constant high-power operation. That’s why, unlike petrol engines, electric motors have two power figures: peak power (i.e. flat-out running) and continuous power (i.e. how much power can be sustained before overheating and shut down). Spec a standard motor with expensive magnets, which keep working at a higher temperature, and it’s possible to close the gap, but it’s costly. Our spoke motor has magnets arranged at 90 degrees to the hub with laminations between each of the spokes. This gets better use of the magnetic material: for a certain torque, we can use 25 per cent less, or use the same and get 25 per cent more.
We can also get water inside the hub and cool the magnet directly. So, the spoke motor gives us more torque to start with, but is much better at cooling. The package is also compact. Against a conventional motor of similar performance, we’re about 50 per cent of the volume and 80 per cent of the mass, and because the motor is smaller and lighter, it’ll be cheaper to make.
In terms of performance, the result is a motor capable of high power and torque output than more conventional configurations. Our APM200 motor, for example, weighs just 40kg and produces 220kW and 450Nm at up to 10,000rpm. To further put that into context, on a kW/kg basis any electrical engineer would be overjoyed with an output of 4 kilowatts per kilogram. Our APM 200 motor puts out 5.5kW/kg and the technology can be tuned to make as much as 15 kW/kg.
The motor was developed as part of an INNOVATE UK joint venture project to build a range-extended electric supercar – the Ariel Hipercar. Due in 2020, it will feature four of our motors giving a total output of 1,180bhp.
Aren’t magnet motors expensive, though, compared to induction or switched reluctance motors?
The short answer is, at the moment, yes – but that’s not the whole story. Batteries are by far the most expensive component of an EV powertrain, with the price still around £300/kWh. So, if you can reduce the size of the battery, you can substantially reduce the cost of the entire powertrain. One way to do this is to use an electric motor that is more efficient and powerful, while also being lighter. The result being that, for a given range, less battery capacity is required resulting in a smaller, lighter, cheaper battery.
Another often-mentioned drawback of magnet motors is the cost of rare earth materials. Our APM200 motor may use Neodymium rare earth magnets, but there are various grades of material, from ‘cooking grade’ right up to motorsport levels of cost. We can use the cheapest because the spoke architecture allows us to keep them cool enough to maintain flux.
They still make up as much as 50 per cent of the cost of the raw materials, but once you consider the cost of manufacture, the contribution of buying and processing the Neodymium is just 15 per cent of the motor’s total. With the performance benefits and reduced battery requirements, the increased cost of using our magnet motors is offset, making them an attractive proposition and ideally suited to automotive applications.
Until now, there just hasn’t been a low-cost route to manufacturing a spoke motor.
Also, until now, there just hasn’t been a low-cost route to manufacturing a spoke motor. We’ve adapted the architecture for mass production, using a cheap, forged aluminium hub, while our patented rotor design optimises cooling, but uses standard processes and materials.
What stage of development have you reached with your spoke motor? And by when do you expect it to reach mass production?
The motor is fully developed and ready to be used on a car, bus, bike, boat, plane or anything that requires a high performance, compact and efficient electric motor. In terms of manufacturing, we are already building APM200s in low volumes to meet demand generated by a host of projects. These include a number for an electric supercar – I cannot say which I’m afraid! – and of course there is the Ariel Hipercar project, with the first cars due to arrive in 2020.
Scaling up is the next key step and where our ambition lies.
Scaling up is the next key step and where our ambition lies. We are currently scoping out sites for a factory close to our base in Hethel, with the aim of ramping up production to 10,000 units annually. We’re actively seeking outside investment to accelerate our progress here. However, while we can build every part of the EV drivetrain, true mass production is one thing we can’t do. For that, we would more than likely need investment from a Tier 1.
We understand that an upcoming application of the motor includes an electric bus. What is the market opportunity for electric buses? And who else do you have in your sights?
Yes, we are very excited to be working with Brazilian company Agrale on an electric bus project. We are providing them with a low-cost powertrain for a new electric bus that is set to go on sale in Buenos Aires, Argentina, in 2020. We are developing the entire powertrain, which we have dubbed ‘Ebus’. This has two APM200 motors at its heart and along with the very latest lithium-ion batteries, the vehicle has enough range for one day’s running: around 200 miles.
The market opportunity is significant, in Buenos Aires alone there are around 16,000 buses. Closer to home, London currently has around 8,000 buses. If we were to look at it from a global perspective, for large buses (over 10 tonnes) you are talking about market sales of around 300,000 new vehicles per year. A recent report from IDTechEx predicts that all new bus sales will be electric by 2024, so the opportunity is huge and we are well placed to take advantage.
As for other opportunities, we have no firm details right now but the Ebus powertrain is modular so it can be adapted to a variety of bus sizes and configurations – from small single deck to large double deck vehicles. Watch this space.
There appears to be more focus than ever on developing electric powertrain components. In terms of electrification, has the auto industry reached a turning point? In 2030 what do you see the share of pure electric vehicles being at?
There is tremendous pressure on OEMs to reduce emissions and they are struggling to keep up with ambitious legislation. As a result, electrification is an enormous focus for makers of passenger cars, but it’s not just that sector: commercial vehicles, motorcycles, maritime and aerospace, you name it, we are currently inundated with work. In terms of adoption and a turning point, that really does depend on global incentives and having the appropriate infrastructure. How many pure EVs will be on the road in 2030? That’s almost impossible to predict, but sales of ‘electrified’ vehicles, whether they are solely electric or hybrids, are only going up and they will all require electric drive components, such as compact, lightweight, powerful and highly-efficient electric motors.
Do you think there’s room for fuel cell electric vehicles?
Provided there is the infrastructure, yes. In terms of our business, it would not have a significant impact – fuel cell vehicles are essentially electric cars, so our powertrain would still be suitable.
What’s next for Equipmake?
We’re fully focussed on transitioning to a Tier 1 manufacturer, while continuing to remain ahead of the race in terms of power dense motors. We are currently developing a motor using advanced additive manufacturing techniques which will enable us to double the power density of the motor.