
Continuing just-auto’s series of interviews with global automotive material suppliers, Ralph Ramaekers, global marketing director, automotive at DSM explains how the supplier’s engineered plastics and new processes can support OEMs in designing tomorrow’s car.
Could you tell us about DSM Engineering Plastics?
We are a global supplier of high-performance engineering thermoplastic solutions. DSM Engineering Plastics has a focused portfolio of products; with each of them it has realised global leadership. DSM is the global number three in the overall market for semi-crystalline engineering plastics and is the global market leader in high-temperature polyamides. In polyamide 6, DSM holds a number two position, as it does in thermoplastic copolyester elastomers.
DSM Engineering Plastics is a global player in development, manufacturing, marketing and sales of polyamides and polyesters. These materials are used in components for the electrical and electronics, automotive, flexible food packaging, and consumer goods industries.
The automotive industry is a key end-market for DSM Engineering plastics. Key segments for DSM in automotive are powertrain, air/fuel management, safety components, automotive electronics and lighting, and gas tank systems.
Who are your customers?
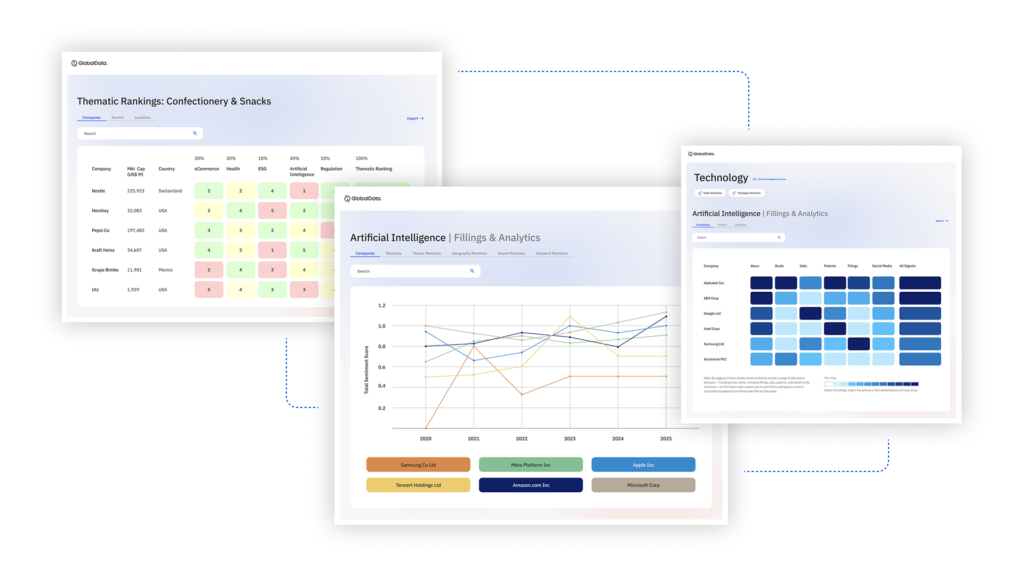
US Tariffs are shifting - will you react or anticipate?
Don’t let policy changes catch you off guard. Stay proactive with real-time data and expert analysis.
By GlobalDataDSM Engineering plastics is operating at all levels in the value chain, from the moulders up to the OEMs. Our automotive customers include Bosch, Valeo, Denso, Aisin, ZF-TRW, Autoliv, Schaeffler Group, Renault-Nissan, Peugeot, Tata Motors, BMW, Daimler, Toyota, Volkswagen, Ford, and General Motors.
Given the very gradual move toward autonomous driving, to what extent do you see the automotive and electronics industry merging?
The merging of these two industries is already at full speed. Just look at the amount of electronics in the new cars that are currently being released on the market. DSM Engineering Plastics has a long history in Electronics and we are benefiting from this position for the automotive market right now. Automakers are working on new vehicle concepts that have the potential to transform the automotive industry in the most dramatic ways. The ‘connected car’ is no longer a fantasy. It is already there, a fully digitised car with WiFi, advanced infotainment systems and apps; V2V communications that let cars on the road ‘talk’ to each other, exchanging data such as speed and position etc.
Also the ‘intelligent car’ is just around the corner. As a precursor to the autonomous vehicle, the intelligent car can give drivers a first taste of the experience of relinquishing control of the vehicle.
The fully autonomous car will be the next step and automakers, the path from current models to driverless cars is going to be an exciting period of transformation. These new developments represent enormous opportunities for DSM Engineering Plastics.
As more electronic functions are squeezed into cars, packaging space becomes even more limited. How can DSM help?
ADAS [Advanced Driver Assist Systems] is the name of the game towards full autonomous driving which requires a lot of new hardware next to very intelligent software. It is on the hardware side where DSM plays an important role to ensure secure interconnections, data integrity and miniaturisation with innovative material solutions.
I guess that an increasing number of electronics in cars – and delivery of digitised information – means more effective shielding of electronic components against, and from causing, electromagnetic interferences. Is that correct? What is DSM’s solution to this?
EMI [electromagnetic interference] is already now a big issue and will increase in the future only more through the penetration of electronics into automotive. DSM has spent quite some R&T effort in understanding EMI and implementing solutions to shield sensitive components from EMI. This is achieved through special fillers like, for example, carbon fibres which are not only delivering the required high electrical conductivity but moreover also increase mechanical strength of parts. Embedding also thermal conductivity into such materials on top of what carbon fibres deliver, one can also deal with the thermal management of electronics enclosures.
In what ways do high-performance consolidated components help optimise manufacturing processes? And what are the upcoming applications?
Functional integration into a single component like EMI shielding and thermal management. For example, in one plastic cover of an ECU. This way metal cover can be replaced by highly efficient plastics covers contributing to about 40 percent weight reduction.
Miniaturisation of electronics components like connectors to achieve space reduction, this leading to different assembly techniques such as reflow soldering as replacement of wave soldering.
Through technologies such as LDS electronics assemblies with various contacts points and cables can be simplified by printed electronics straight on top of the plastic resulting in higher reliability and component count reduction.
Could you tell us more about your Laser Direct Structuring (LDS) process? i.e. what is it, what does it do and why should your customers be interested?
In automotive, especially with the further advance of advanced driver assist systems and its natural evolution into autonomous driving, designers will increase their demand towards reliability, safety and weight reduction.
In addition, space becomes a real premium since more functionality will get integrated into already now confined space. DSM is a leading technology and material supplier in LDS. LDS allows printing of electronics directly onto the plastic omitting the use of PCBs and skipping lots of cables and interconnects. This technology does not only directly lead to the removal of parts which previously consumed space and had extra weight, it furthermore also increases reliability since any of these contacts previously could break in a car is use.
Our solutions are currently used in many commercial applications such as sensors or switches, antennas or lighting and we see a strong customer pull to further expand the usage in automotive.
We understand that your materials used from LDS are based on polyamide 4T and branded ForTii. How do these compare to rival liquid crystal plastic materials also suitable for LDS?
ForTii is outperforming alternative LDS materials in various aspects. Its line resolution is at par with LCPs while outperforming in weld line strength. A very important advantage to designers is the form of a weldline between LCPs and ForTii. The stronger weld line of ForTii is completely flat. The form enables a designer to plate his electronics across the weld line without compromising on design. In case of LCPs they cannot do so since the weldline has a V-shape and the plated track would not find any support by an underlying plastic, hence the track is cracking. A designer therefore is forced to change his design by avoiding plating across a weldline which is already mechanically a root cause of higher failures with LCP.
Compared to alternative PPAs, ForTii has the highest line resolution and as tested by LPKF sets the new standard for the so-called plating index, a parameter which indicates the plating time and hence directly correlates to the cost of the process. The smaller the plating index, the shorter the plating time, the lower the processing cost and in addition the better the plating quality due to no over plating. We have also expanded our LDS portfolio significantly. Further to ForTii, we now also added ForTii Eco (a bio-based compound derived from renewable source and non-competing with the food chain).
In addition, we have also added Arnite LDS grades with are polyester based. This gives designers a complete portfolio to select the material matching best to application requirements and taking extra care of the environment.
How do you see the role playing out for engineered plastics in alternative and future mobility concepts?
Engineering plastics are becoming even more relevant when it goes towards integrating more electronics into future cars. Higher assembly temperatures through the move to reflow soldering, environmentally friendly halogen-free plastics, plastics with higher flow to enable miniaturisation. Such requirements will become as common as in consumer electronics. We also believe that on the mid to long run more flame retardant plastics will be required with the advance of electrical cars as a car will basically needs to be treated as an unattended appliance product during the charging, so requirements such as flame retardant or glow wire performance may become common requirements for major parts of automotive electronics.
Next to that the electrification of the drive train plays an important role, i.e. hybrid and full battery electric vehicles. DSM is working closely with OEMs on the next-generation high-voltage e-motors, which require different materials than the current generation due to higher thermal loading and more challenging design space. Mechanics, flowability, thermal conductive and insulation properties need to be well balanced.