
Covestro AG (which emerged from Bayer MaterialScience AG in 2015) brings new high-tech materials from the product areas of polycarbonates, polyurethanes, coatings and films into play. Continuing just-auto/QUBE's series of interviews, we spoke to Ciro Piermatteo, Global Technical Marketing Mobility and Christoph Klinkenberg, Global Technical Marketing Mobility Exterior, Covestro about the application of polycarbonates for future mobility concepts.
There is a lot of talk about the autonomous car, specifically larger displays and touchscreens. In what ways can Covestro support this?
Due to the trend towards autonomous driving, the automotive interior is evolving into a multifunctional living space with 'function on demand' concepts. As part of this, the number and size of displays and touchscreens in car interiors is expected to increase due to the progressing digitisation and networking (connectivity).
This trend offers great opportunities for the use of polycarbonate resins and films from Covestro. For example, they enable large surface, three-dimensional screen designs that can be seamlessly integrated into the surfaces of instrument panels, centre consoles, door and seat panels.
In addition, polycarbonate resins can be used for novel ambient and dynamic lighting elements for the car interior, e.g. light guides.
What new and potential automotive applications are there for polymers?
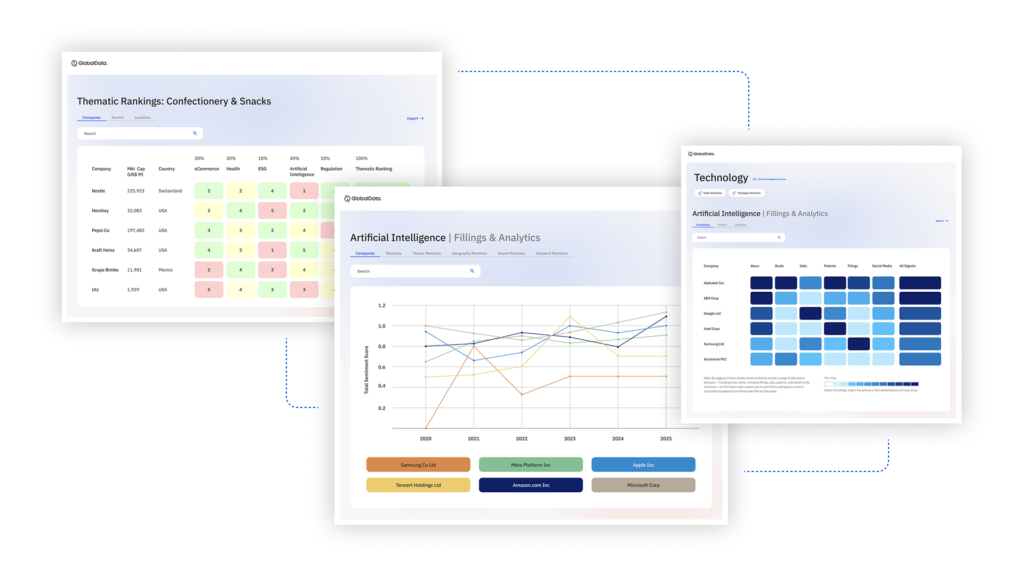
US Tariffs are shifting - will you react or anticipate?
Don’t let policy changes catch you off guard. Stay proactive with real-time data and expert analysis.
By GlobalDataMany of the functionalities of future mobility are derived from electrical and electronics applications of polymers like polycarbonate, whether it is about electric drive or battery technology, sensor technology, connectivity or artificial intelligence. For instance, recent developments with polycarbonate have led to an improved surface appearance of car body parts.
A new car concept of Covestro presented at K 2016 fair also revealed new design possibilities by usage of transparent Polycarbonate for body parts like black panel effects.
Furthermore such parts can contain colour-patterns, 3D-effects or backlit structures which benefit from the glass like depth-effect of the transparent polycarbonate.
How do you see the role playing out for engineered plastics in alternative and future mobility concepts?
Based on Covestro´s long-term experience in polycarbonates and due to the outstanding, e.g. glass-like properties of this engineering thermoplastic, it can also serve as a key material for the new mobility.
One example is the seamless glazing of injection-molded elements and the integration of vitreous body parts. The use of polycarbonate combines design freedom and functionality with safety of passengers and other road users. For example, seamlessly integrated LED lighting concepts and front elements that are highly permeable to infrared (IR) radiation from LiDAR sensors also contribute to this, as well as a new wrap-around glazing concept.
Another trend will be installing displays in the auto exterior for car-to-human communication. This might contain expressions of the driver's mood …
Another trend will be installing displays in the auto exterior for car-to-human communication. This might contain safety-relevant messages as well as expressions of the driver's mood or simply advertisements in case of shared vehicles. Such displays have to be covered by a transparent, impact- and scratch resistant material like coated polycarbonate.
The automotive polycarbonate glazing market penetration has been slow and limited. Laminated glass is now lighter and more formable. Further advances have been made to chemically toughen glass, too. So has the big push for polymer glazing gone away?
The mentioned new possibilities in glass don´t come for free and first have to show their value-for-money performance in mass-produced cars in the coming years.
Polycarbonate is ideally suited for automotive glazing due to its high transparency, low weight, freedom of design and strong impact resistance.
Polycarbonate is ideally suited for automotive glazing due to its high transparency and clarity, its low weight, huge freedom of design and strong impact resistance. Recent developments even increase its suitability for this application, e.g. the modified UN 43R regulation, which opens up possibilities for designing windshields from polycarbonate, by that allowing for a 360-degree wrap-around glazing, as demonstrated by the car concept we have showcased at K 2016.
With regard to alternative drive concepts like electric mobility, the excellent thermal insulation of polycarbonate will play a more important role in the future. A thermal management based on an improved thermal insulation of the car interior will reduce the energy consumption of the air conditioning or heater and thus extend the range of electric cars.
Furthermore, the trend for large transparent glass-like surfaces in the auto exterior like the former radiator grille area will require coated polycarbonate – this will push the PC glazing market eventually as well.
In terms of applications, where do you see the opportunities for polycarbonate glazing on passenger cars? And do you see it limited to aesthetic glazing, such as sunroofs?
New mobility concepts will open up entirely new applications for polycarbonate.
Besides traditional passenger cars, new mobility concepts like shared electric vehicles which drive autonomously [will] open up entirely new applications for polycarbonate. This will contain transparent glazing as well as glass-like, design-driven body panels which are hiding technology like sensors and cameras in an invisible and seamless way.
Where do you see the greatest opportunities/ applications for carbon fibre in mass-produced cars?
Composite materials made of continuous fibre-reinforced thermoplastics already play an important role in the automotive business. They contribute to climate protection and resource conservation by simplified and highly integrated processes, by that reducing energy consumption and offering powerful sustainability opportunities.
Particularly with the use of polycarbonate-based composites, it will become possible to combine aesthetics and semi-structural properties in one part: light, strong and beautiful.
Diverse market segments, among them the electrical and electronics industry, but also the automotive business, are looking for even stronger and lighter materials than before. Only recently, Covestro started commercial production of continuous fibre-reinforced thermoplastic composites (CFRTP) in southern Germany.
It appears that processes to manufacture carbon fibre have moved faster than those for recycling it. Are there still challenges when it comes end of life recycling of carbon fibre parts?
In principle there are different possibilities for a recycling of CFRTPs. For thermosets it can be e.g. pyrolysis or solvolysis – these technologies reduce the technical properties of the fibres.
Thermoplastic materials do have different options for recycling – they can be re-melted, cut into flakes for high-performing forged carbon applications or ground to be used for compounding and many more applications.
However, for the choice of the most suitable method, ecological and economic factors always need to be taken into consideration, as well as legal regulations.
A major advantage of CFRTPs is their high durability so that users can expect a long service life of their products.
What other trends are you seeing with respect to lightweighting using composites in vehicle manufacture?
In general, plastic composite materials enable a lightweight construction of cars, by that reducing energy consumption and – in case of electric vehicles – extending their range and by functional integration simplify the cars assembly and have the potential to reduce assembly costs.
In addition, polycarbonate based CFRTPs are able to realise class-A surfaces so they can put structural properties onto a visible part.
Given that composites are robust and offer freedom of design, they will play an even more important role in future mobility.
Furthermore, composites are robust and offer much freedom of design. Due to these properties, they will play an even more important role in future mobility.
Which automotive applications are the most promising for 'smart materials'?
We believe that the automotive car body of the future will be characterised by an extended use of plastic parts with multifunctional glass-like surfaces, which are seamlessly integrated into the outer shell. New tailgate concepts based on PC and even a wrap-around glazing offer possibilities for additional weight savings, a higher freedom of design and the integration of further functions and not least an economic production using two-component injection molding.
Instrument panels, centre consoles and back seat covers will receive new digital surfaces with integrated functions.
The integration of light and functions opens the door to innovative interior parts. Instrument panels, centre consoles and back seat covers will receive new digital surfaces with integrated functions. Polycarbonate will enable the implementation of high-gloss and matte adjacent surfaces, projecting surfaces or advanced lighting elements.
Another focus is the integration of innovative light concepts based on energy-efficient LED lighting technology. New functionalities and design options will not only be used in the classical headlight and rear light areas, but also for larger exterior parts of the car body. For this purpose, new plastic optical components will need to be integrated into plastic parts.
Autonomous driving, in particular, will require the integration of a multitude of sensors, operating with different measuring principles, e.g. LiDAR systems. For these requirements, Covestro has developed a polycarbonate colour concept, which offers a maximum degree of IR transmission.