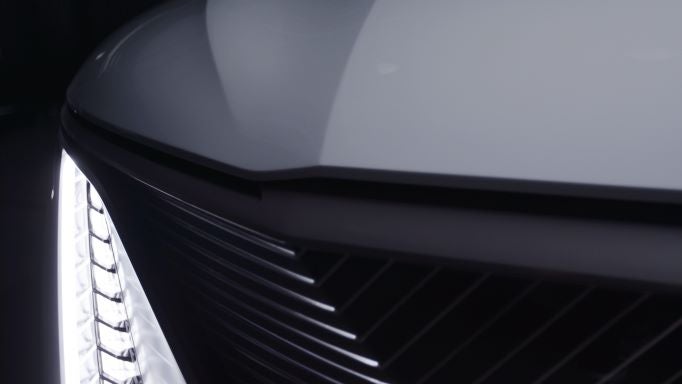
Some EVs aim to offer long driving ranges or rapid acceleration, but a growing number are leaning into the luxury angle as a means to draw in potential buyers. Models including the Lucid Air and Mercedes EQS are emphasizing their larger interiors compared to ICE luxury cars, made possible by using a BEV skateboard platform. Equally most range-topping EVs come with powerful yet silent battery-electric powertrains, further enhancing their luxury image.
Packing luxury features into EVs allows automakers to sell a smaller number of vehicles at a higher price with a greater profit margin compared with mass-market models. This strategy is well suited to BEV models that typically cost more to build than an equivalent ICE vehicle, and means current cell supply constraints will have less of an impact on production numbers.
Into this environment, Cadillac plans to launch the 2023 Celestiq – a new luxury flagship sedan for the historic American brand. Little is known about the Celestiq other than the scant details Cadillac announced in a recent press release, however, there are some significant clues in the reveal that indicate what to expect from Cadillac’s latest standard-bearer.
It will use 3D printed components
Additive manufacturing, more commonly known as 3D printing, is a manufacturing technique that gained more favor in the 21st century thanks to several advantages. Benefits include the ability to design and print parts with extremely complex internal and external geometry that would be prohibitively complex to achieve through casting or milling. These parts can display impressive strength and weight properties thanks to using structural designs inspired by nature that would be extremely difficult to replicate with conventional strategies.
However, for all the bluster, 3D printing has not become a mainstay in mass-produced vehicles. Several reasons can explain this, with the most pressing issue being the time taken to painstakingly print each piece which, compared to stamping or casting operations, is far longer. This slows the build process, thus adding cost and complexity when utilizing a stamped or cast part would be far faster and cheaper overall. Another issue limiting the application of 3D printing, especially for metal parts, is the fact that many additive printing methods risk creating occlusions (small voids or gaps) in the part’s structure, making it unsuitable for applications where high strength or malleability is required.
How well do you really know your competitors?
Access the most comprehensive Company Profiles on the market, powered by GlobalData. Save hours of research. Gain competitive edge.
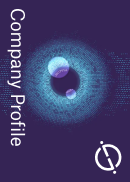
Thank you!
Your download email will arrive shortly
Not ready to buy yet? Download a free sample
We are confident about the unique quality of our Company Profiles. However, we want you to make the most beneficial decision for your business, so we offer a free sample that you can download by submitting the below form
By GlobalDataGM plans to have more than 100 individual 3D printed parts in each Celestiq, encompassing both structural and cosmetic parts, made from both plastic and metal. This suggests GM is willing to accept the trade-off between the cost and complexity of utilizing 3D printed parts in order to leverage their unique look, feel and structural properties in the Celestiq.
It will be, to some extent, hand built
Vehicle assembly, especially at the mass-market end of the sector, is a prime example of heavy automation in manufacturing. Production lines are commonly kitted out with many highly accurate, fast-acting robots which enable the rapid and repeatable production of high-quality vehicle parts at a low enough cost for mass-market vehicles.
Conversely, hand assembly is usually associated with low-volume production of expensive and high-end products. This is a means to achieve the extremely fastidious levels of quality control expected with costly, low-volume, luxury products but, naturally, means each part or vehicle will cost more and take more time to produce compared to a robot-assembled vehicle.
It will be built at a facility not previously used for vehicle assembly
Joining GM’s unconventional decision to deploy both 3D printing and hand assembly to the Celestiq’s production line is its choice to set up that line in GM’s Global Technical Center in Warren, Michigan. This will make the Celestiq the first-ever vehicle to be manufactured at that facility, which is more commonly tasked with the automaker’s R&D efforts.
What this tells us about the Celestiq…
The points highlighted here clearly hint that the Celestiq is not going to be ‘your average Caddy’. GM’s decision to 3D print several components, along with utilizing hand assembly at a facility more commonly associated with R&D efforts than fullscale vehicle production, strongly suggests the Celestiq will be a low-volume, ultra-luxurious flagship model. This will likely entail very low annual production numbers, and a price well into six-figure territory as befits a true flagship model.
This article was first published on GlobalData’s dedicated research platform, the Automotive Intelligence Center