Long gone are the days of providing “best guess” assembly plans. Today’s virtual reality-based software systems provide a way to assemble components and correct mistakes before a part is even prototyped.
Once, engineers had to use bits of cardboard and paper to create layouts for assembly processes. Problems like the parts not fitting together, or access holes being too small for assemblers to reach into were worked out on the factory floor, which usually involved stopping the line and costing considerable amounts of money. But advances in computer technology have given us a “virtual world”, where engineers can use digital models in place of cardboard and paper.
Several software companies are providing the tools to create virtual assembly processes. Granted, when the first virtual assembly software models hit the market, they were mostly high-tech smoke and mirrors. Two-dimensional pictures allowed users to create a sort of map of what the factory floor would look like, but there was no animation, and no way to simulate actual parts moving through the process of being put together. These early models only provided a computerized “best guess.”
Since then, simulation systems have evolved to the point where they let designers use actual CAD data to exactly simulate parts. And animation allows virtual people or robots to actually perform tasks. Problems such as collisions, bad fits, and poor access to work areas are highlighted.
On the Menu
There are several features that most assembly simulation packages offer. Editable animation, integration with an organization’s product data management (PDM) system (for automatic part design updates), various options for input formats, 3D graphics, and a Windows or Windows-like environment to name a few. Especially important to simulation software programmers is CAD integration. Most do not use intermediate files such as .DXF or .IGES files. Too much data is lost or mistranslated, they say. “Direct CAD interface is key”, says Eric Jacobs, manager of simulation products at Silma Div. (San Jose, CA). “Then the simulation package becomes the `owner’ of the data. There’s less room for error.” In other words, the CAD data becomes native to the system as it is introduced and used.
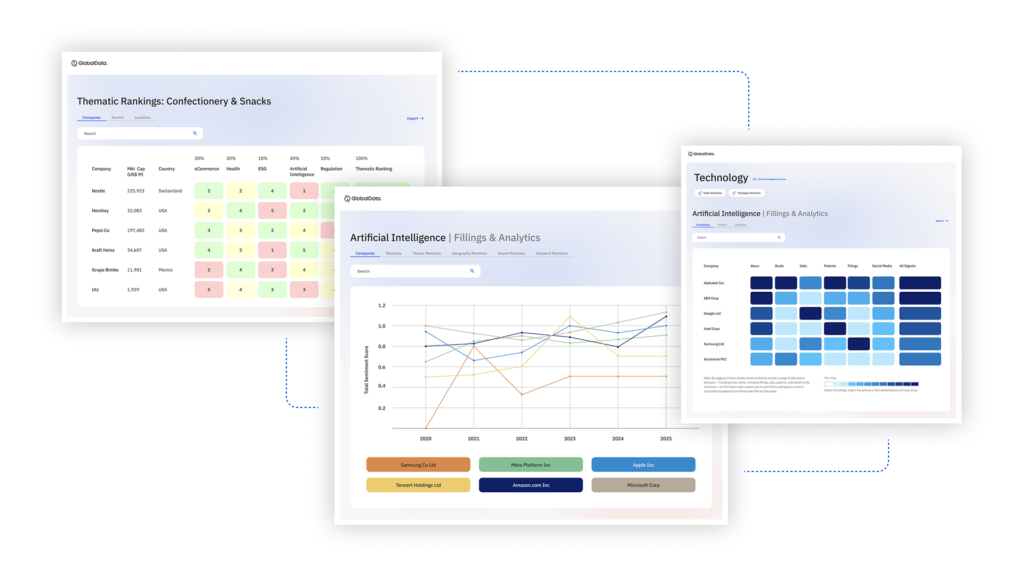
US Tariffs are shifting - will you react or anticipate?
Don’t let policy changes catch you off guard. Stay proactive with real-time data and expert analysis.
By GlobalDataEach software developer also breaks from the crowd with one specialty or another. What potential users opt for will often depend on what “specialty” they are looking for. Tecnomatix (Novi, MI) distinguishes itself by being one of the forerunners of simulation software systems, offering one of the more sophisticated systems on the market. They work with several automotive manufacturers and their suppliers to create simulation software capable of mimicking both manufacturing and assembly processes.
“CAPEd” Crusaders
Tecnomatix uses the phrase “computer aided production engineering” (CAPE) to describe its software systems. The company’s software is based on the idea that all aspects and areas of a manufacturing facility can be harmonized through a virtual manufacturing environment. It has software to simulate every part of the production process, including machining, inspection, assembly, and packaging. For assembly, the company offers Dynamo, a tool that allows users to look at assembled parts. When used with RobCAD, users can create pathways to define the process of assembling parts, and look at their relationship with each other once assembled. CAD data is used to check assembly and production constraints. Pathways can be defined, enabling engineers to take a 3D look at how a robot or a human would assemble parts. Dynamo then looks for collisions and other factors once the parts are put together.
Design errors at this point can easily be spotted and adjusted. As an example, Tecnomatix uses a demonstration of an animated simulation of a human model inserting a door latch into a rear car door. Based on what was displayed, engineers determined that the access hole on the door panel was too small for the model to reach the appropriate position. This conflict was flagged and sent back to design, where the hole was enlarged.
As conflicts like this one are highlighted and corrected, the changes made are saved into the system’s database, which fully integrates into an organization’s existing PDM system. “With a lot of systems, you have to remember to incorporate changes into the PDM as well as the simulation system,” says Darrell Bozeman, technical director at Tecnomatix. “We decided that it would be confusion down the road.” The database can also be expanded to include new equipment or situations as they are added to an organization.
The Dynamo software system also features a disassembly module that lets engineers take an assembly apart once it is put together and integrated into the vehicle. Tecnomatix software engineers consider this important for a couple of reasons. First, it points out possible serviceability problems. If the oil filter won’t easily come out of a car, it could be a costly error for both the car maker and the car owner. Secondly, the module can be used to create animated illustrations of how a part should come out of the vehicle for servicing that can be used by service technicians.
People Matter
In the example used previously, the human model and the motions it made were created using RobCAD/Man, a module within the system that simulates human actions. While other simulation software makers feature similar modules, Tecnomatix provides the ability to create both a female and male model. Both feature the average height, weight, and reach characteristics of the given gender. “From what we know, only 5% of the workforce on an assembly line is female,” says Bozeman. “But they have to be considered. What if a part was too heavy for a female to lift? This way, at least you’d know ahead of time so she could be accommodated.”
Much of the path generation is automated, and both fixed and variable paths can be created. In the case of the door latch, only one discreet path is available, while others may have various possible scenarios.
The ability to simulate human actions also allows users to look at the ergonomics of a process. If a person would be bending too much to perform an operation, perhaps a robot would be better suited for the task. While it appears that no other simulation system features both a female and male model, there are other systems that have the ability to simulate human actions.
This is where Deneb Robotics, Inc. (Auburn Hills, MI) distinguishes itself from other simulation systems. The company programs Deneb/Ergo, a module for its Deneb/Assembly software system. Ergo includes the ability to include curved path walking, and a quick-pose feature for generating adjustable postures for sitting, standing, and stooping. Deneb/Ergo goes even further by examining the variables surrounding human actions. For example, NIOSH multi-task analysis lets engineers take a look at the risks involved in two-handed lifting situations. There is also an analysis tool that evaluates the amount of energy a person would use performing high exertion tasks, as well as one that evaluates working postures to determine the risk factors involved with upper limb disorders that could evolve as a result of a specific action (such as carpal tunnel syndrome). Tools like these make it easier to determine how long it would take a person to complete a task, and at what risk. In the end, the engineer may be making a more informed decision in opting for a robot to perform a task rather than a human.
Robotic Concerns
As much as people are still involved in assembly, lines are becoming more and more automated as equipment becomes more sophisticated. With this in mind, the Silma division of Adept Technologies, Inc. (San Jose, CA) has developed software that focuses on automated assembly lines. Adept Rapid and Soft Assembly let users build robotic models based on attributes. For example, the Parametric Peripheral module allows the input of a type of assembly tool, such as a gripper. From there, graphics are automatically generated, based on the input. This enables the building of models based on what the robot needs to do. From there, Smart Swap then lets users exchange the generic input for actual equipment once it has been determined what capabilities are needed. If the organization does not have a robot fitting these characteristics, the engineer is alerted, and can reconfigure the process.
The simulator also allows the consideration of how the parts move from task to task. Physics-based simulation modules simulate CAD-based models dropping onto conveyor belts, analyzing how they would land, and how this would effect the movements of the next robot in the line. Actual distribution of parts on the conveyor is also automatically calculated.
“Our typical user is an assembly system integrator,” says Eric Jacobs. “They’re building systems for automakers, so it is important to be as exact as possible before a system is put together.” He goes on to explain that the software lets integrators model how the system will wire into the controller, making on-site installation even simpler.
Future Applications
Working within the world of virtual reality to iron out potential real-world problems has so far saved both automakers and suppliers untold amounts of time, effort, and money. The next step is to be able to pass simulations up and down the supply chain, which is already in the works. Automakers also want to be able to take this
technology beyond making cars to repairing them as well. “They want to be able to use these simulations to set up a virtual training manual for repair technicians,” says Darrell Bozeman. “That way they’ll know exactly how to take components apart to repair them.” Looking far into the future, programmers look to the development of artificial intelligence kernels that will set up assembly processes based on CAD drawings, and send them right to the factory floor. Then there won’t even be people involved in design for assembly, much less cardboard and paper bits.
![]() |
The effects of tolerances and sequence can be evaluated using Valisys/Assembly by Tecnomatix. Key characteristics are highlighted so engineers can check and adjust them as needed. |
![]() |
RobCAD aids in designing both manual (human) and robotic tasks in the assembly process. |
![]() |
Here, Deneb Assembly walks users through the layout of an assembly line. Where certain parts will be inserted is highlighted, as well as where control boxes will be placed, and what they will be controlling. |