In Smartville, they build more cars per person than even Nissan’s UK plant in Sunderland – but the factory, close to the French and German border at Hambach, does not even figure in the league table for productivity. Currently rated at number one in the annual survey by the World Markets Research Centre’s list of Europe’s most productive car factories, Nissan makes 99 cars per employee a year. In Smartville, writes Chris Wright, they make 140 . . .
So is plant manager Klaus Fischinger downbeat? Not at all. He is content that he is running one of the most innovative car factories in the world – so innovative that it puts itself out of the running for the WMRC list.
“Our production process means there is no stamping plant on site and no conventional paint shop,” said Fischinger. “Panels are individually sprayed rather than painting the whole body-in-white.” According to productivity researchers, this makes comparing Nissan in Sunderland to Smartville in Hambach like comparing apples with pears.
Fischinger added: “To be fair, if we evened things up we would probably be producing around 90 cars per employees so we are always looking for improvement.”
Formerly the project manager for the Smart Roadster, Fischinger now has to build the car and he admits that he is happy being involved in the ‘fun’ side of DaimlerChrysler. The idea of sharing the assembly responsibility with supplier partners was revolutionary and has been ultimately successful, although Fischinger said there were doubts in the beginning.
“Each company has its own philosophy and each was worried as to how that would correspond. We meet every month to discuss how we have been doing and how we plan to work in the following month.
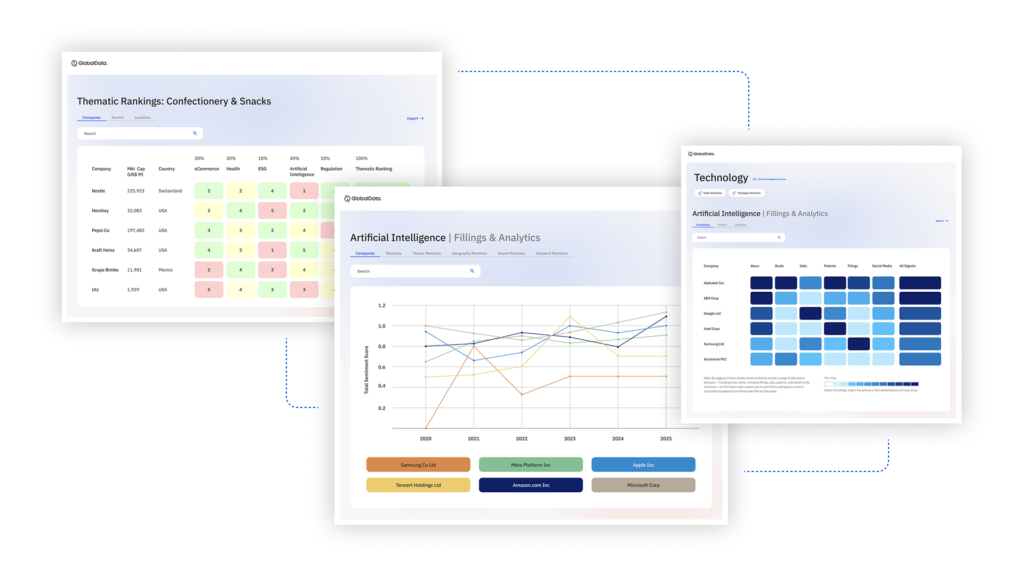
US Tariffs are shifting - will you react or anticipate?
Don’t let policy changes catch you off guard. Stay proactive with real-time data and expert analysis.
By GlobalData“We get a number of visits from other vehicle manufacturers to look at what we are doing here, especially from within the DaimlerChrysler Group. Plant managers have been coming over from the United States, and Jeep has been especially interested in what we are doing.”
Things have moved on from when the Smart factory started up in 1998. There was then just one model line and a choice of four colours for the plastic body panels. Now with the Smart fortwo and cabrio plus the Roadster and Coupe, the original 250 part numbers have grown to 2,000 and there is much more complexity in the number of specifications.
“We have grown up very quickly,” said Fischinger. “Originally cars were actually completed at the Smart Centres, but we now do more work at the plant, fitting the radios etc because we and our supplier partners have refined and optimized the manufacturing process.”
Luxury specification such as ESP, leather seats, heated seats, and high performance Brabus engines are just a few of the items now finding their way into these tiny city cars.
There are 2,200 employees in Smartville, so called because the plant comprises 14 buildings and is shared with six systems suppliers, Magna Chassis & Uniport, Surtemal/Eisenmann, Siemens VDO, Dynamit Nobel, Cubic Europe and Thyssen Krupp
Hambach, in the Lorraine region of France, was chosen because DaimlerChrysler wanted the plant located in the middle of Western Europe. The plant is 10kms from the German border. It is an area that has changed nationalities several times through history, and while 95 percent of the staff are French, most speak German.
Total investment in the plant stands at more than €500 million, including all systems suppliers. Wages in Smartville are the same whether you work for Smart or one of its partners, only the benefits may be different.
Body panels are produced by Dynamit Nobel where general manager Hartmut Hensel boasts that there is virtually no waste. Plastic is recycled and used on black parts which are not seen on the car while even the paint changes are used to create some of the weird and wonderful dual colours for some of Smart’s unique body panels – this negates the need to completely clean out the paint tanks at the end of each colour run.
Between 10 and 12 percent of all panels made are for the aftermarket or replacement – not necessarily because they are damaged, but so that people can change the colour of their car. A complete set of panels costs €500 and can be changed within 35 minutes – all you need is a screwdriver.
Another innovation is that nothing actually belongs to Smart until the car is signed off the line. It is when the bar code is scanned that suppliers are paid.
Theoretically the factory owns the car for just a few minutes before responsibility is handed to Mosolf, the distribution logistics provider. In fact the plant usually hangs on to the vehicles for a day to give it a re-work buffer.
Smartville is something of a co-operative. Damage on the line is not monitored unless it is really obvious. Problems are cured at the end of the line.
If a single fault is discovered, none of the suppliers get paid, although ultimately Smart takes its share of the ‘blame’ for any problems. Too long in the re-work zone and all staff start to lose bonus.
Bonus is paid according to delay, quality and cost. If everything runs properly, then everyone gets a bonus.
While there is room for expansion, Smart’s new forfour will be build at Born in the Netherlands, a plant shared with Mitsubishi. This is not the last of the line, however.
Smart plans to launch an assault on the North American market in 2006 with an all-new SUV, and it will build this car in Brazil.
The plant at Juiz de Fora, north east of Sao Paolo, currently produces the Mercedes-Benz A-class but will become the centre of worldwide production for the SUV.
According to Helmut Wawra, Smart’s head of design and engineering, most suppliers for the project will be European.
“Because of the size of our engineering department it is important suppliers have the ability to carry out engineering work close to us in Germany and have plants in Brazil, this is the case certainly for the tier 1 suppliers.”
The United States will be the main market for the Smart SUV taking 50 percent of production. Wawra said: “It will obviously be a very important car for our brand because it will be the first Smart car in that market. With the federal regulations involved we will not be introducing any other Smart products there until the next generation City Smart (now called fortwo).”
Between now and launch at the Detroit Auto Show in 2006 there are a lot of tests to be passed to meet US Federal regulations. “Emissions tests are particularly time consuming and it is a challenge to squeeze it all in to the time schedule,” added Wawra.
He said that Smart would not have its own retail chain in North America but will almost certainly use the Mercedes-Benz network. “Our colleagues at Mercedes-Benz have a lot of experience in the North American market from things such as Federal regulations to the special expectations of the consumers in the United States.
“When we introduce the SUV it will be a small car with some special design features but it will be instantly recognisable as a Smart and that is what we are working on right now.”
![]() |
Smart roadster is being built at Hambach. |
This will include the Smart DNA: Two tone colour, the combination of steel and plastic, interior textiles use and the unique shape and features of the instrument panels
Wawra added: “We have to look at all the expectations consumers have for an SUV and apply them to our brand. At the moment people in the United States have no expectation of what Smart is.”
What happens beyond North America? Does Smart start to attack the fast-emerging Chinese market?
Wawra said: “With the fortwo and Smart Roadster we have special answers to special questions. They are not necessarily an answer to mobility. In China there is a need for commercial vehicles, pick-ups or family cars.
“The forfour or SUV might start providing some answers for them in the future. In Europe the Smart is the second or third car in the family, with the forfour and the SUV we can start thinking about making it the first or second.
Will this mean the family is complete? “We have no concepts in mind but we have been working very intensively with only a small pool of people, just 600 engineers. We have to be thinking about the new generation fortwo.”
Smartville and its history The decision to establish the production facility in Hambach was taken on 20 December 1994, and the foundation stone was laid in Europôle des Sarreguemines on 14 October 1995. Around 70 locations were examined prior to the decision to site production operations in Lorraine. DaimlerChrysler says that positive aspects which prompted the decision in favour of Hambach were the location’s good accessibility at the heart of Europe and the French authorities’ “swift and unbureaucratic approval procedure”. The region also offered DC a large qualified labour force with whom it furthermore proved possible to agree flexible arrangements on working hours. The cross-shaped “smart Plus” factory was completed after an 18-month construction period. The official inauguration on 27 October 1997 was carried out by the then German Chancellor, Helmut Kohl, and French President Jacques Chirac. Smartville’s unique factory concept ensures a maximum distance of ten metres between a component’s delivery point and the assembly belt. The vehicles pass through the 140 assembly stations in just four and a half hours. The factory’s modular design reflects the concept which applies to all smart vehicles. |