Although the idea of replacing vehicle glass with lighter weight plastic sounds like an obvious innovation, it is not new. For over thirty years, auto glass experts have explored the potential for polycarbonate as a replacement to glass. Matthew Beecham reports on how the polycarbonate auto glazing market is taking shape.
Compared to the shape limitations of glass, polycarbonate glazing is highly versatile. It is also lighter by as much as 50% and has high impact resistance. Automakers can now consider 3D-shaped windows, innovative designs and locations and new opening and closing mechanisms.
In terms of the opportunities for polycarbonate glazing in the automotive industry, Dr Klaus Badenhausen, director, chief-engineer A-/B-class, Smart, believes that panoramic roofs, backlites and tailgates are good examples. He told us: “High quality exterior trim parts like roof spoilers with integrated stop lights and quarter rear lights can be made out of polycarbonate. The material is opening up promising perspectives due to its low weight, high robustness and proper physical characteristics such as impermeability against ultraviolet as well as absorption of infrared light etc. These properties predestine polycarbonate as a first class alternative for transparent roofs: It helps lowering the vehicle’s centre of gravity and proves to be impact resistant. The degree of freedom in terms of design is higher compared to glass.”
Bayer Corp’s subsidiary, Bayer MaterialScience is pushing back the technical boundaries of polycarbonate glazing. Bayer MaterialScience’s Makrolon polycarbonate glazing has commercial applications in several vehicles including the Porsche Carrera special edition back window, Mercedes-Benz C Class sports coupe transparent body panel, Smart Fortwo rear window, and Smart Forfour panoramic roof and rear window. The company says it has a close-to-production prototype of a highly integrated lamella roof based on its polycarbonate Makrolon material. The company points out that the roof’s special feature is that it incorporates transparency sealing, opening and closing functions in a single plastic component that can be manufactured in one process step. “This lamella roof with a plastic-compatible design primarily represents an alternative to conventional fabric or PVC-based sliding and folding sunroofs,” said Florian Dorin, a specialist in Bayer MaterialScience’s automotive glazing team. “We have incorporated cost-effective production technologies in this project and also given the prototype component a close-to-production design so that we can move straight to concrete projects with system suppliers and OEMs.”
Exatec, a wholly-owned subsidiary of SABIC Innovative Plastics, is another front runner developing polycarbonate glazings. “Over the past 12 – 18 months, we have seen a very active market place with certain OEMs working with us toward creating specifications for PC,” said John Madej, CEO, Exatec. “It has been a necessary step to go through. It means that OEMs can move beyond the weathering question [of PC] and ask: what is the NVH on a vehicle when we have PC versus glass? What is the solar load difference between a PC roof and a glass roof? We have seen a huge increase in requests for full prototype parts over the last 18 months. That tracks very closely the work that both my team and Derek’s [SABIC Innovative Plastics] team are doing at the OEM’s on polycarbonate specification. Once that happens – and in some cases, we are already there – then we reach the point when OEMs are putting out requests for polycarbonate for real cars, not just concepts.”
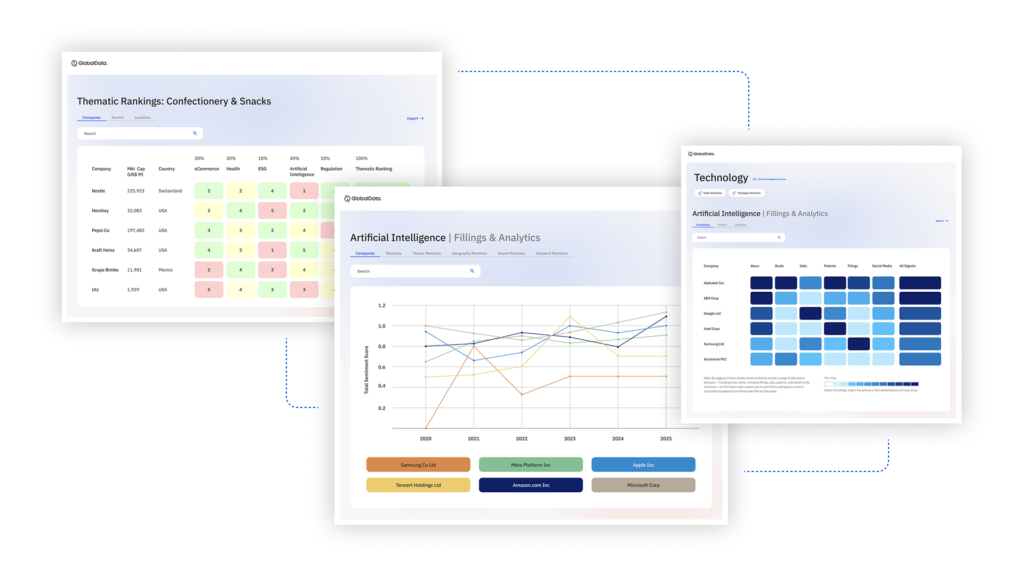
US Tariffs are shifting - will you react or anticipate?
Don’t let policy changes catch you off guard. Stay proactive with real-time data and expert analysis.
By GlobalDataOn the flipside, there are still a number of issues to address when automaker’s consider the use of polycarbonate automotive glazings instead of glass.
Although the cost of polycarbonate glazing relative to tempered glass is still a concern, its cost compared to laminated glass is reckoned to be more palatable to automakers. Badenhausen said: “Plastic glazing obviously is more expensive than single pane tempered glass at present – but less so compared to laminated glass. Polycarbonate has got the potential to replace conventional car glass, wherever its properties will prove advantageous. The costs of polycarbonate are limiting the application to areas, where the manufacturer definitely decides to spend money on. The material being derived from oil, its price is related to this valuable resource. High quotes must be expected.”
In explaining the cost difference between a laminated and polycarbonate roof, Madej said: “There are a lot of different flavours. In general, if you compare a flat piece of tempered glass with a flat piece of polycarbonate, then it is twice as favourable to use glass versus polycarbonate in terms of cost. But if you compare a piece of laminate with PC then — depending on the brand of laminate and the thickness of the PC piece – the costs of those two materials are actually similar. At that point, OEMs begin to consider other factors such as the fact that glass does not allow you to integrate anything whereas polycarbonate does. Therefore by using a PC piece on the roof can help the OEM save costs.”
While the cost issue appears to be diluting, albeit for certain applications, polycarbonate glazing is more easily scratched than glass. However, various coatings can make polycarbonate glazing more scratch-resistant, as Volkhard Krause, head of the Automotive Glazing Team at Bayer MaterialScience told us: “We have performed a number of different tests which demonstrate that scratch resistance, especially for roof systems, is not a problem. For example, we have simulated a vehicle with a wet coat PC roof going through a car wash once a week for two years. As a result of such tests, we do not see any problems with the currently available wet coat systems. As far as fixed side windows are concerned, scratch resistance is not really an issue. There are already fixed side windows in production. The first application for fixed side windows started already in 1998 for the Smart ForTwo.”
Volkhard adds that a drawback for polycarbonate for moveable side windows relates to the actual stiffness of the material. “There is a huge difference in stiffness when comparing polycarbonate with glass. Glass has a much higher modulus than polycarbonate. This is the reason why it will be difficult to use polycarbonate for moveable side windows in the next ten years. What we need to do – not just BMS but all the development companies – is to develop completely new door modules to integrate those moveable polycarbonate side windows into them. As long as we do not have that available [to us] then polycarbonate is not a suitable a material for moveable side windows. We are, however, working on a number of long term pre-development projects to overcome this. For rear windows there must be included different functions into the polycarbonate window, in order to meet OEM’s requirements and to be cost competitive. There are different technologies available which allow us to achieve that. We are working on that.”
While polycarbonate glazing has been around for decades, auto industry concerns over material cost (relative to glass), scratch resistance, weatherability have held back its use. However, it’s clear that some companies have managed to push back the technical boundaries making the material a real alternative to automotive glass, albeit for certain applications. Weight savings is another driving force behind the growing popularity of polycarbonate glazing, especially for large roof applications.