Ignition system technology has taken a number of twists and turns over the past 50 years. Matthew Beecham talks with experts from Delphi and Denso about the latest developments both on the OE and aftermarket side of the sector.
In the late 1940s and 1950s, the ignition unit consisted of an ignition coil and distributor that delivered the voltage generated by the ignition coil to the ignition plugs. Following this product, mechanical power distribution evolved into electronically distributed power.
By the early 1980s, the integrated ignition assembly appeared, combining the distributor, ignition coil and driving circuit (igniter). This basically eliminated the need for a high-voltage cable between the ignition coil an distributor, thereby further improving product reliability.
During the mid-1980s, distributor-less ignition appeared. High-voltage generated by the ignition coil was directly applied to the ignition plug. The distributor was eliminated resulting in a lighter unit. Product reliability was further improved by electrically controlling high-voltage distribution and ignition timing.
By the mid-1990s, the stick coil began to appear featuring a smaller igniter. Today, there are basically three categories of ignition systems: coil ignition, capacitive discharge ignition, and other types such as AC-Ignition. Coil ignition is the most popular system.
In terms of market drivers, Peter Weyand, engineering manager ignition, Europe, Delphi, believes that the most important factor that drives the design of an ignition system today is the combustion system. He told us: “Some of the advanced combustion methods like homogeneous or stratified direct injection, or highly dilute (lean and/or high EGR) combustion have requirements that cannot be addressed any more with comparably simple ignition systems. Smart ignition systems have thus been developed. The first step to a smart ignition was an improved self-diagnostics and feedback of ignition current and voltage waveforms to the ECU. These offer information regarding the combustion event.
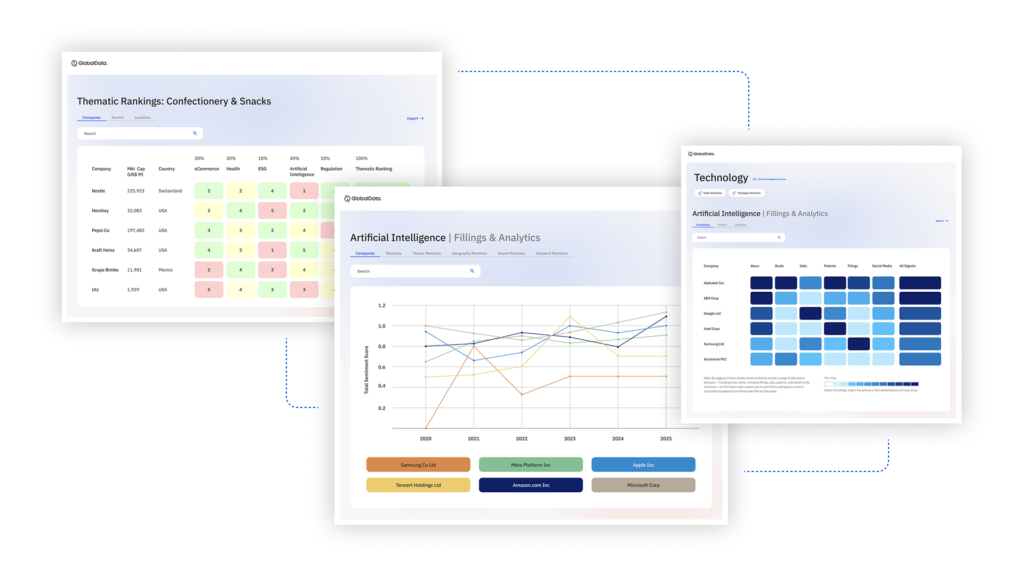
US Tariffs are shifting - will you react or anticipate?
Don’t let policy changes catch you off guard. Stay proactive with real-time data and expert analysis.
By GlobalDataEspecially for combustion methods that have a less predictable cycle to cycle behavior, like GDI, this immediate insight helps the ECU control strategy. The most advanced systems are using this combustion information to adjust the actual ignition algorithm “on the fly”. These systems are usually MultiCharge Ignition systems or their derivatives that fire several times to increase the probability to even ignite mixtures under severe air/fuel ratio conditions. Ion sensing capable ignition systems or quasi alternating current systems are addressing certain problems that are not or barely resolvable with a standard single spark system.
Shin Nishioka, spark plug engineer, Denso Europe BV, business unit aftermarket, points out that trends in engine design mean that more and more discharge energy is required these days in order to secure stable combustion. He told us: “This is probably the biggest challenge for ignition coil development at present.”
There is also a clear trend toward increasing energy requirements. “Stratified GDI is clearly the main driver, but turbocharging is also a contributor,” added Weyand. “Downsized, turbocharged engines require higher ignition voltages with a corresponding need for increased ignition energy to sustain a long-lasting spark. Instead of large high energy coils, Multicharge Ignitions provide a smarter way to deliver the required energy within several pulses from smaller and lighter coils. So to say, while GDI was the starter of high energy ignition systems, downsizing is now taking advantage of the achieved developments.”
Nishioka added: “Stratified gasoline direct injection can require more energy than a homogeneous system. For this reason, Denso ignition system developments are focusing on developing an even more robust structure that can deliver the required outputs across a long lifetime.”
Turning to trends in the ignition system aftermarket, Claver Joseph, IAM vehicle electronics product manager for Delphi says the ignition system is a key component in today’s engine management system. “As the transition from traditional mechanical technology is replaced by electronic systems, there is a natural growth and demand for these products. This inevitably means that the market place has now become competitive. Some aftermarket suppliers provide lower quality products that can lead to ongoing problems and unreliable repairs. Delphi is recognised for delivering high quality OE products to its OEM’s and Aftermarket customers.”
As far as technology is concerned, most modern commercial vehicles have moved away from traditional mechanical systems. Joseph concluded that a key change includes a shift to a full electronic system, which delivers greater accuracy on ignition timing and improved reliability. “The electronic control unit has evolved and now manages multiple systems, which manage passenger safety and comfort. Delphi has a suite of diagnostic tools capable of identifying faults stored within the ECU.”