The automotive supplier is taking modularity to a new level: to the roof. It has developed a method to combine coil-coated metal with a headliner and a polyurethane in between that not only can provide better physical properties for a roof, but which can improve assembly, as well.
What does John Montagu (born, November 3, 1718; died, April 30, 1792) have to do with the auto industry? Arguably, not a heck of a lot. But when you see his title, it becomes a bit clearer: he was the fourth Earl of Sandwich: yes, the guy for whom the “sandwich” was named.*
The earl came to mind when Meritor Automotive, Inc. (Troy, MI) launched its integrated roof module, which, according to Terry O’Rourke, president of Meritor’s Light Vehicle Systems (LVS) business, is likely to appear in a high-volume application (probably a European auto) in model year 2004.
A key aspect of this roof module-which is a second-generation design for the supplier of roofs, doors, access control systems, wheel products and suspension systems-is that it has what is known as a “sandwich build”: there is a polyurethane composite layered between the outer skin and the interior headliner. This encapsulation is as handy as its edible namesake in that it permits the integration of various components, such as wiring harnesses (with wires proliferating throughout even non-Internet enabled vehicles, the overhead real estate is key) and ordinary sunroof parts, including the guide rails and water management elements.
O’Rourke suggests that the roof module has the potential to revolutionize automotive assembly, not only as a result of the integration of components through the sandwiching, but also from the standpoint of the assembly plant. Nowadays, doors-off production is common in assembly plants. This is done not only to protect the doors from getting marred during vehicle build, but also in order to facilitate access for workers and components into the vehicle.
The roof module, O’Rourke says, would permit roof-off production: “There is a day in the not-too-distant future where the second-to-last station on the assembly line is where the roof module is glued in place. . . and the last station will be where pre-fabricated doors are hung.” Given the fact that Meritor is in the door-making business, there is the potential for the application of this sandwich-based technology for doors, too. Dr. Heinrich Wied, Meritor’s vp of Light Vehicle Engineering says that they are examining the feasibility of having a polyurethane plate onto which things are attached that would be integrated with the door inner. This might be something along the lines of an open-face sandwich.
How well do you really know your competitors?
Access the most comprehensive Company Profiles on the market, powered by GlobalData. Save hours of research. Gain competitive edge.
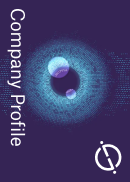
Thank you!
Your download email will arrive shortly
Not ready to buy yet? Download a free sample
We are confident about the unique quality of our Company Profiles. However, we want you to make the most beneficial decision for your business, so we offer a free sample that you can download by submitting the below form
By GlobalDataIssues
According to Erik B. Roeren, acting director, LVS Roof Systems, the company has two years’ experience providing roof modules: the DaimlerChrysler MCC smart car is being fitted with a Meritor roof module. That’s the first-generation roof.
Of course, in the case of smart, it was a clean-sheet approach to manufacturing. But in conventional automotive operations, there are issues that need to be considered. For example, roofs are usually a pick-up point for cars being moved through paint systems. There would need to be reengineering here. There are some political/cultural issues that need to be addressed, as well: the people who are responsible for the outer skin are different from those who are responsible for the headliner. The modular roof creates a new level of responsibility (especially as the accounting that makes it cost-justified requires plenty of aspects to be considered, a more holistic approach than is the norm).
And there is a non-trivial level of responsibility involved with a roof module: as Wied points out, the roof module is “an expensive, big part. We have to be able to assure that it is produced with high quality.” An auto company is going to require plenty of assurance that when a vehicle reaches the second-to-last line that the roof is going to be ready.
Approaches
Ordinarily, roofs are stamped, welded into place, then painted in spray booths along with the rest of the car. But the Meritor roof module’s outer skin is produced with different processes. Instead of being painted after the material has been formed into the finished part, the metal is coil coated in sheet form. Then the sheet of coated material is deep drawn to form the roof. This drawing process is patented. We do know that the material is not rigidly fixed into the tooling but it is able to flow, thereby minimizing the potential for the painted surface to be broken or marred by the tooling during forming.
Coil coating is said to provide a number of benefits, such as a better control of the painted finish and a minimization of paint waste (i.e., no over spray).
Obviously, a completed component like this roof is not something that one would like to have a spot welding gun around. Roeren says that the adhesive used to attach the roof to the body is like that used to affix windshields in place. Additional assembly assurance can be attained through the use of supplementing the adhesive with a few screws.
In terms of the physical performance of the roof module, there are said to be advantages. For example, Roeren says that by using an aluminum outer skin and a fiberglass-reinforced foam material, there can be a 40% weight reduction without giving up anything in terms of stiffness. If the outer skin is steel, then a thinner gauge material can be used (e.g., 0.38 mm versus the common 0.8 mm). Sufficient stiffness can be produced such that cross-car members can be eliminated (even adjusting the type of adhesive used can help improve the stiffness of the roof). NVH (Noise, Vibration, Harshness) can be improved not only by providing sound-absorption materials into the headliner, but also by the potential of integrating speakers into the roof.
From the standpoint of cost, there can be a savings as much as 30%, assuming that all costs are factored into the calculations (e.g., taking into account such things as changes in the stamping plant, as well as in the off-line integration of elements that are ordinarily included during final assembly).
Undoubtedly, there are sandwiches and there are sandwiches. Given that Meritor has five development contracts with auto makers for its sandwich approach to roof module build indicates that there are plenty of people are-dare we say it?-hungry for new technology.
*There are two takes on this. One is that the invention was a result of Montagu’s love of gambling: he didn’t want to leave the table, so he had his servants bring him meat and cheese between two slices of bread-which combined portability with a means by which the cards were kept from getting all greasy. Others counter that due to a war wound that he experienced at age 17, he had to live on liquids; the sandwich was something that he’d observed while visiting farms in France.
This (above) is the outside of the roof (it could be steel, aluminum or plastic) and below is the inside, the headliner. Sandwiched in between, there’s a polyurethane composite material. Meritor Automotive can supply completed roof modules like this-and include things such as wiring harnesses and other overhead components-to an assembly line at the second-to-final station, which would mean that not only could cars go through final assembly with doors off, but with the roof, off, too, which would certainly facilitate such things as installing seats.