Fully integrated supply chain management
systems can pay their way. This was the outcome of a pilot project recently undertaken by
one US supply chain in the automotive industry. The participants proved that an integrated
supply chain gives significant cost and time savings, not just for the OEM and the first
tier supplier, but also for the second, third and fourth tier suppliers.
Rapid response in the supply chain is much
sought after. This is particularly true in the automotive industry where competitive edge
is closely linked to the ability to respond to an ever-changing marketplace. The
procedures and technology to operate a smooth-flowing integrated supply chain already
exist. However, few companies have adopted them because of an inability to justify the
investment. The recent pilot project MAP (Manufacturing Assembly Project) proves
justification does exist. In fact, it concluded that improved communication within a
multi-level supply chain could save the automotive industry an estimated $1 billion every
year.
“Electronic Data Interchange (EDI) is
already widely used in the automotive industry for transmitting purchase orders and
invoices. However, it is rarely used outside of the OEM first tier supplier context,”
says Susan Hill, manager of JBA’s Detroit branch.
The seat-assembly supply chain which MAP
focused on involved car manufacturers Ford, Chrysler and General Motors; seat manufacturer
Johnson Controls; and twelve suppliers from four tiers of the chain. Each participant set
up an integrated supply chain management system. All reported major benefits.
Lead times, for example, showed
considerable improvements. The time to move schedule information from the OEMs to the
bottom of the chain fell from more than a month to 11 to 13 days, says the Automotive
Industry Action Group (AIAG) which initiated the US pilot. A lead time of one day per tier
will soon be reached when further improvements are made, the AIAG claims. Inventory turns
have also been increased by 17-24 per cent and error rates cut by 75 per cent. In
addition, MAP participants report a labor saving per customer of up to eight hours a week
in the order-entry process.
Benefits throughout the Tiers
How well do you really know your competitors?
Access the most comprehensive Company Profiles on the market, powered by GlobalData. Save hours of research. Gain competitive edge.
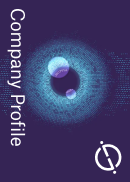
Thank you!
Your download email will arrive shortly
Not ready to buy yet? Download a free sample
We are confident about the unique quality of our Company Profiles. However, we want you to make the most beneficial decision for your business, so we offer a free sample that you can download by submitting the below form
By GlobalDataOne MAP participant R-R Springs, which
employs 34 people making seat springs, reported knock-on benefits. According to Rick
Richter, vice president of engineering, shorter order processing times allowed production
schedules to be generated more rapidly and capacity planning to be done more accurately.
“As a result, we have become more aggressive in developing new business with the
confidence that we can quickly move this business into production and meet the
customers’ delivery requirements,” he says.
“The benefits that US firms have
gained through their participation in MAP are equally available to European car companies
and suppliers”, says Susan Hill. “A European pilot project is not necessary. MAP
serves as a pilot for industry worldwide and not just for the automotive industry.”
Each company in the supply chain does,
however, need to be equipped with an Enterprise Resource Planning (ERP) system capable of
automatically receiving order schedules and daily call-ins from customers, and generating
schedules and call-ins for onward transmission to suppliers. Current ERP systems, Susan
Hill claims, are well able to handle the variety of communications standards and message
formats used by different companies on different continents.
“MAP is indeed a very significant
project”, Susan Hill believes. “People have talked a lot about EDI but few have
fully integrated the supply chain. Now, through MAP, we have proof of the tangible
benefits that result from integration. We can now put dollars against it.”