In this month’s management briefing, Mark Bursa reviews developments in Russia’s automotive market and industry. In this second part, he looks at vehicle production developments and components issues.
New production rules
Foreign OEMs wanting to enter the Russian market must comply with Russian government rules on volumes, local content and import tariffs. These have recently been revised in a new regulation called Decree 166, and foreign OEMs have responded positively, making larger volume commitments.
The main change is an increase in foreign carmakers’ investments in Russian plants. The minimum size of investments for carmakers that already have plants in Russia is to be set at USD500m, or USD750m for those that are only starting production in Russia. Previously, the average size of investments in production in Russia ranged from USD150m-200m.
Under the Decree 166 rules OEMs must commit to:
- Produce at least 300,000 units at a new plant within four years of the agreement being signed, or build more than 350,000 units for an existing plant within three years of the agreement being signed
- Achieve 60% local content within six years (more rapid timetable for existing plants)
- Carry out stampings within four years
- Equip at least 30% of vehicles with locally-sourced engines and/or transmissions within four years
- Establish an R&D centre in Russia
In return, the following concessions are allowed:
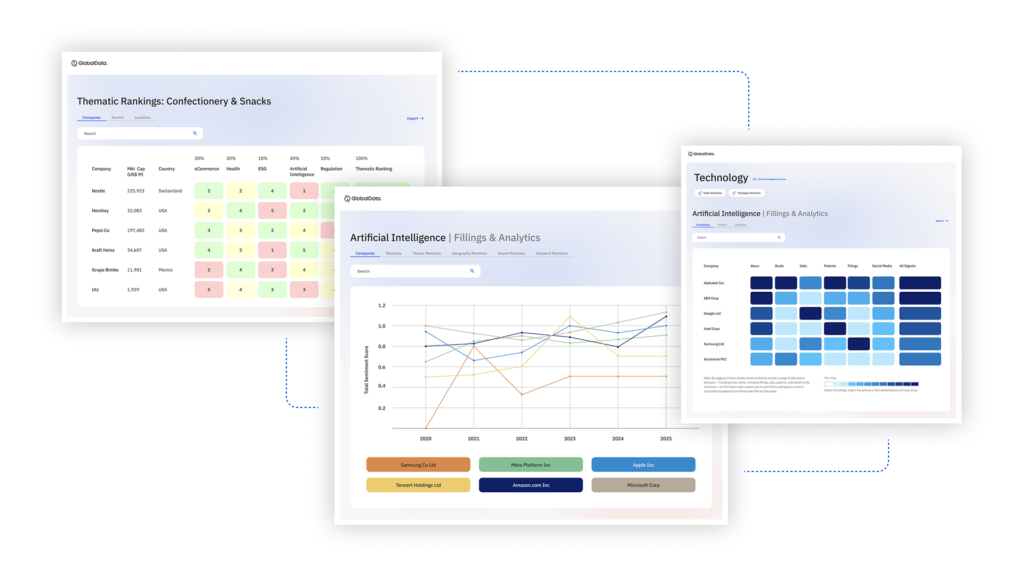
US Tariffs are shifting - will you react or anticipate?
Don’t let policy changes catch you off guard. Stay proactive with real-time data and expert analysis.
By GlobalDataComponents can be imported on preferential terms for eight years (but no later than 2020)
SKD (semi-knock down kit assembly) can be carried out for 36 months following the signing of the new agreement (but kits should not account for more than 5% of total production)
So far, a number of automakers and JVs have agreed to these terms, including:
- Renault-Nissan/AvtoVAZ
- KamAZ/Mercedes-Benz
- Ford/Sollers
- Volkswagen/GAZ
- General Motors
- Fiat
- Magna
The only potential problem with this is the likelihood of medium-term overcapacity. All the commitments to the new rules would amount to 3.15m of capacity, and JD Power estimates that could give Russia a combined production capacity of 3.85m by 2016. If the Russian domestic vehicle market is significantly under that level – and it is forecast to be – then the Russian market will have overcapacity.
Addressing the major problem – components quality
The most significant obstacle to achieving these targets – especially the local content-related objectives – remains the quality of local Russian-made components.
Despite the arrival of foreign OEMs, components quality still lags behind accepted standards, even in Central Europe, and legislative measures designed to increase local content have not gone hand-in-hand with initiatives to improve the domestic auto component industry.
The low quality of Russian auto components is a consequence of the technical and technological backwardness of the industry. In the Communist era, most auto components were produced by automobile plants with a high degree of vertical integration. AvtoVAZ’s Togliatti factory produced every part that went into a Zhiguli, from steel panels to plastic mouldings.
The manufacturers admit that vertical integration has been a problem. AvtoVAZ deputy CEO Sergey Tselikov told Just-auto in 2008: “Being a full-cycle plant was an advantage in the past – but now we see it as a disadvantage that has hampered the development of independent components manufacturers.”
As a result, it was difficult for new market entrants to find independent suppliers capable of making parts of a suitable standard for more modern cars. The only alternative was to encourage foreign Tier 1components suppliers to follow the manufacturers into the Russian market. But even these initiatives were beset with problems due to the poor standard of Tier 2 suppliers and inadequate materials quality, especially plastics.
The good news is that around 40 international suppliers are establishing manufacturing operations in Russia – the extra volumes demanded by the new government automotive production rules have clearly encouraged more components manufacturers to build new facilities to supply the new “transplants” and JVs.
These promised volumes, plus the large potential aftermarket demand, have made Russia attractive to the global Tier 1s. Analysis by Ernst & Young suggests the proportion of OEM components compared to aftermarket components will shift over the next three years. Currently the Russian component aftermarket exceeds the OEM market in value terms with a share of 73% against 27%. But by 2014, the OEM segment is expected to reach a 48% share, which would be more in line with other mature markets.
The growth will be rapid – Ernst & Young estimates the total value of the Russian automotive components sector to be USD33 billion in 2010 (with only $9bn accounted for by OEM components). By 2014, this will have grown to an estimated USD56bn, including USD27bn worth of OEM parts.
Ernst & Young also expects to see more joint developments between Global Tier 1s and established Russian suppliers rather than Greenfield projects, as JVs offer a number of benefits, including risk sharing with a local partner and more rapid access to the market.
Many of the components JVs being established are alliances with the Russian automakers. GAZ Group has signed agreements with Bosal of the Netherlands to make emissions control systems, and with Swedish industrial producer FinnvedenBulten to produce fasteners. Both JVs will be located close to GAZ’s Nizhny Novgorod plant.
The GAZ-Bosal JV will make exhaust pipes, mufflers and catalytic converters from the fourth quarter of 2011 at an annual rate of 350,000 kits. It will supply GAZ and other automakers.
GAZ Group president Bo Andersson said: “Implementation of the project will become a successful step in attracting leading international manufacturers to localise hi-tech auto components in the Nizhny Novgorod region and to develop the automotive cluster in the region.”
Some suppliers are opening wholly-owned plants to service the growing market. Trelleborg Automotive has opened a new manufacturing facility in Zavolzhye, near Nizhny Novgorod, to make anti-vibration products. It is the company’s first production facility in Russia
Jim Law, head of Trelleborg’s anti-vibration division, said: “The increasing demand for new cars in Russia, along with government initiatives for Russian-based car manufacturers to source locally-manufactured components, means that many globally recognised car manufacturers are opening production facilities in the country.”
Other manufacturers are bringing affiliated suppliers with them. A group of Hyundai suppliers has opened a RUB5.872bn industrial park to produce car components in St. Petersburg, close to Hyundai’s new plant. The park includes seven Korean component supplier facilities: Sungwoo Hitech, SeJong, NVH, DooWon, DongHee, and ShinYoung. Four more suppliers are expected to be added later.
See also – Part 1 – Market review
Still to come – Part 3 – Manufacturer alliances