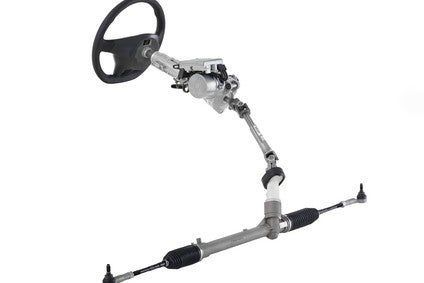
For many years, power steering technology was focused on hydraulic systems but demand is now favouring electric power steering mainly due to fuel consumption and logistical benefits. In this briefing extracted from just-auto/QUBE’s research service, Matthew Beecham provides an overview of some key companies and developments in the steering sector.
There are generally three types of electric power steering (EPS), depending on the positioning of the motor/reducer unit: column type, pinion type and rack type. The best type for any given vehicle model depends on that model’s particular characteristics.
EPS systems effectively eliminate the traditional hydraulic system’s power steering pump, hoses, hydraulic fluid, drive belt and pulley on the engine.
More specifically, EPS offers significant fuel efficiency advantages and reduced CO2 and greenhouse gas emissions as steering assist is only supplied upon driver demand through an electric drive system that is independent of the engine. Because electric steering systems operate under computer control, steering feel can be tuned through software, enabling integration with other electronically controlled technologies such as electronic stability control braking systems. Electric steering systems are also suitable for supporting electric vehicle architectures. An EPS system can effectively change the assist force for steering operation depending on information such as steering angle, steering angle velocity, speed and acceleration of the vehicle and each wheel, and yaw rate. The EPS system can therefore not only reduce the steering load but also optimise the assist force depending on the driving situation.
SELECTED COMPANY DEVELOPMENTS
Nexteer
How well do you really know your competitors?
Access the most comprehensive Company Profiles on the market, powered by GlobalData. Save hours of research. Gain competitive edge.
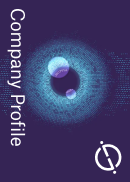
Thank you!
Your download email will arrive shortly
Not ready to buy yet? Download a free sample
We are confident about the unique quality of our Company Profiles. However, we want you to make the most beneficial decision for your business, so we offer a free sample that you can download by submitting the below form
By GlobalDataDuring an interview with just-auto, Nexteer’s president and COO Laurent Bresson was asked for his thoughts on what is next in the steering technologies roadmap after EPS? He said: “There will continued development of different types of EPS. However, I would mention two main themes – one is mass savings, switching to lighter materials and using different joining and welding technologies. The other is around the safety of the products – cybersecurity is a major focus from the OEMs, self-driving cars, park assist, and lane keeping technologies. There are many opportunities with steering a major enabler of many ADAS solutions. Also, as a company we benefit in that we are very vertically integrated in terms of the design and the development of these new technologies – for example, we write all our own software, we design all the hardware; we have build-to-print design on the motors etc.”
TRW Automotive
TRW Automotive has developed a suite of environmental sensors including long- and medium-range radar, short-range radar, video sensors, steering and roll angle sensors and yaw rate and velocity sensors. Together these sensors create a more complete picture of the driving environment and help enable the most appropriate engagement of the integrated safety subsystems.
Peter Lake, TRW’s executive vice president, said: “The intelligence in our systems has evolved. In the past, systems were purely reactive to driver inputs; they moved to become responsive and to interpret a driver’s intent – but still depended on input (for instance brake assist increases the brake force when the system ‘learns’ that the pedal force isn’t sufficient for the situation). And now, with the appropriate level of information about the driving environment – through the use of multiple sensor sources – the systems can ultimately take autonomous action to lessen the severity of an unavoidable incident – regardless of whether a driver hits the brake pedal or moves the steering wheel.”
According to Lake, electro-hydraulic power steering, which the company thought would be “transitional technology”, is going to be around for the foreseeable future. In discussing the ‘autonomous vehicle’ in an interview with just-auto, Lake said that he sees automatic emergency braking and park assist becoming more common while the increasing use of electric park brakes, evolving to electro-hydraulic park brakes, adds additional functionality such as hill holder and automatic park brake application. He feels any move away from steering wheel and pedal control (à la the Airbus airliner maker’s switch to the ‘side stick’ 20 years ago after years of control columns) is “counter intuitive but, who knows, it might come”. Some form of steering wheel-mounted brake control would be more likely, Lake thinks, but even that is not intuitive, he adds.
“I think you are going to see by-wire,” he said. “Whether it’s a hybrid system that optimises what you can do with 12V or maybe it’ll be 24V. None of us went to 42V because it was too expensive, and didn’t make sense, but 24V might. If we do see very high volumes of electric vehicles, it really depends on what architecture they put on them. Is it going to be 300V or are they going to make 12V or 24V available? We could come up with a hybrid system of electric [brakes] on the rear and hydraulic on the front, or all-electric, but it’s an issue of having that power available. I can see a pull for electro-mechanical braking and so forth but again it will come down to cost.” He said any new technology had to add significant new functionality rather than being ‘me-too’ – the same as what’s on the car – otherwise, there’s not a lot of reason to adopt it. Lake noted that a lot of TRW’s US production had been moved to Mexico while European output had progressively moved east but it was “evolutionary rather than revolutionary and, paradoxically, some of these low-cost regions aren’t as low-cost as they used to be”.
In October 2012, Nissan Motor unveiled the world’s first steering technology that allows independent control of a vehicle’s tyre angle and steering inputs. A conventional steering system directs tyre movements by transmitting steering inputs to the tyres via a mechanical link. Nissan’s next-generation steering technology reads the driver’s intentions from steering inputs and controls the vehicle’s tyre movements via electronic signals. This transmits the driver’s intentions to the wheels even faster than a mechanical system and increases the direct driving performance feel by quickly and intelligently communicating road surface feedback to the driver. The system controls and insulates the vehicle from unnecessary road-generated disturbances to deliver only the necessary performance feel to the driver. For example, even on a road surface with minor ridges or furrows, the driver no longer has to grip the steering wheel tightly and make detailed adjustments, so travelling on the intended path becomes easier.
Nissan Motor also announced the development of the “autonomous emergency steering system. This system offers a high level of collision avoidance capability by applying automatic braking and automatic steering in situations where a collision is imminent and evading obstacles by braking may not be effective. The system takes effect in situations where unpredictable risks arise, such as sudden intrusions onto the road in low speed zones, or when a collision at high speed is imminent due to the driver’s delayed recognition of the tail end of a traffic jam.
The autonomous emergency steering system, using the information provided by the front-mounted radar and camera, the two left and right rear radars, and the five laser scanners attached around the vehicle, initially acts on a risk of collision that cannot be avoided by braking. Simultaneously, it checks if there is a forward zone free of obstacles and that there are no vehicles approaching from the rear, and then displays to the driver the direction that the vehicle should be steered. If the driver cannot immediately steer in that direction, the system takes over to automatically steer the vehicle to help avoid a collision.
NSK has developed a low-friction reduction gear for an EPS system that, it claims, helps makes for smooth steering corrections during straight driving as well as improved comfort when the steering wheel returns from large steering efforts such as turns in intersections. NSK used its tribology technology to optimise the formation of oil film for improved lubrication and developed a new grease that incorporates additive technology that prevents the increase in viscous drag. As a result, oil film is formed between the face of the gear teeth in the reduction gear for a 17 percent reduction of friction in the reduction gear. The supplier is planning to introduce this product in 2017.
More: Global light vehicle steering market- forecasts to 2030