Jaguar’s new AJD-V6 diesel has set new standards in refinement and performance. Jesse Crosse looks at the new engine in detail and uncovers the secrets of its success.
Few engines have attracted quite as much speculation during their development period as the new 2.7-litre V6 diesel from the PSA/Ford alliance. Since it’s announcement in Paris in 1998, there’s been almost unending speculation as to the V6’s specification, especially in relation to its use as one of Jaguar’s debut diesel powerplants. At the time, both sides of the alliance remained tight-lipped about the premium diesel’s precise specification, admitting only to its basic configuration, capacity and that its development would be led by Ford and that it would be manufactured at Dagenham. Now Jaguar’s version, the AJD-V6 engine, has finally appeared beneath the bonnet of the 2004 model year S-Type Jaguar, quickly seducing road testers with its refinement and power.
A prediction in May 2001 by this author was for an all aluminium engine with four valves per cylinder, in the region of 180bhp, 285lb ft torque with a transient capability of 320lb ft, twin-turbochargers and piezo-crystal injectors. As it turned out, the ‘Lion’ engine surpassed even that, giving up a maximum of 206bhp and 320lb ft without using overboost. The engine block is made from CGI (compacted graphite iron) provides a good proportion of the weight advantage achievable with aluminium but without compromising noise suppression. So light is the new engine at 202kg, it outweighs the petrol V6 by only 15kg, while even outstripping the 4.2-litre V8’s maximum torque. According to chief engineer, Paul Walker, CGI also offers 75 percent higher tensile strength than conventional cast iron, 30-40 percent more elasticity, and has twice the fatigue strength. Tellingly, Jaguar says these characteristics allow potential for increased engine performance over several vehicle generations, something which implies not only that a long life is planned for this motor, but that it could indeed power future sports car projects hinted at by the Jaguar RD6 concept.
High fives
The induction side of the engine is particularly impressive. At the beginning of the project, Ford had been investigating electrical assist turbocharging for diesel engines generally, but since the start of what has been a four-year project, the new Jaguar has the latest technology, turbochargers which overcome the usual problems of low speed response. The inertia of the compressor turbines has been considerably reduced compared to earlier designs and the variable nozzles are electronically, rather than mechanically, actuated. On the injection front, Siemens VDO’s piezo-injection common rail system does the honours, providing 1,650 bar pressure and enough performance to deliver up to five injections per cylinder, each cycle. The injector bodies contain specially developed piezo-ceramic crystals, each one around 0.1mm thick, arranged in a 45mm high column and capable of lifting an injector needle by 0.8mm. The solid state actuators deliver a minimum switching time of 0.2 milliseconds.
Fuel is delivered through nozzles in each injector tip of just 145 microns in diameter. Thanks partly to the immense speed of the injectors (whose reaction time surpasses electromagnetic predecessors by a factor of four) two pilot bursts are possible followed by a split main injection and a small post injection. Unusually perhaps, these figures have not been reached through a kind of random process of evolution over a number of years, but were identified and targeted way back in the late 1990s by most common rail developers. Six years ago, advanced diesel engineers were looking forward to the day when an operating pressure of 1,300 bar might escalate to the magical 1,600 bar seen as a prerequisite for super fine atomisation of fuel and efficient control. Piezo injectors were also seen as something of a Holy Grail in diesel development, capable of delivering the speed, timing and accuracy of fuel metering necessary to reduce knock, bring emissions tumbling and enable more efficient regeneration of particulate filters if needed.
How well do you really know your competitors?
Access the most comprehensive Company Profiles on the market, powered by GlobalData. Save hours of research. Gain competitive edge.
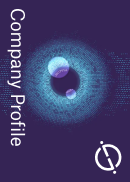
Thank you!
Your download email will arrive shortly
Not ready to buy yet? Download a free sample
We are confident about the unique quality of our Company Profiles. However, we want you to make the most beneficial decision for your business, so we offer a free sample that you can download by submitting the below form
By GlobalDataFilter free
With Euro 4 now upon us and the spectre of Euro V and beyond looming, realising the current level of technology was essential as continued improvements in the combustion process and control systems provide better tools for engineers to tackle the growing demand for lower emissions. Despite the lead taken by PSA with its particulate filter and the subsequent announcements by Mercedes, BMW and GM/Fiat of their own, additive free filter systems, most diesel engineers stress the importance of dealing with the particulate problem during the combustion process as far as possible, rather than mopping it up afterwards.
For the time being, Jaguar’s powertrain remains unfiltered, manual installations conforming to Euro 4. Automatics meet Euro 3 although Jaguar says the engine is Euro 4 capable when necessary – and that’s a shame, considering both current UK taxation benefits for Euro 4 vehicles and just how advanced this diesel is supposed to be. Discerning buyers are bound to ponder that one when weighing up the pros and cons. Nevertheless, some of the detail in the engine emphasise how no stone is left unturned when it comes to improving efficiency and the fuel feed is an example. Diesel oil is delivered to the high pressure, three-piston radial pump by two low pressure pumps, all three under the control of an ECU. Fuel to the high pressure pump is precisely metered according to demand, providing the minimum pumped volume at any given time. The result is lower inertia in the fuel system and therefore minimum power consumption by the high pressure common rail pump. Fuel is cooled during its passage through the ‘V’ of the engine block and also in the return line.
The ECU is all seeing and all powerful. Taking advice from 23 sensors (including two knock sensors) and giving orders to 20 actuators, it handles the opening and closing of flaps in the sophisticated inlet port system to optimise flow and swirl through the engine’s entire operating range. The ECU also acts as the EGR controller – responsible for reducing combustion temperatures and therefore NOx – as well as being responsible for the VNT turbochargers and the electronic throttle’s management of shut-off shake. The S-Type Diesel’s character is coloured by more than it’s sublime power unit, though. It’s integration with the ZF HP26 automatic transmission, dual isolated engine mounts, plus the spectacularly successful tuning of the suspension has made this one of the most well-rounded and cohesive S-Type packages yet and it’s hard to imagine it not becoming a best seller in the range.
Subtle blend
Jaguar lists some of the suspension hardware changes that have been made, such as low friction ball joints allowing freer suspension movement, retuning of spring and damper rates as well as the revision of steering characteristics. That, of course, is a simplistic account of the magic wrought with this S-Type derivative by vehicle dynamics guru, Mike Cross and his team, combining collected body control, taught and responsive chassis and steering with an almost unbelievably supple ride. Considerable work has also been done on the calibration of engine and transmission to effect seamless yet swift shifting. Overall, the blend of characteristics is so subtle and yet executed with such clarity, it’s hard to image anything better. Indeed, this time Jaguar may have tossed down a gauntlet so big, competitors might struggle to pick it up.
Although we’ve talked about numbers endlessly crunched in search of a super-refined, civilised diesel, we haven’t yet touched on the experience of sitting behind this engine. It’s quiet, super refined and almost completely lacking the ‘cackle’ (rattle, or knock) which normally emanates from even the best diesels. Only when approaching 5,000rpm at maximum load can you detect a familiar, though muted, diesel soundtrack. Apart from the super-sophisticated fuel and air system on this new engine, a double-skinned sump, elastomeric-isolated, composite cam cover and dual isolated engine mounts all contribute to this diesel’s composure. Credit must also go to Jaguar’s vehicle refinement team who in recent years have been blessed by a new anechoic chamber complete with a rolling road capable of testing both two and four-wheel drive cars at speeds of over 170mph. Audio labs allow detailed analysis of the types of sound generated in, around and by the car to the extent where sounds can be digitally disected into component parts, the source of unwanted frequencies targeted, then taken out. Jaguar engineers have had a few years practice with the new facilities now. Early results were good but the work on this car is nothing short of an engineering triumph.
Back to that sublime powerplant, then. Most of the work, says Jaguar, was carried out between engineers at Ford’s research centre in Aachen, together with engineering teams at Jaguar’s, Whitley Engineering Centre. The engine will be built at Ford’s new Dagenham Diesel Centre, initially at the rate of 100,000 to 150,000 units a year. Investment costs of €350 million included provision of an on-site engine block machining facility and allows room for expansion as more Jaguar, Land Rover and PSA models come on line. No doubt, we’ll get PSA’s side of the story when the engine appears in the 406. Naturally, there will be considerable differences and although most of the basic hardware will remain the same, a Peugeot source says it’s likely that the common rail system will also come from Siemens VDO and of course, calibration and configuration will be handled by PSA engineering teams. For Jaguar though, the work is done, though there’s no time for resting upon laurels. The engine is destined for the XJ6, it’s aluminium architecture presenting vehicle refinement teams at Jaguar with a whole new set of challenges which, on their present form, they’ll rise to with flying colours.