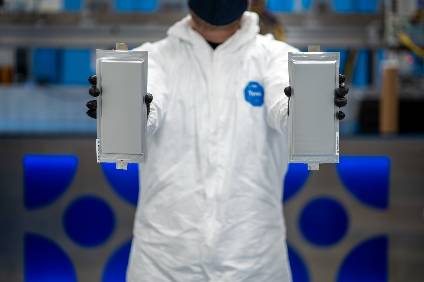
Far Away Are Mass Market Solid-State EV Batteries
Battery technology is emerging as a key differentiator among electric vehicle projects. With most of the EV powertrain beyond the battery pack achieving efficiency figures in excess of 95%, improvements in battery tech offer the greatest potential for range and performance gains.
Incremental improvements have been made by adjusting the chemical makeup of a cell’s electrodes or electrolytes, or by optimizing the sizing, layout and structure of cells within a battery pack. However, none of these modest improvements compares to the giant performance leap promised by solid-state batteries.
How well do you really know your competitors?
Access the most comprehensive Company Profiles on the market, powered by GlobalData. Save hours of research. Gain competitive edge.
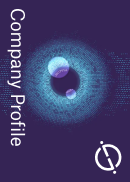
Thank you!
Your download email will arrive shortly
Not ready to buy yet? Download a free sample
We are confident about the unique quality of our Company Profiles. However, we want you to make the most beneficial decision for your business, so we offer a free sample that you can download by submitting the below form
By GlobalDataSolid-state cells generally use the same lithium-ion-based chemical reaction to store and discharge energy as conventional cells. The difference lies in the electrolyte used to separate the anode and cathode and facilitate the movement of lithium ions. Conventional cells use a liquid-based electrolyte – commonly a lithium salt suspended in an organic solvent – while solid-state cells swap that out for a wafer-thin solid electrolyte, usually made from either ceramic, polymer or glass.
Removing the liquid electrolyte brings many potential benefits. Solid-state cells are lighter and more compact than their liquid-based counterparts, meaning pack weight can be reduced, or energy capacity increased. They should be more resistant to lithium dendrite formation, which will improve power discharge performance and raise potential charging speeds, along with extending the service life of the battery pack. In addition, once mass-manufacturing is achieved, they should be easier and quicker to make than conventional Li-ion cells thanks to the removal of solvents and having fewer production steps.
There are even more pronounced benefits offered by solid-state cells in the field of battery safety. Fires caused by defective or damaged lithium-ion cells have been widely publicized, including the current problems faced by the Chevrolet Bolt and its LG-sourced batteries. In many cases, these fires occur because internal failure or external damage has caused the volatile lithium electrolyte to become exposed to the outside air, causing it to ignite and setting off a chain reaction that can destroy the whole battery pack. Solid electrolytes sidestep these problems entirely and are highly resistant to fire and explosion – even in the event they are punctured or impacted.
While they offer many theoretical benefits, no company has yet demonstrated the ability to mass manufacture solid-state cells for light vehicles, with most still at the bench-test stage. There are still a number of issues left to solve including designing the solid electrolyte and electrodes in such a way that they interface evenly across their entire surface, because any warping can create gaps that limit cell efficiency. In addition, material stability has been shown to be a problem with the electrolyte’s brittleness leading to microscopic fractures that limit cell performance.
Blue Solutions, a subsidiary of France’s Bolloré, has won a contract to supply its solid-state cells for Daimler’s eCitaro G articulated urban bus – the first recorded commercial supply agreement for the technology. However, the optional solidstate pack needs to be deliberately heated to a relatively high operating temperature of between 50C and 80C – sapping some range in the process and making it inappropriate for use in light vehicles with their unpredictable usage patterns.
What GlobalData users think
We surveyed 467 automotive industry respondents globally across GlobalData’s automotive products to understand their expectations for the solid-state battery timeline. We specifically asked when they thought these cells would enter massmarket vehicles, because it is likely that some of the first solid-state fitments will be in rarified, low-volume, highperformance EVs that have little bearing on the majority of light vehicles sold.
A solid 42% of total respondents indicated that they expected solid-state cells to take more than five years to appear in mass-market EVs.
A solid 42% of total respondents indicated that they expected solid-state cells to take more than five years to appear in mass-market EVs. Only 25% felt solid-state cells were less than three years from mass-market EVs, with the remainder falling between these two timescales.
Breaking down the respondents by region, we can see those with the most optimistic timescales tended to come from the Americas, with a majority there expecting commercialization between three and five years. Respondents from Europe and Middle East and African regions sounded the most cautious tones, with 47% and 60% respectively expecting solid-state batteries to take more than five years to appear in mass-market vehicles.
The timelines for solid-state deployment predicted by GlobalData respondents mostly match the timelines proposed by EV makers. Nissan announced at the end of November that it would invest $17.6 billion over the next five years building out its EV manufacturing capabilities, with part of that investment going towards launching a solid-state-powered model by 2028, using its own proprietary cell technology.
Meanwhile, Stellantis and Daimler are targeting 2026 for deployment of solid-state cells, with both companies recently investing in US solid-state startup Factorial Energy. BMW expects to demonstrate solid-state technology in 2025, while VW-backed QuantumScape is targeting 2024 for deployment. GM, Ford and Hyundai are all investigating the technology, and Toyota has thousands of patents in the field with its partner Panasonic, with a 2025 target for deployment.