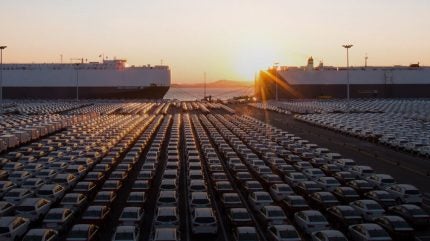
Since the US government announced it was hiking import tariffs on new vehicles and components to 25% earlier this year, global automakers – including US manufacturers GM and Ford – have scrambled to adapt their existing business plans and implement new strategies to safeguard their positions in the world’s second-largest auto market. Many automakers, already struggling with falling market shares and volumes in China, the world’s largest vehicle market, have since substantially revised down their earnings forecasts for the current year and subsequent years.
The automotive industry, including its highly complex component supply chain, inevitably works on long-term planning and relies on a stable government policy environment. New investments are linked to new model production cycles, the introduction of new technologies, and market demand. The sudden introduction of the new import tariffs has taken the industry by surprise, forcing automakers to revise and bring forward their existing investment plans and make short-term fixes to limit the effects of the new tariffs.
President Donald Trump’s seemingly off-the-cuff, ever-changing style of policy-making has created significant uncertainty among global vehicle manufacturers, including GM and Ford, making it more difficult to make long-term investment plans. Trump’s decision to end the EV incentive policies of the previous government has also had a significant impact on the industry, prompting manufacturers to scrap, delay, or withdraw from battery production projects in the US worth many billions of US dollars.
Many in the industry are also wondering whether the next US government, which will be elected in four years’ time, will continue with the hardline trade policies of the current Trump administration.
It is widely accepted that the US had become too heavily dependent on imports to meet its domestic vehicle demand, with Mexico, Japan, South Korea, and the EU being the largest net exporters to the US. Mexico produced almost four million vehicles last year and exported approximately 2.8 million units – with the US accounting for around 80% of these. South Korea and Japan were next, with 1.6 million and 1.5 million vehicles shipped to the US last year, respectively, worth a combined US$ 80 billion, with very few vehicles shipped in the opposite direction.
Canada exported some US$ 28 billion worth of vehicles in 2024, with more than 90% going to the US, although the country also relies heavily on imported vehicles from the US to meet domestic demand. Germany was the fifth-largest vehicle exporter to the US, with shipments worth US$ 26 billion, followed by the UK with almost US$ 10 billion. Demand for US-made “gas-guzzlers” has traditionally been very limited in markets such as Europe, where fuel prices are typically much higher and cars, on average, much smaller.
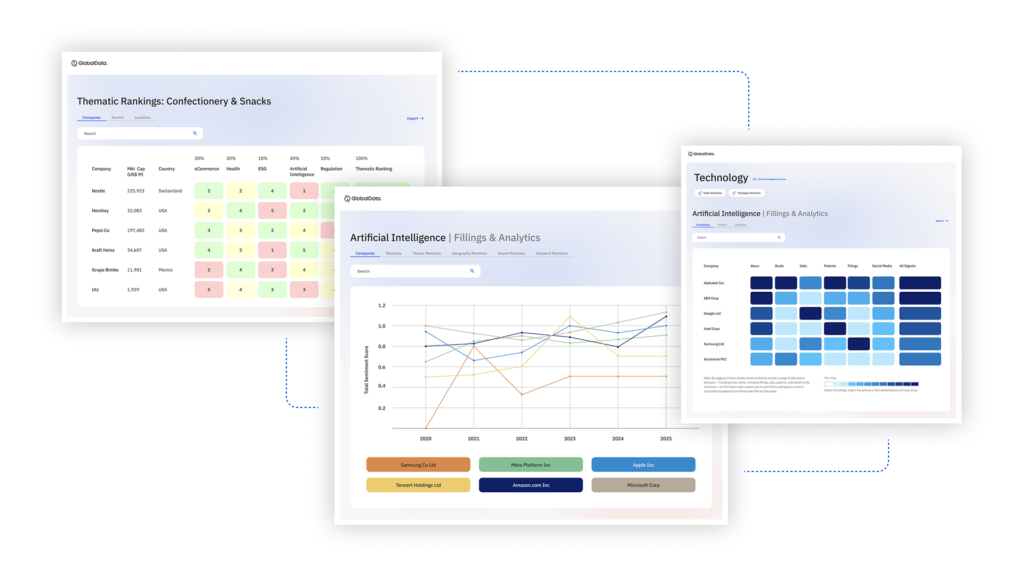
US Tariffs are shifting - will you react or anticipate?
Don’t let policy changes catch you off guard. Stay proactive with real-time data and expert analysis.
By GlobalDataMost global vehicle manufacturers have substantial production operations in the US, but clearly not enough to fulfill local demand, making them heavily dependent on plants located elsewhere. In some cases, manufacturers have been operating their US plants at well below capacity, choosing instead to prioritise production in lower-cost countries such as Mexico to maximize operating margins. This trend is now being reversed.
Most vehicle manufacturers have accepted that they will have to raise prices in the US to maintain positive operating margins, with the burden likely to be shared across the range rather than just on imported models. Prices will inevitably rise across most industries in the US as a result of higher import tariffs, which are expected to increase consumer price inflation, leading to higher long-term interest rates.
US investment plans
In recent months, most global volume vehicle manufacturers have reconfirmed their existing US investment plans and also announced additional investments, as they looked to support their respective governments’ forthcoming tariff discussions with the US administration.
Earlier this year, Nissan announced that it would transfer some production from Mexico north of the border, to increase output and capacity utilization at its US facilities. More recently, US automaker GM announced plans to invest US$ 4 billion in the US to reduce its dependence on imports from Mexico, and similar moves are being planned by Ford, albeit on a smaller scale so far. Shifting supply chains will be more complicated, and will inevitably take more time.
GM has indicated that it will consider discontinuing its manufacturing operations in South Korea, which rely heavily on exports to the US, in the long term if the new US tariffs become permanent.
Honda and Toyota recently confirmed they plan to move production of some models from Japan and Canada to the US. They also confirmed they will have to raise prices in the US to help soften the impact of the tariff hikes.
Hyundai Motor Group began operating its third US plant in Georgia in October 2024. The facility, which has a production capacity of 300,000 units per year, was originally designated to produce BEVs but will now also produce plug-in hybrids. Output is being ramped up this year as more models are added. The South Korean automaker confirmed earlier this year that it will expand the plant’s capacity to 500,000 units per year later in the decade. The group has also cut US exports to other markets in the region, as it prioritizes production for the local market.
BMW confirmed it is currently investing US$ 1.7 billion in its US operations, including US$ 1 billion at its Spartanburg plant to accommodate production of BEVs and US$ 700 million to assemble battery packs at a separate facility nearby. The company plans to assemble “at least” six BEV models in the US by 2030, in addition to ICE and plug-in hybrid models. Earlier this year BMW said it is considering adding a shift at the Spartanburg plant to lift output.
Mercedes-Benz announced that it plans to introduce a new model at its Tuscaloosa, Alabama, plant in 2027, and confirmed it plans to add a new “core vehicle segment” to its US production line-up as part of its “deepening commitment to the US.”
Volkswagen is currently investing US$ 2 billion in a new manufacturing plant in South Carolina to produce battery-powered and hybrid SUVs and pickup trucks from 2027. The German automaker recently formed a strategic partnership with US BEV manufacturer Rivian, in which it plans to invest US$ 5.8 billion to develop and produce a new range of battery-powered software-defined vehicles (SDVs), the first of which is scheduled to go into production in the US in 2028.