Front end module use could reach 50% penetration in Europe by 2006/7, but the market is complex with definitions varying from OEM to OEM. Colin Whitbread unravels the latest technical developments, the potential benefits, and the key players
The use of front end modules (FEMs) is gaining momentum in Europe, based on a list of theoretical benefits to OEMs that seems compelling. These same OEMs retain some caution with regards to widespread adoption however. This reflects scepticism with regard to actual deliverable benefits, especially in the areas of quality and cost, but does not appear to be slowing expansion. Estimates of market size vary as definitions of FEMs vary, but leading players believe that around 20% of cars produced in Europe in 2002, equal to around 3m units, were equipped with an FEM. Europe is the leading market for FEM applications – it is expected to grow to 30% in 2003 (4.5m-4.6m units) and 40% in 2004 (6m units). Further out, some suppliers believe 50% penetration is possible by 2006/07, a level that would take unit demand to 7.5m-8m.
Alongside differences in the definition and adoption of FEMs from one customer or supplier to another, differences persist over the depth of responsibility handed down to the tier 1 FEM integrator. This is particularly with respect to selection and management of the lower tiers of the supply chain. The key integrators mostly offer a full service from the initial module design concept through supply chain management and assembly/delivery logistics, but at present supplier capabilities appear to exceed OEM demands. Many suppliers acknowledge that the challenge of fully convincing OEMs to adopt modularity in the front end of new vehicles has yet to be overcome. Marc Szulewicz, President of Plastic Omnium Auto Exterior, says that “eventually they will all turn to modules. They do not need to outsource, first they need to accept modules”.
The key benefits of FEMs to customers are in:
- Material cost reduction
- Reduction in vehicle assembly time
- Assembly line length reduction
- Reduction in investment tooling
- Reduction in facility investment
Specifics depend on customer preference and strategy – for example whether the front bumper is included or excluded – but FEMs should offer a cut in the number of individual components and their complexity – thereby lowering weight, reducing space requirements, reducing labour costs for OEMs, lowering logistics and quality assurance costs.
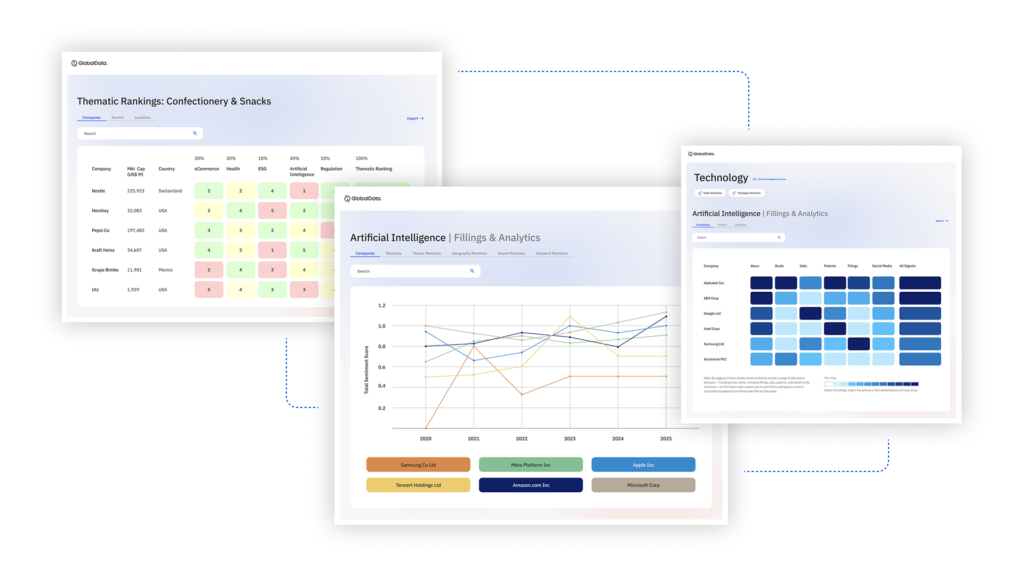
US Tariffs are shifting - will you react or anticipate?
Don’t let policy changes catch you off guard. Stay proactive with real-time data and expert analysis.
By GlobalDataLeading edge FEMs should also enhance the optimisation of major functions such as safety, style and cooling. Some suppliers, such as Denso, believe FEMs without such optimisation can only ever be of limited value. For Denso’s latest FEM, for the Japan-built Daihatsu Copen, the supplier says that by optimizing the entire front-end thermal component zone, it made improvements in heat exchange efficiencies not possible through improvements on individual components. Interviewed at the Frankfurt 2003 IAA, Denso’s new President and CEO Koichi Fukaya, stressed that “additional functions for a front end module are a key point”. “Just assembling the bumper, radiator, condenser etc is not acceptable to customers” he said. “Additional functionality is the key.” Laurent Burelle, Plastic Omnium’s CEO has similar views: “The backbone of our modular strategy is innovation. If the idea is just to put together all the parts, there is no added value for the customer.”
The most complete FEMs comprise the front end carrier, bumper beam and bumper, cooling fan unit, water and engine oil cooling radiators, the air conditioning condenser, radiator grille and headlights. Some suppliers stretch this list to include impact absorbers, the wiring harness and various sensors, usually related to safety systems.
All suppliers have to outsource a slice of module requirements to other tier 1 specialists. Faurecia for example combines its own core expertise in the areas of front end carriers, structural parts, bumper fascias and cooling fan systems with those of specialists in the areas of lighting, air conditioning/cooling and electrical. This still holds true even when two suppliers join forces to pool expertise in a long-term joint venture, as with Hella and Behr with Hella-Behr Fahrzeugsysteme. Suppliers may also join forces for a specific project – Plastic Omnium and Valeo created an alliance just to develop the front end module for the Renault Megane 2.
Despite this multi-sourcing, the FEM integrator must take responsibility for delivering optimum solutions to OEMs in multiple areas, including vehicle structure, component integration, quality, serviceability, fit and finish. This advanced modularity becomes well-suited to multi-site, multi-vehicle platforms, multiplying the benefits to OEMs.
Current Developments
FEMs are evolving, even though the actual concept has yet to be accepted by all OEMs in all global areas.
Many of these developments focus in the area of the front end carrier, the underlying structure of the FEM onto which various components and subassemblies are integrated. These are constructed of thermoplastic materials or, increasingly composites or metal/plastic hybrids and are lighter than metal, rigid and highly impact resistant, and save cost. Faurecia is at the leading edge of these developments – the hybrid metal-plastic carrier developed for the Audi A6 combines metal stamping and plastic injection technologies. Faurecia has patented a continuous compression process designed for semi-structural parts such as the front end carrier and in the field of injection, has patented a process that combines polypropylene and long glass fibres.
Tier 2 suppliers are also playing a crucial role in this area. Dow Automotive has developed a low energy substrate adhesive (LESA) that allows low surface energy materials such as polypropylene (PP) to be joined to other plastics and metals without flame or plasma pre-treatment and without the use of primers.
![]() |
Denso’s carrier for the Daihatsu Copen FEM is also constructed using a new injection moulding process (developed by the supplier) and a light, cost efficient PP material reinforced with long-fibre glass. This boosts strength and rigidity and the new moulding process allowed the carrier to be shaped for optimisation of improved thermal efficiencies in the heat-exchange components. Denso says changing the carrier material and improving the thermal efficiencies led to a 30% reduction in weight compared to conventional components including steel carrier while maintaining sufficient rigidity.
At the 2003 Frankfurt IAA, Plastic Omnium developed the FEM concept a step further, showing a new architecture for an FEM. With this new architecture, the FEM is split into two sub-modules: a technical submodule, which carries the main functional parts, such as cooling, beam and latches; and a design submodule, which carries the body and aesthetic parts (bumper cover, headlamps etc).
|
The technical module is similar to the front end carrier and is dedicated to mechanical behaviour. However, it does not provide so-called “gap and flush” functions as it only integrates hidden standard parts such as the cooling module, impact beam, water reservoirs etc. There could be many advantages to this tech-nical front end: it is a simplified part with a high level of stiffness and at the same time is a more compact module in height and depth, which allows for optimisation of pedestrian safety features. Perhaps one of the most important advantages is that the technical module can be used across platforms and on many different vehicles.
The design sub-module, which is made of a semi-structural frame and the bumper cover, can be manufactured to individual OEM requirements and easily attached later in the vehicle assembly process. This sub-module is critical to final fit and finish and the assembly process becomes of much less significance to gap and flush performance, especially in the headlight/ wing/ bumper interface areas. In addition to function support and integration for such things as sensors, antennas and lights, the sub-module has a pedestrian impact management role.
Plastic Omnium describes this development programme as an on-going pre-study, indicating that commercial applications are some way away. But it highlights the R&D effort that is underway in the sector. Faurecia has also developed what it calls its Measy system to provide a front end platform. This helps compensate for wing-to-wing dispersion when the front end is mounted to a vehicle, thereby optimising gap and flushness performance. Production will begin in 2004.
Summary
![]() |
Supplier competence is growing in the FEM sector and the major players are investing heavily in new concepts designed to accelerate growth. A key focus must be to push ahead with genuine integration of components and functions in order to move away from basic assembly of disparate components, which adds little real value to customers. The advances made by Denso with the Copen FEM illustrate the way forward. Full service capabilities ranging from design/development through supply chain management and delivery logistics are also essential.
Even with these in place, however, there are no guarantees that volumes in the mass market area, the key to growth, will accelerate as quickly as some suppliers predict. OEMs have a variety of strategies with regard to FEMs that present complex challenges to suppliers. Some remain sceptical of the real benefits of the concept while even the more enthusiastic have widely differing approaches to how much responsibility is handed over to suppliers, especially in the areas of lower-tier sourcing and final FEM assembly. Even Renault, which has firmly embraced the use of the Valeo Plastic Omnium FEM for the Megane/Scenic platform retains some scepticism. Odiles Desforges, purchasing head of the RNPO says there are still unanswered questions about the benefits of modules. “Quality is OK she says, but “there is still a question mark over whether the modules are a breakthrough in cost reduction”
“We are expecting more innovation proposals from our supplier base,” she says. For FEM suppliers the hard-sell remains. cwhitbread@supplierbusiness.com
Key players Faurecia Plastic Omnium Hella-Behr Fahrzeugsysteme (HBF) Valeo Denso Visteon Other suppliers |