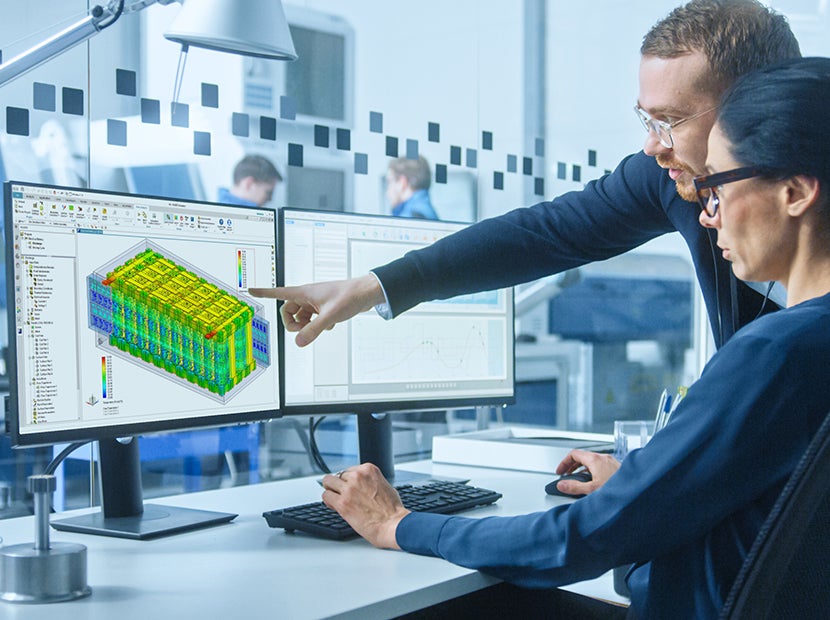
Electric vehicles (EVs) have a set of vehicle performance requirements, including typical vehicle related performance goals such as top speed and acceleration. EVs also have specific requirements such as range and battery charge time. These requirements are the key criteria that ultimately determine battery pack size. These parameters are fundamental in shaping the initial estimate for volume and weight of the battery pack. They are used by the battery team to determine pack performance, packaging and cost trade-offs. The team considers technical information on everything from battery chemistry to total number of cells. Cooling system configuration must also be considered such as type (water or air) or placement of coolant flow. All of these factors can impact overall battery pack volume, height and width, and can cause issues in packaging the battery pack in the vehicle.
Cost, of course, is a crucial consideration. The battery team evaluates the cost impact of performance requirements in order to help maintain the vehicle target price. The final result of this battery analysis is defining the cell type as well as number of cells per module and number of modules in the battery pack.
How well do you really know your competitors?
Access the most comprehensive Company Profiles on the market, powered by GlobalData. Save hours of research. Gain competitive edge.
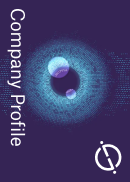
Thank you!
Your download email will arrive shortly
Not ready to buy yet? Download a free sample
We are confident about the unique quality of our Company Profiles. However, we want you to make the most beneficial decision for your business, so we offer a free sample that you can download by submitting the below form
By GlobalDataIn parallel to the battery team, the body-in-white (BIW) team will take vehicle requirements into consideration for initial car body design exploration. The BIW team considers how to package both mechanical and electrical systems into the vehicle while meeting the packaging and performance requirements.
The battery pack performs a key powertrain function, but due to its location and size it must contribute to structural integrity by helping provide BIW strength, stiffness and durability, particularly with regards to crash and safety considerations. While locating the battery pack under the vehicle floor is common practice, it does make it vulnerable, especially to side-impact crashes. Protecting the pack is a packaging challenge for the BIW team as additional space may be needed around the battery pack for crumple zones.
The BIW team also considers the integration of passenger compartment amenities. An increasingly complex set of in-car facilities not only drive power demand but also add to the packaging challenges. When the pack is placed under the floor of the car, it is essential to consider passenger comfort. How hot will the batteries run? What impact will that have on the cabin? How noisy will it be? Will there be excessive vibration?
The key outcome from the BIW team is an allowable battery volume that will be presented to the battery team. This volume, in combination with the battery team’s initial parameter definition of type/number of cells and layout, becomes the starting point for the battery team to explore battery layout options.

The BIW and EV battery teams now collaborate to maximize the number of cells in a given volume without sacrificing thermal and structural integrity of the pack. The goal is to ensure that the specified cell count required for power output and thermal performance can be packaged within the target volume.
Cooling and other components such as electronics that need to be placed within the pack must also be considered at this stage. Coolant channels layout is an important design choice, as it can have an impact on battery performance and safety, as well as overall packaging. The choice of cooling systems can also affect the ability to package into the target volume provided by the BIW team. An effective way to undertake this design effort is by leveraging a CAD-embedded CFD thermal management simulation that allows engineers to conduct design trade-offs in an automated way without the need for clean geometry or for addressing meshing issues.
Having received the details on the battery requirements, in terms of module dimensions, weight, quantity, and other areas that need to be reserved within the battery pack, the BIW can now evaluate structural design alternatives for the battery pack enclosure.
The battery pack enclosure must fit all battery pack components while contributing to the overall vehicle structural and crash-worthiness goals. The battery pack frame and structural components such as cross beams must be designed in such a way to properly arrange and fit battery components within the desired pack volume.
Throughout this process, analysis must keep overall weight in check. If the battery pack weight is over target, engineers may need to reduce weight through redesign of battery pack enclosure. This may involve switching a component to lighter material. For example, one could substitute composite material for aluminum to maintain stiffness while achieving a significant weight reduction. Composite design simulation tools can be used to make sure the composite components are manufacturable and meet structural requirements.

Although the need for collaborative design exploration between battery and BIW teams is recognized, execution can be challenging. True collaboration can only happen with a shared design language, shared data and ultimately a single, unified platform. Having access to a shared software platform that allows BIW team and the battery team to see each other’s data and analysis is bound to make EV design a smoother and more efficient process.
Further details:
For more information on technologies being discussed, click here.