The world’s first commercially-available brake-by-wire systems arrived in early 2002, when DaimlerChrysler launched the latest version of its SL Grand Tourer, writes Anthony Lewis. The system in this vehicle was jointly developed by Bosch (assisted by the provision of Motorola components and expertise) and Mercedes-Benz, but is an electro-hydraulic, rather than a true electro-mechanical, system – and ought really be considered an interim product.
Anticipating changes to legislation allowing by-wire systems and the change over to 42-volt power circuitry, major brake systems developers such as Continental Teves, Delphi and TRW are working on the development of brake-by-wire packages. Continental Teves, for example, has apparently already developed an effective hub unit which eliminates the need for today’s hydraulic units, and all have control systems which provide the required level of driver feedback.
Discover B2B Marketing That Performs
Combine business intelligence and editorial excellence to reach engaged professionals across 36 leading media platforms.
In common with other elements of the drive-by-wire vehicle, reduced installation, inventory and component costs are likely to be benefits. As Bosch and Mercedes-Benz have already demonstrated with the SL package, the system provides greater scope for use of anti-lock, anti-skid technologies. Taking this to its logical conclusion the system can be integrated with collision avoidance systems with far greater ease than could be achieved today with hydraulic-based systems.
Data from wheel speed and slippage sensors, external hazard sensing and other salient inputs will be capable of ultra-fast processing by the system’s control unit, with appropriate responses being made automatically by the vehicle. This, in theory at least, is likely to be co-ordinated at a faster rate than any driver would be capable of achieving.
Mercedes-Benz says that its Sensotronic Brake Control (SBC) electro-hydraulic brake system in the E-Class is “another milestone in automotive technology . . . fitted as standard on all model variants (it)pushes open the door to the future world of “brake-by-wire” systems.”
The most important characteristics of Sensotronic Brake Control include the extremely high dynamism with which pressure is accumulated and the precise observation of driver and vehicle behaviour using sophisticated sensors. With these features, the innovative system offers a significant plus in terms of ride safety.
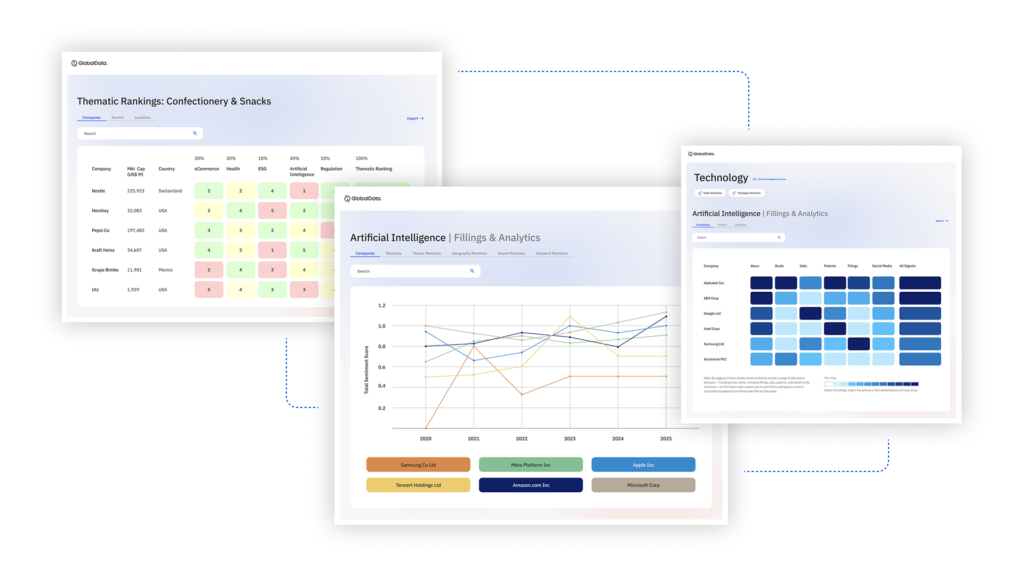
US Tariffs are shifting - will you react or anticipate?
Don’t let policy changes catch you off guard. Stay proactive with real-time data and expert analysis.
By GlobalDataOn emergency braking SBC recognises a quick switch by the driver from the accelerator to the brake pedal as an indication of an emergency situation and can react automatically. With the aid of the high-pressure accumulator, the system increases the pressure in the brake cables and applies the pads to the brake discs, which can then act immediately with full force when the driver steps on the brake pedal. As a result of Brake Assist, which also triggers earlier, the stopping distance is shortened.
Where there is a risk of skidding, SBC collaborates with the Electronic Stability Program (ESP), which keeps the car safely on track using specific brake impulses at individual wheels and/or by reducing the engine torque. As a result of even more rapid and even more finely metered brake impulses from the SBC high-pressure accumulator, ESP can stabilise a swerving vehicle early and, at the same time comfortably.
In the wet Sensotronic Brake Control ensures, with regular, short brake impulses, that the film of water on the brake discs is wiped off so that SBC can always operate with full effectiveness. This automatic brake drying function is activated when the windscreen wiper has been operating for a specified time. The brake impulses are precisely metered so that the driver is not aware of them.
When braking on bends SBC offers more safety than a conventional braking system. Depending on the ride situation, the variable brake force distribution proves particularly advantageous in actively influencing the self-steering behaviour of the vehicle. While conventional brake systems always meter the brake pressure at the wheels on the inside and on the outside of the bend in the same ratio, SBC can apportion the brake force according to the situation in hand. The system automatically increases the brake pressure at the wheels on the outside of the bend, because they can also transmit more brake force as a result of the higher wheel contact forces. At the same time, the brake force at the wheels on the inside of the bend is reduced to benefit the lateral traction forces which are important for directional stability. The result is more stable braking with optimum deceleration.
SBC also has additional convenience functions which offer even greater levels of safety and comfort. These include the Softstop function which enables the vehicle to come to a stop particularly smoothly, which is highly appreciated in stop-and-go traffic with frequent traffic lights. Sensitive pressure control makes this possible. The Softstop function is always active – the system only gives priority to rapid deceleration during emergency braking or slow manoeuvring.
In conjunction with the automatic transmission, Sensotronic Brake Control now also comes with Tailback Assist which can be activated using the cruise control lever while the vehicle is stationary or on the move at speeds of up to nine mph. This system is of benefit in stop-and-go traffic, since the driver only has to use the accelerator pedal; when the accelerator pedal is released, SBC brakes the car to a standstill with constant deceleration. Tailback Assist can remain active up to a speed of 37 mph, if required; it switches itself off automatically at higher speeds.
In a paper presented to the 2002 SAE Congress in Detroit, Delphi Automotive Systems, Infineon Technologies, Volvo Car Corporation and WindRiver gave details of their BRAKE project to use microelectronics technologies to design a brake-by-wire system.
The consensus is that software will play a greater role in defining the character and brand of the vehicle, and the vehicle manufacturer, as system integrator, will have to define the behaviour of the total vehicle in terms of function, performance, comfort, endurance, safety, etc to differentiate with respect to competitors.
The driver will no longer experience the characteristics of the “real car”, so much as the characteristics of a virtual car model the carmakers want to brand. The system vendors will provide modules that plug into this vehicle-level system. Interfaces allow the integration of these modules at the vehicle level.
Car manufacturers jointly with the ECU suppliers and electronic device vendors, supported by tool suppliers, must innovatively expand their system development to meet this new challenge of complex automotive “super-systems”.
The automotive industry continues to use mechanical subsystems with electronic control because:
- Electronically supervised systems increase the reliability by continuously testing the system components.
- Features can be introduced into the car more quickly and more easily than mechanical systems
- Digital communication between vehicle subsystems enables new and greater authority vehicle level functions
Until recently electronic control has mainly been used to control and to supervise the functionality and to adapt the behaviour of mechanical systems. In case of an error within the electronic control, the performance of the mechanical system is reduced, while still providing minimum functionality. This is known as fail-safe operation. System requirements in the future can no longer be met with fail-safe operation.
Brake-by-wire systems will no longer have mechanical backup and in the presence of an error, the electronic system will have to provide minimum functionality, and ensure that errors are confined. In addition, as vehicle systems transition to brake-by-wire, it will no longer be the mechanical design that defines the character of the vehicle (comfort, handling, and performance), but software function.
This means that the interface between customer and supplier becomes more complex including mechanical, electrical, and software interfaces. Since the character of the vehicle ultimately forms part of the OEMs’ brand differentiation, then many OEMs will want to become more involved in the control software definition.
Today, the responsibility for software development for x-by-wire systems and the subsystem knowledge commonly resides with the suppliers.
Furthermore, the suppliers have greater knowledge of how to control their actuator, whilst the OEM determines how it will control the vehicle. This creates the need for software partitioning and OEM-Supplier interfaces.
By working on an appropriate methodology and tool infrastructure the project enables the development of a distributed control algorithm and the subsequent allocation of the resulting control tasks to a network of distributed control units.
The BRAKE architecture consists of four such control units, each of which is located at or near one of the vehicle’s wheel brakes. Having sufficiently powerful electronic control units to run the necessary software components, and an appropriately designed operating system, centralised control schemes will become obsolete.
A key part of the software running on an ECU is the proposed operating system that is designed according to the time-triggered concept which allows complete separation of tasks (task encapsulation). In case of a faulty task, the operating system is able to enter a “silent state” (failsilent). Error detection exploits the fact that the brake system has four wheels. Each wheel brake control unit computes the required braking torque for itself and each of the other wheel brake control units. A fault tolerant communication system is used to communicate the real time image of each of the wheel brake units.
In contrast to the more conventional approach with central master and local redundancy the total number of required individual electronic control units is significantly reduced. The BRAKE project also contributes to the definition of open interface standards, using open system concepts to reduce the dependency on specific suppliers and products.
In particular the focus is on:
- The interface between the brake actuator’s control circuitry and the brake’s electronic control unit
- The interface to the communication system
- The interface between upper control layers. The project began by establishing a brake system architecture that meets the automotive requirements for safety and reliability, utilising the inherent redundancy of a braking system. In order to leverage this inherent redundancy, each brake actuator is able to function with some level of independence. This means that the control software is no longer centralized, but de-centralized.
Significant challenges arise in the implementation of such architecture, specifically:
- Global time synchronization between ECUs and processes to ensure accurate calculation of vehicle states from sensor inputs
- Deterministic actuation of wheel brakes with the respect to brake demands
- Composability of brake system elements
- Encapsulation of sub-systems and faults
|
Advanced braking functions such as anti-lock braking, traction control, vehicle stability and chassis control allow optimization of vehicle braking and stability but are not required for basic deceleration performance. These functions may remain centralised with fail-safe behaviour allowing maximum integration with other chassis systems, for example in a vehicle supervisory role. The scope of this project is to ensure base brake functionality, whilst at the same time identifying the interfaces required to allow communication between distributed subsystems and vehicle level systems
As more and more automotive systems can no longer rely on mechanical backup, they have to provide deterministic behaviour even in the presence of faults. Today’s approach for fail-safe operation is to build each system unit (ECU) redundant in order to achieve safety.
As systems grow in complexity and previously separate systems share information and start to interact, they become hard to verify and even more difficult to ensure fail-safe operation. This project uses the inherent distributed redundancy of the brake system in order to provide fail-safe/fault tolerant operation instead of adding redundancy to particular nodes.