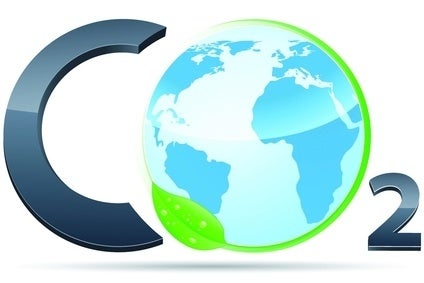
The main forces driving automotive emission technology are, of course, the ever increasing stringent emissions regulations worldwide. These in turn are triggering a raft of innovation in developing fuel efficient engines such as diesel or lean burn gasoline engines with high demands in particulate emissions reduction and NOx reduction technology. Alternative fuels are another viable way to reduce CO2. For this second part of our management briefing, we talked with executives of Aeristech, Zircotec and Federal-Mogul about trends in after-treatment, exhaust coatings and ‘upstream’ factors influencing emissions as part of a move towards higher energy ignition systems.
Consumers, and therefore automakers, are increasingly focused on, and governments are increasingly requiring, improved fuel efficiency and reduced greenhouse gas emissions in vehicles.
The desire therefore to lessen environmental impacts and reduce oil dependence is spurring interest in green technologies and alternative fuels. As such, there is continued focus on production of hybrid and electric vehicles because of their fuel efficiency, and developing ethanol, hydrogen, natural gas and other clean burning fuel sources for vehicles.
Among those leading players doing their bit to push back the emission technology boundaries are Federal-Mogul, Aeristech and Zircotec.
Federal-Mogul’s innovations
We are seeing an increasing focus on the ‘upstream’ factors influencing emissions as part of a move towards high(er) energy ignition systems.
How well do you really know your competitors?
Access the most comprehensive Company Profiles on the market, powered by GlobalData. Save hours of research. Gain competitive edge.
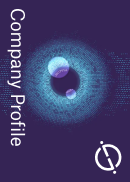
Thank you!
Your download email will arrive shortly
Not ready to buy yet? Download a free sample
We are confident about the unique quality of our Company Profiles. However, we want you to make the most beneficial decision for your business, so we offer a free sample that you can download by submitting the below form
By GlobalData“Fuel economy optimisation is driving higher energy requirements”, says Sandro Pino, Federal-Mogul’s European Application Engineering Manager, Powertrain – Ignition Products. “Higher energy requirements are also driving advances in spark plug technology to ensure wear characteristics of the materials chosen meet the service interval required.”
Pino adds that increased engine efficiency further introduces other potential problems with engine operation. “Abnormal combustion under low speed, high load operation is now something that needs to be controlled. Spark plug designs must be capable of resisting these adverse conditions. We are developing higher energy systems in order to ensure greater combustion efficiency, essentially making the spark more visible for a longer period or using higher energy in one burst to guarantee the fuel ignites efficiently.”
Federal-Mogul Powertrain has also pushed back the technical boundaries of ceramic insulator technology and insulator design in addressing the increasing voltages and thermal demands of high-output gasoline engines. The supplier’s latest range of spark plugs, called SureFire Plus uses this technology to manage voltages of 42kV or more, compared to 36kV previously. Pino adds: “The improved ceramic performance allows the use of smaller insulator diameters that package more easily into the crowded cylinder heads of multi-valve downsized engines.”
Q&A with Aeristech
Aeristech is a UK-based clean technology innovation business that is developing a range of electrically driven pressure charging technologies that aims to help solve the driveability, emissions, integration and cost challenges facing the next generation of high efficiency petrol and diesel engines.
As powertrain engineers seek constant improvements in engine efficiency, often through downsizing and boosting, they are exposing the limitations of existing turbocharging and supercharging technologies. In a recent interview with Aeristech, we learned about the latest developments in this area and what they could mean for future vehicles.
The company is working with vehicle manufacturers and suppliers to licence innovative proprietary technologies to reduce tailpipe emissions, increase fuel efficiency and heighten driving characteristics of the next generation of ‘right-sized’ diesel and gasoline engines. We caught up with Bryn Richards, CEO of Aeristech to discuss some of the latest trends in emissions control and after-treatment technology.
As emissions regulations become more challenging, how is this driving trends in after-treatment technology?
The intention to move to real world drive cycles, in conjunction with lower limits on tailpipe emissions, will make effective control during transients even more important. As so many engines, both gasoline and diesel, are downsized and heavily boosted nowadays, the after-treatment system and the boosting technology must be considered as part of an integrated approach in order to provide the required driveability, emissions and fuel economy at the minimum cost.
In such an approach, a turbocharger becomes a constraint on progress; it is at its least effective under transient conditions and introduces thermal mass and inertia into the exhaust stream, making it more difficult to maintain catalyst temperature when running at part-throttle. A more holistic approach would combine a cost-optimised catalyst specification with boosting on the cold side of the engine.
Does that mean a supercharger? Surely they just introduce other issues?
The limitation of a conventional mechanically-driven supercharger is that it constantly consumes some of the power the engine produces, unless connected through a clutch which can, in itself, introduce issues for the accessory drive when re-engaging. The rotational speed of a mechanical supercharger is a function of engine speed, so air delivery increases with crank speed, leading to the inefficient wasting of surplus air under some operating conditions.
The alternative is an electrically driven supercharger but a 12v system is so severely power limited that it is only really capable of providing infill torque at low engine speeds during transients. This gives some improvement in driveability to a downsized engine but still relies on the turbocharger to provide steady-state boost at all engine speeds, and this becomes increasingly difficult as boost levels increase.
What is required is an electric solution that can give sufficient continuous boost to provide a useful increase in steady state output while decoupling the compressor speed from crankshaft speed. Many industry predictions agree that we are going to see 48 volt systems become increasingly popular as a highly cost-effective basis for future mild hybrids and this provides an opportunity to overcome the normal issues that arise with supercharging.
Is that the basis of the Aeristech eSupercharger – 48 volt architecture?
There’s a lot more to it than that. The use of 48 volt architecture provides the necessary power to deliver useful levels of boost – over 2.5 Bar – but our eSupercharger is the first one capable of continuous operation at this boost level. We have overcome the thermal management issues that normally restrict electrically driven superchargers by using permanent magnet motor technology in place of the more usual switched reluctance type. We have made this cost-effective by developing patented control and switching technology that enables the use of many low cost components.
We also use a high speed centrifugal compressor with a higher efficiency than a typical screw-type compressor, which reduces the heating of the intake charge and helps to reduce the high combustion temperatures that increase NOx formation.
Our capability to run at speeds up to 150,000 rpm with low mass, low inertia motor designs means we can operate with the fastest possible transient response, from idle to target speed in <400ms. This helps to eliminate lag and also reduces the workload for the catalyst by avoiding peaks in engine-out emissions during transient load changes.
Diesel engines will need expensive exhaust filtration systems to meet the emission regulations. Can electric forced induction systems make a contribution here too?
The ability to match the air supply to the fuel input at low engine speeds would both cure the emission problem and improve fuel economy. It makes better sense to convert emissions to useful energy, rather than filtering them out of the exhaust. Filters are inherently inefficient in that they increase the pressure drop in the exhaust system.
Q&A with Zircotec
UK-based Zircotec is a specialist coatings company that produces a range of proprietary plasma-sprayed metal and ceramic coatings to protect materials from the damaging effects of heat, abrasion and wear.
Zircotec recently announced that it had secured a number of new OEM contracts for both OE automotive and motorcycle exhaust coatings, marking a step change in the volumes its UK-based factory is now producing. To find out a little more about the intricacies of exhaust coatings, we spoke to Peter Whyman, sales and marketing director of Zircotec Ltd.
Why coat exhausts?
There are many varied reasons for coating an exhaust system, mostly related to thermal management. A Zircotec plasma-sprayed ceramic thermal barrier coating will significantly lower exhaust temperatures – reductions by 33 percent – resulting in lower engine bay temperatures (<50oC have been reported). This in turn gives a lower air intake temperature leading to increased engine performance.
Additionally, keeping the heat inside the exhaust gas allows the gases to flow more easily, increasing cylinder scavenging to create a supercharging effect – to provide further power gains – and allowing turbochargers to become significantly more responsive.
With engine compartments becoming more and more tightly packed, a Zircotec coating can protect vulnerable components located close to the exhaust avoiding heat damage and increasing component life. Lower exhaust component temperatures also reduce heat soak through foot wells, bulkheads, etc. so drivers are potentially cooler, more comfortable and more able to concentrate.
What parts can be ceramic coated?
A Zircotec coating can be applied to each and every part of an exhaust system from manifold to tail pipe, including catalytic convertors and diesel particulate filters which have been shown to work more effectively due to increased exhaust gas temperatures with faster ‘light up’ and potential to reduce emissions.
How is demand shaping up with exhaust coatings?
Demand for exhaust and high temperature coatings is increasing both for the performance and protection benefits previously listed and there is a great demand for engine compartment beautification. Enhancing the look and perceived quality of an engine bay, providing visual differentiation for special editions and being robust, sealed and easily maintained it ensures tailpipes, often prone to unsightly corrosion and staining stay, stay looking good. In addition, the coating is resistant to stone chips and has passed numerous OE lifecycle tests.
See also: August 2015 management briefing: Innovative emission technologies (1)