Two recent natural events, the Japanese tsunami in March 2011 and more recently the autumn floods in Thailand were both human and economic tragedies and showed that man, whatever his illusions, is still not master of the planet. At a more practical industrial level, should they also be seen as a wake-up call to global industry to reassess its supply-chains, sourcing philosophy, dual sourcing and strategic risk management?
These two recent events may well justify some further lateral thinking. These notes seek to address three principal issues at a very high level – first the immediate and practical issues of the Japanese tsunami and the Thai autumn floods, second, highlight some of the strategic issues arising from the aftermath with regards to dual sourcing and risk management and, thirdly, comment on some of the longer-term issues and the need for their possible re-examination.
Tsunami, Thai floods and the aftermath
The March 2011 tsunami was, in addition to the loss of 18,000 lives, an almost perfect storm. Not only was there a massive tidal wave which treated flood protection with contempt, but it wiped out a number of towns and villages in the north east of Japan. The earthquake itself damaged communications, factories, homes – and nuclear power installations.
Japan relies on nuclear power for a third of its electricity and its industrial might has a voracious appetite for power. An immediate response to the tsunami was to cut back on nuclear power generation and manufacturing industry across the country suffered as a result. Electricity was rationed and heavy users went onto load sharing work patterns to ensure the best use was made of capacity. Some activities moved to night or weekend working.
The immediate reaction to the tsunami was that productivity dropped significantly and even by year-end the recovery is far from complete. We are yet to hear the full assessment of the Thai floods.
Within the automotive sector there have been a number of issues which have stretched way beyond the immediate tsunami. Consider some of them:
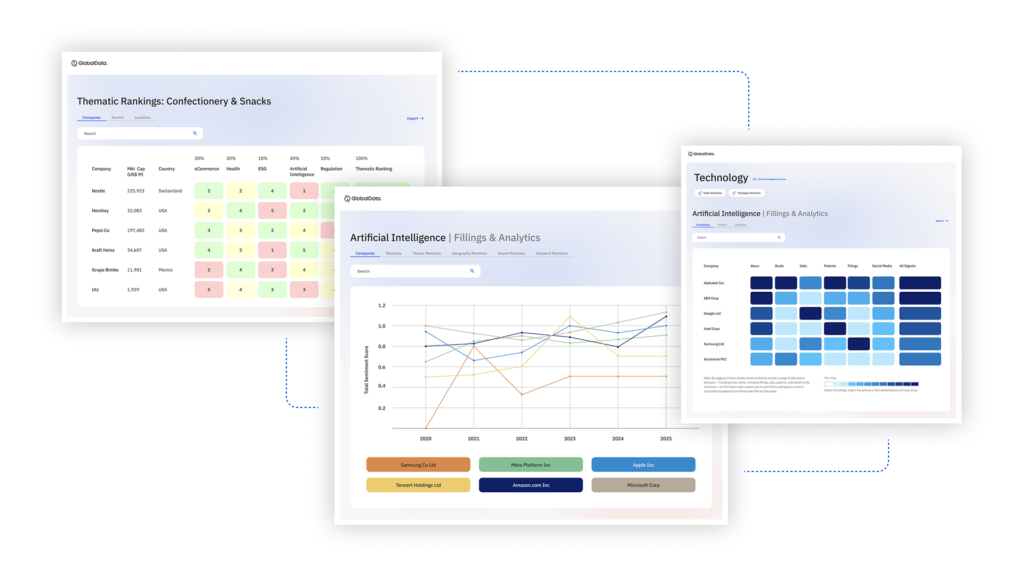
US Tariffs are shifting - will you react or anticipate?
Don’t let policy changes catch you off guard. Stay proactive with real-time data and expert analysis.
By GlobalData- Toyota reported that as at the end of June they were still missing some 30 critical parts;
- A global premium car manufacturer was having problems in terms of supply or a red paint pigment single sourced in Japan;
- Honda in the United Kingdom has been on part-time working since the tsunami and anticipates coming back to full working towards the end of the year, maybe a little later. However, their labour flexibility arrangements should help them catch up on lost production.
- Subaru in the UK indicated it would have no new product until 2012 because of the destruction of a key electronics components facility. Dealers will have to make do with used vehicles and service business;
- Suzuki has confirmed that it will spend half a billion dollars on relocating an electronics facility away from the sea.
Some commentators have suggested the impact of the autumn floods in Thailand could be almost as devastating with the large amount of assembly and component making that it embraces, but as yet the full situation may not have crystallised.
One could quote many other examples from across the whole of the automotive industry. Reports suggest that the biggest, often unperceived Achilles’ Heel in Japan and Thailand has been the Tier 3 and Tier 4 players which do not necessarily have the wherewithal to develop contingency plans and elaborate schemes to enable them to bounce back.
A number of organisations have expressed concern at this hidden weakness in the supply-chain with single sourcing strategy and multiple tiering.
The tsunami impact could be called ‘rolling’ in that some players did not suffer immediately but only now are starting to feel the impact as the supply-chain empties.
Further down the line, national sales companies and dealers may have been starved of single source aftermarket parts if those scarce supplies have been sucked back into vehicle assembly by OEMs or the supply chain.
Perhaps the biggest strategic impact of the tsunami will be its influence on Japanese nuclear power policy. The Japanese nuclear industry supplies a third of the country’s electricity. Given the problems with the earthquake and tidal waves, future location policy is under challenge as, indeed, is the very future development of a nuclear industry. Japan has no significant sources of oil or coal.
The demise of dual sourcing?
It might be claimed dual sourcing has been the victim of its own success in manufacturing and quality assurance.
Given a facility, whether in Japan or Thailand, that produces an output with a one in a million or one in ten million failure risk why should a global player not take every advantage of that capability and seek to minimise material and sub-assembly acquisition costs by opting for single sourcing?
The problem has been perhaps, as already noted, with many Tier 3 and Tier 4 suppliers. They may provide simple components or sub-assemblies but, at the same time, have all of the expertise and unique production capability gathered in one small, but high volume facility or work as an integral part of a major supply chain.
It would appear that electronics components and sub-assemblies such as engine sensors, sourced from a single supplier are one of the major problems and a modern car cannot be built without them.
In the ceaseless hunt for lower costs there has been a steady growth in single sourcing because production has reached such a high level of perfection – a true victim of their own success indeed.
The ghost is only now starting to come out of the shadow as to the risks of single sourcing on a global basis. Not only will domestic finished goods capacity collapse, given any serious disruption, but a global operation could be halted all too easily.
Strategic reserves of a key finished product could be held in inventory, but that has a cost which might offset or delete the benefits. Would any strategic reserve – ‘product insurance cover’ – be economic, or does one take the chance of an occasional breakdown and write that off?
Prolonged disruption is a different matter. But consider the risk management issues associated with single sourcing.
Risk management and single sourcing
Every organisation practices some form of risk management in terms of both the key generic issues and also some of the specific ones unique to the organisation, the product or the economics.
The principal risk management elements in any single source manufacturing decision might be summarised as follows:
- Economics; will production costs remain acceptable – and what might be the impact of any strategic changes in currency? Relationships between currencies appear to be changing – consider the historic under-valuation of Chinese currency, for example, or the impact of the cheap dollar.
- Political; within this heading one might consider such issues as ‘the Arab Spring’ and its backlash. Equally, one might ask regarding the political manifestations of the government in power. Is that a risk which may continue and spread to manufacturing locations. More material is being acquired from developing or politically unstable countries. How secure, strategically, is China – and could critical sourcing be used as a political weapon?
- Technological; perhaps the most compelling reason for single sourcing are the benefits from a single large state of the art plant. Would two lesser capacity plants in different location be a justifiable step investment-wise? Should one look toward significant strategic stocks with all the problems that can create?
- Social risks; historically these have been strongly linked with labour relations. A plant could be built in an area of low social risk but political landscapes can change quickly. Dictators can fall suddenly and their replacements may be just as ruthless but not be as effective in business.
- Climatic and geographical; historically perhaps not granted the visibility it deserves but climatic and geographical conditions are becoming more important. Global warming is causing increased unpredictability – whether through hurricanes, rainfall, snow or other concerns. The apparent slowdown in emissions management caused by recession may accelerate the level of risk.
Ever-increasing globalisation and the emergence of four manufacturing blocs – North America, Western Europe, Far East and increasingly South America – might suggest single sourcing is no longer a realistic option. The geographic location of a single source plant, or dual locations can take on increased importance with the migrating motor industry.
The risk of single global sourcing may also have serious implications for both locational and dual sourcing into the supply-chain.
Dual sourcing – a strategic dinosaur?
To this writer’s generation, dual sourcing was a mantra; single sourcing anathema.
There are perhaps three principal strategic risks beyond those highlighted in the previous paragraphs. Consider them: 1) What would be the impact on unit costs and quality of moving to single sourcing when additional logistics and inventory costs have been built into the equation? 2) Are there sufficient volume demands to justify dual sourcing or would two smaller scale production facilities be more risk averse at a marginal increase in cost – a cost of security. 3)Are there substitute products or redesigns which might be used if a single source facility were to fail?
Quite simply, given the growth in the wider spread of the global automotive industries, is it justifiable to rely on single sourcing for key components or should manufacturers look towards duplication within the supply-chain to ensure secondary sources are available – even if that means sharing with a competitor?
Product security would be the benefit of dual sourcing. It would be interesting to peer into the management accounts of the global automotive players to establish the true costs of the March tsunami or the Thai floods. That figure might indeed act as a benchmark figure for the cost of dual sourcing.
Some implications and conclusions
Cost reduction, silo management, globalisation, multi-tier sourcing have all benefited from the enhancement of logistics and logistics management. The logistics sector of the automotive industries may have to bear a disproportionate part of any significant supply disruption, however it is caused.
Dual sourcing may, in future, once again become a critical requirement. It’s ironic that dual sourcing may not be an issue to be driven by the actual manufacturing process but by the environment in which the associated supply-chain operates.
To quote the Spanish philosopher Paul Santayama ‘he who forgets history is condemned to repeat it’.
Professor Peter N C Cooke
University of Buckingham