BMW’s announcement last week of an additional GBP500m investment in its UK production network over the next three years also came with confirmation that the UK will be a production location for its next generation Mini models. It is also a part of a modular industrial strategy that will bring flexible plants that can make BMWs or Minis.
The creation of the Mini brand has been an extraordinarily successful project for the BMW Group. BMW took an iconic car with heritage and reinvented it as a modern premium small car brand in a manner that has been widely applauded.
The announcement last week that BMW’s UK facilities are to receive further investment for the next generation of Minis was not exactly unexpected. The GBP500m will be used to ready the Mini assembly plant at Oxford, the pressings plant in Swindon and the company’s engine plant at Hams Hall near Birmingham.
BMW chairman Norbert Reithofer and his board colleague Ian Robertson also explained to journalists how the planned investment fits into BMW’s modular industrial strategy. It boils down to making cars where you sell them so that you avoid adverse currency risks while also having plants with the flexibility to make the models that fit the strategic objectives.
Robertson points out that BMW Group is a global company with factories around the world and that it needs to take account of volatile markets and currencies.
“We have a simple philosophy which is to move production to where our largest sales operations are,” he says.
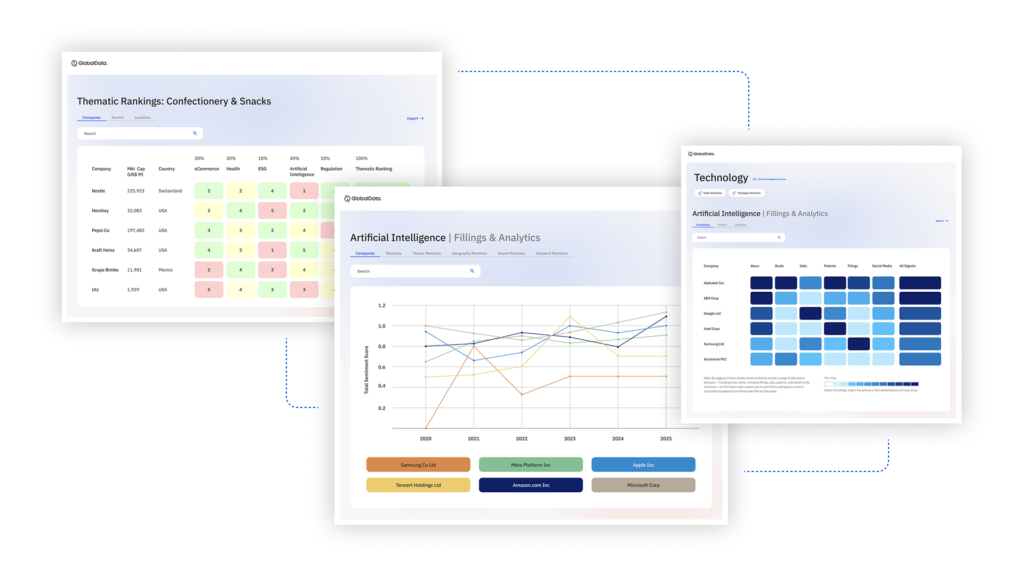
US Tariffs are shifting - will you react or anticipate?
Don’t let policy changes catch you off guard. Stay proactive with real-time data and expert analysis.
By GlobalData“In the years to come we will see more volatility in markets and more volatility in currencies and the only way we can manage that, ultimately is to manufacture and sell in as equal balance as you possibly can. It’s never completely accurate. We have a big operation in the United States and we have enormous sales in the United States; same in China and in many other markets around the world where we do manufacture. That trend will continue.”
It begs the question, if the Mini is so successful in the US, why not make it there?
“There’s no plan to make Minis in the US. We have just extended the X family in the US – so we have the X3, X5 and X6 there. Why is that? Well the biggest market for these vehicles is in the United States, so that makes real sense and we have extended our plant there, invested just shy of US$800m in the last two years. It [Spartanburg plant] now has a capacity of around 250,000 units. As we develop our business further, maybe there are other extensions in countries like the US, but it has to be seen against where we see our major markets and having the right balance. And it’s not necessary to say ‘well because we’re an integrated group and sell a lot of Minis in the US, so why not do that?’ We have an X project range in the US and that’s a deliberate move as well.”
But the future is more flexible and it is planned that BMW Group will be able to respond to market demands in a more agile way via modular production systems.
“Our plants will be flexible in the future with new modular systems, starting in the year 2013, 2014, 2015, so that plants will be able to produce Minis and BMWs and that is true for Oxford as well,” Reithofer maintains. “But we have enough product ideas for Mini to fill Oxford with Mini production,” he adds.
So there you have it; the option will be there to more easily make Mini cars in plants outside of the UK – should BMW ever want to do that. If the demand is there in 3-4 years’ time, it will make good business sense to make some (emphasis on some) Minis elsewhere. The BMW brand has shown how it can be done. They make BMW brand cars across the world. The cars still come heavily imbued with BMW brand values and most BMW cars are still made in Germany – the heart for the BMW brand the way Britain is for Mini. A BMW that rolls out of Spartanburg is perceived as a BMW, its production subject to BMW’s global engineering and manufacturing values, systems and quality thresholds. A similar strategy is surely not inconceivable for Mini if for no other reason than that capacity constraints are not too far off in Britain.
BMW believes that its assembly factories work best at capacities of around 250,000-270,000 cars a year because beyond that the logistics of managing a factory become a lot more challenging. You optimise scale benefits at that sort of level, according to Robertson and BMW does not want to build bigger volume factories.
Oxford’s Mini plant produced 219,000 cars last year and it has a capacity of around 250,000 units. The Mini Coupe and Mini Roadster will ensure that the plant starts to nudge capacity limits in a few years. What would the company do to crank out more Minis if global demand was substantially higher than capacity in the UK?
Reithofer emphasises that the new modular manufacturing system will enhance capacity utilisation for the BMW Group as a whole. “And then the question is on the table: what is the right production facility for the different cars?”
Clearly much will depend on the course of Mini sales over the next 2-3 years in places like the US, China and India. Decisions will be taken when the modular production system on next generation products is in place and according to market needs and prevailing economic circumstances. The important point is that BMW Group will be able to react more quickly and with greater flexibility when looking at the brand-plant-model mix.
Robertson is understandably upbeat about prospects for the Mini brand. “We see more growth, more expansion in years to come. It’s a brand that will continue to be developed,” he says.
Another example of the modular production strategy approach is in electric drive technology. The new BMW ‘i’ sub-brand will introduce the first BMW Group electric cars in 2013 – the i3 Mega-City electric vehicle and the sportier i8 hybrid. The plan is that the engineering architecture will be shared across BMW Group brands – ie BMW and Mini also – in line with evolving market needs.
Reithofer once again emphasises the importance of flexibility in production and the importance of possessing a global manufacturing footpint.
“We are confronted with currency issues more and more. Flexibility gives us more room to move in the future, more quickly.”
See also: UK: BMW announces new investment for UK facilities