Hexagon has been honored with the Innovation Award in Precision Manufacturing in the 2025 Just Auto Excellence Awards for its pivotal role in advancing quality, efficiency, and adaptability in automotive and motorsport production. Through its nearly 20-year partnership with Oracle Red Bull Racing (ORBR), Hexagon’s hardware, software, and expertise have enabled the team to manage rapid design changes, ensure regulatory compliance, and deliver consistent, high-performance results in one of the world’s most demanding engineering environments.
The Just Auto Excellence Awards honor the most significant achievements and innovations in the automotive industry. Powered by GlobalData’s business intelligence, the Awards recognize the people and companies leading positive change and shaping the future of the industry.
Hexagon’s recognition reflects the transformative impact of its precision manufacturing technologies, which have set new benchmarks for performance and reliability in both motorsport and automotive manufacturing.
Precision manufacturing enables consistent, high-quality production
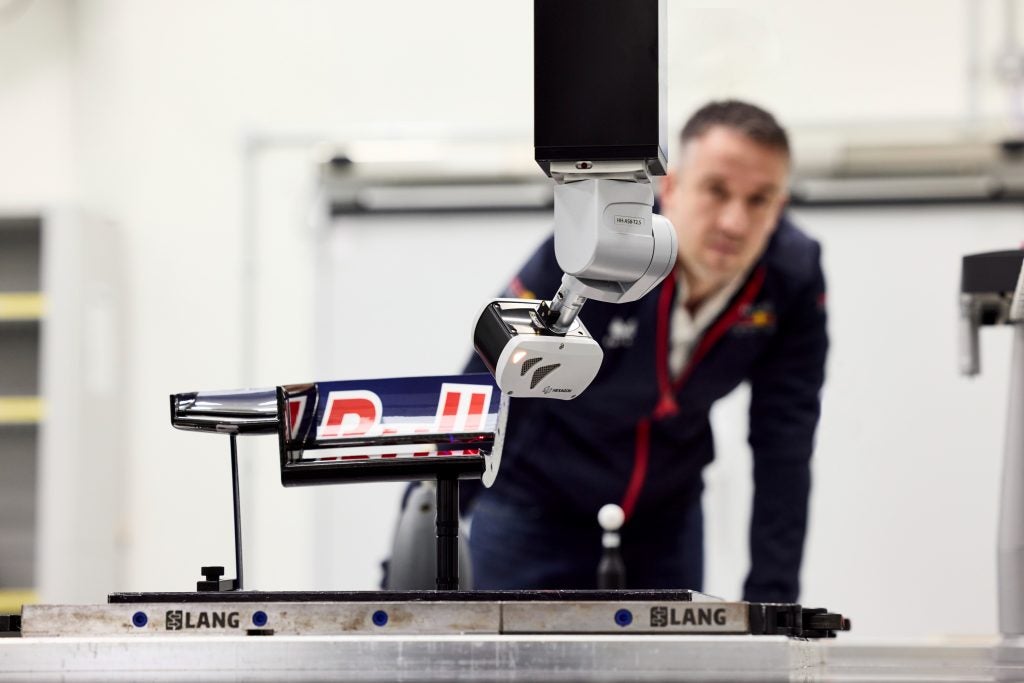
A core reason for Hexagon’s Innovation Award is its transformative impact on manufacturing consistency and quality in Formula 1. The pace of development is relentless, with ORBR executing between 15,000 and 20,000 design changes each season – an increase that underscores the complexity and speed of innovation required at the highest level of motorsport. Teams have a short amount of time to develop the car for the next season, making first-time-right manufacturing essential. Hexagon’s advanced hardware, such as the HP-L 10.10 scanner head and Absolute Arms, and industry-standard software solutions including PC-DMIS, VG software, and QUINDOS, provide the high-resolution measurements and actionable insights needed to ensure every part, from chassis elements to intricate engine components, matches the original design intent.
This precision extends to the smallest details, including the thickness of a single layer of paint, which can influence aerodynamics and performance. Hexagon’s CMMs are used in both internal and external inspection rooms, while their trackers support composite inspection and trackside verification. The Absolute Arms are also used for car setup and to ensure bodywork geometry remains FIA compliant. During race weekends, when the car is disassembled into approximately 8,000 parts for transport and must be reassembled with absolute accuracy at the next venue, Hexagon’s laser trackers are deployed trackside to verify that every component is correctly positioned, ensuring the car performs as intended under race conditions.
By delivering this level of precision and reliability, Hexagon’s solutions help ORBR maintain the consistency and quality required to compete at the highest level, while also supporting compliance with the strict technical standards set by the FIA.
Digitalization and data capture drive performance improvements
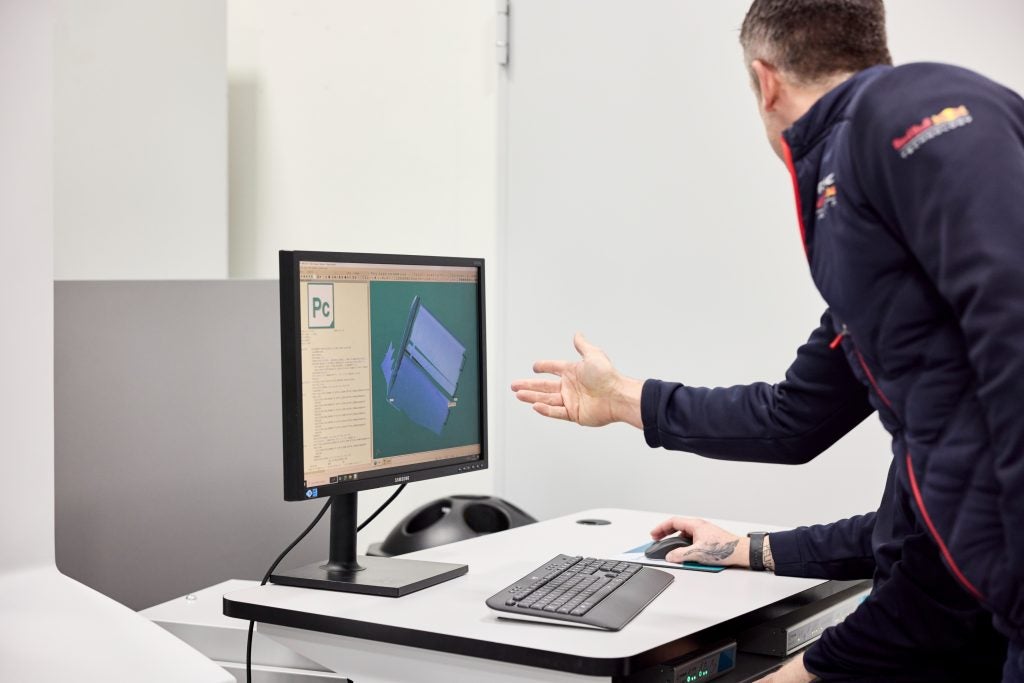
Hexagon’s award-winning approach extends beyond physical measurement to advanced digitalization and data analytics. Each race generates several hundred GB of data, collected from sensors, laser scanners, and metrology devices. Hexagon’s software solutions, such as PC-DMIS, VGSTUDIO MAX, and QUINDOS, transform this data into actionable information, enabling ORBR to accelerate the learning curve between design and testing and to support continuous quality optimization.
The speed and accuracy of Hexagon’s data capture technologies enable ORBR engineers to iterate designs quickly, implementing changes between races or even within a single race weekend. For example, if a new aerodynamic component is introduced, Hexagon’s systems can verify its conformity to design specifications and provide immediate feedback on its performance. This rapid feedback loop is critical in a sport where the ability to adapt and innovate faster than competitors can be the difference between winning and losing.
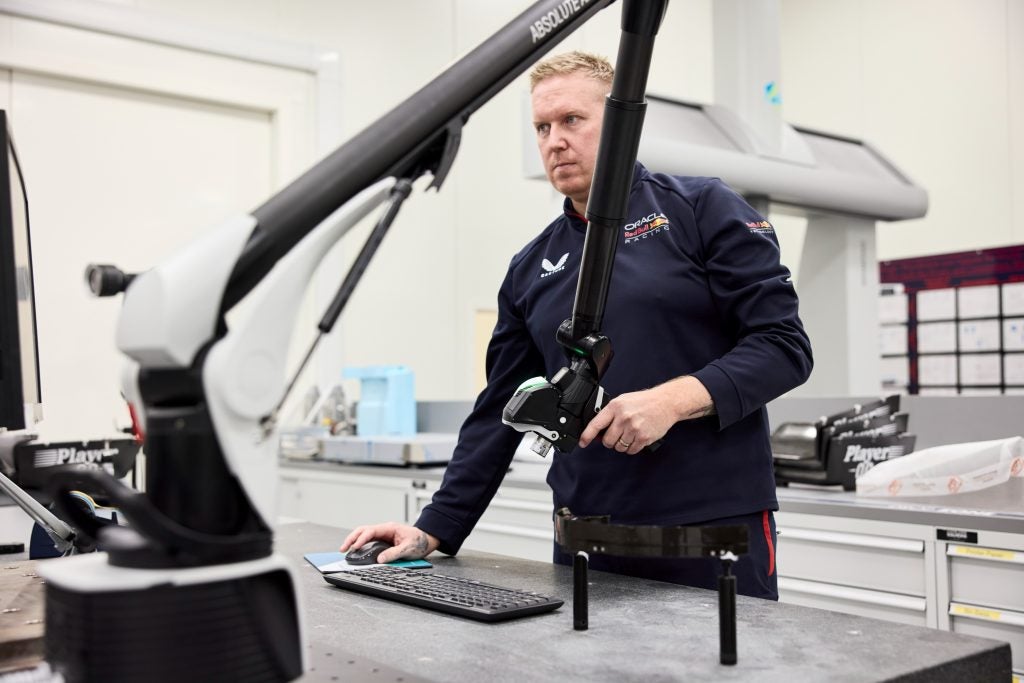
Moreover, the integration of digital quality inspection into the manufacturing workflow has led to a significant reduction in faults – by 50% over two years. This improvement not only enhances reliability on the track but also ensures that all parts meet the rigorous standards required by the FIA, including those related to safety, technical compliance, and cost control under the sport’s expenditure cap. The FIA’s adoption of the same Hexagon hardware further reinforces trust in the data and ensures that compliance checks are consistent and reliable across the sport. By embedding digitalization at every stage, Hexagon empowers ORBR to make data-driven decisions that enhance both performance and operational efficiency.
Supporting regulatory change and next-generation powertrains
Hexagon’s ability to support ORBR through regulatory change is another key factor in its award recognition. The Formula 1 regulatory environment is constantly evolving, with major changes set to take effect in 2026. These new regulations will require teams to redesign their cars to be more agile, competitive, and sustainable, with a particular focus on increasing electrical power and a shift to sustainable fuels. ORBR has responded by forming a dedicated team to develop its own next-generation powertrain, a complex undertaking that demands the highest levels of precision and adaptability.
Hexagon’s digitalization technologies are central to this transition. By providing ultra-fast, high-accuracy measurement and analysis tools, Hexagon enables ORBR to validate new powertrain components against stringent design and regulatory requirements. This capability is especially important as the team works to balance performance with sustainability, ensuring that new engines not only deliver competitive power but also comply with environmental standards. Hexagon’s technology will also be crucial for refining aerodynamics and maintaining competitive performance as the team adapts to the new regulations.
Additionally, Hexagon’s solutions support ORBR in managing the increased complexity that comes with regulatory changes. The ability to quickly adapt manufacturing processes and verify compliance with new rules allows the team to remain agile and competitive, even as the technical landscape shifts. The expanded partnership with Oracle Red Bull Sim Racing also helps to inspire future STEM professionals, further embedding innovation into the team’s culture. This adaptability is a key reason why Hexagon’s partnership is viewed as essential by ORBR’s leadership, particularly as the team prepares for the challenges of the 2026 season and beyond.
Influencing automotive manufacturing beyond motorsport
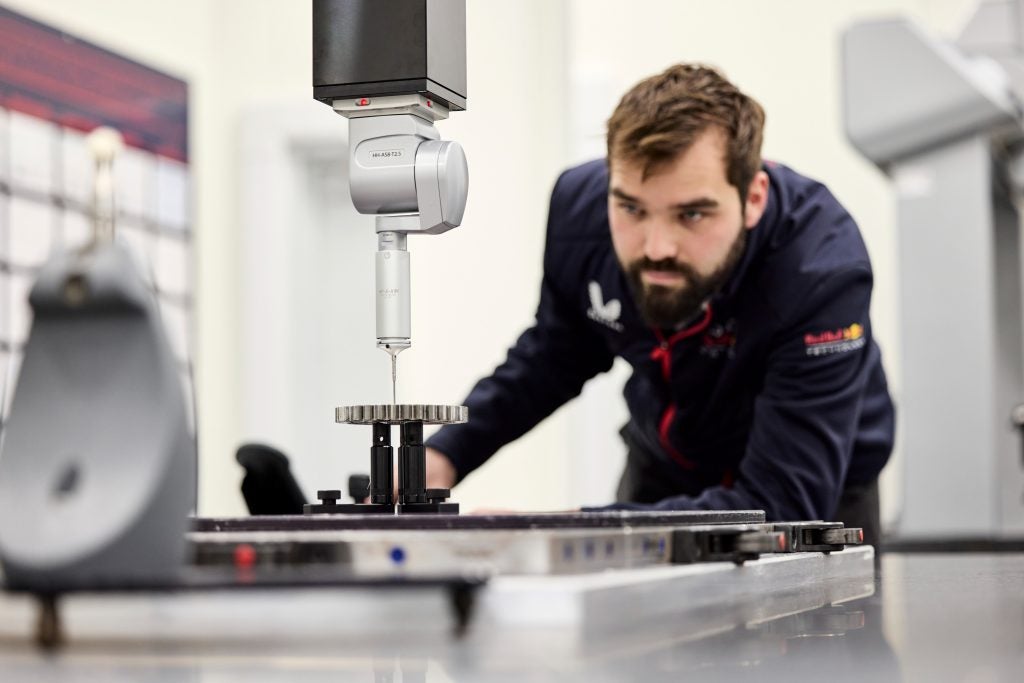
Hexagon’s influence extends well beyond the racetrack, which further justifies its Innovation Award. While its technologies have been proven in the high-pressure environment of Formula 1, their impact is now being felt across the wider automotive industry. Hexagon’s leadership in both contact and non-contact inspection, as well as precision scanning on any type of surface, has set new industry standards. The methodologies developed in partnership with ORBR—such as real-time digital quality inspection, rapid prototyping, and data-driven manufacturing—are being adopted by global carmakers seeking to accelerate time-to-market and improve production agility.
Automotive manufacturers face increasing pressure to reduce development cycles, enhance product quality, and respond quickly to changing consumer and regulatory demands. Hexagon’s solutions, refined through years of collaboration with ORBR, provide the tools needed to achieve these goals. For example, the ability to capture and analyze large volumes of manufacturing data in real time enables manufacturers to identify and address quality issues early, reducing the risk of recalls and improving overall efficiency.
Furthermore, the adoption of Hexagon’s technologies is helping to raise industry standards for precision and quality. As more manufacturers implement these advanced metrology and digitalization solutions, the benefits seen in motorsport—such as reduced faults, faster innovation, and improved compliance—are being realized on a global scale. The trust placed in Hexagon’s technology by both ORBR and the FIA underscores its value as an industry benchmark for precision manufacturing. This transfer of knowledge and technology from Formula 1 to mainstream automotive production highlights the broader significance of Hexagon’s achievements in precision manufacturing.
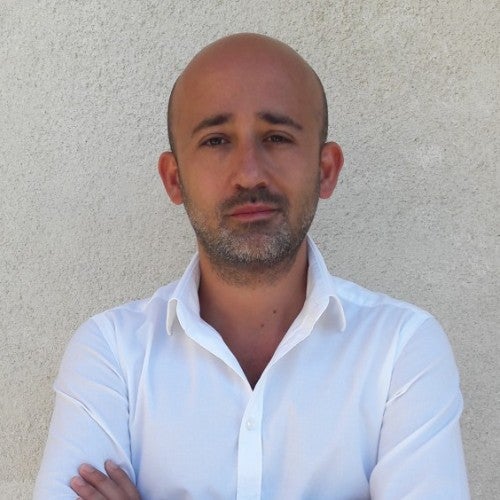
“In both motorsport and mass automotive, competition is intense. And in the current automotive landscape, we know margins have to be protected fiercely. Small manufacturing errors can have big consequences for automakers, and that’s why we’re supporting our customers with solutions that embed quality digitally into every process. By connecting the entire value chain with data, Hexagon’s precision technology gives you the tools to build a competitive, sustainable, and resilient business.”
– Ignazio Dentici, Vice President, Global Automotive at Hexagon
Company Profile
Hexagon is a global leader in precision manufacturing solutions that touch 90% of all cars manufactured globally, empowering the automotive industry to deliver consistent quality at speed with advanced measurement hardware, software, and expertise. With nearly 20 years as the innovation partner for Oracle Red Bull Racing, Hexagon has played a pivotal role in supporting the team’s multiple F1 Constructors’ and Drivers’ Championships through market-leading metrology, 3D scanning, and data analytics technologies.
Hexagon’s solutions enable automotive manufacturers to manage rapid design changes, ensure regulatory compliance, and achieve first-time-right production, even under the most demanding timelines. Trusted by both leading OEMs and regulatory bodies like the FIA, Hexagon’s technologies drive digital transformation, reduce faults, and accelerate development cycles. As the industry evolves toward electrification and sustainability, Hexagon remains committed to delivering the precision, agility, and innovation that automotive manufacturers need to stay competitive and future-ready.
Links