At present, Battery Electric Vehicle (BEV) battery packs are made of singular cells comprised of an anode, cathode, a separator and an electrolyte. These are contained in either a pouch, a prismatic metal container, or a cylindrical metal container. They are connected through a mixture of in series and in parallel configurations, in either a module or, in more recent cases, directly into the battery housing, known as cell-to-pack (CTP), or directly to the body, known as cell-to-body (CTB).
Moving away from modules offers considerably higher packing density, and therefore higher energy density. The caveat of this is a reduction of serviceability; however, regardless of how these cells are packed, inefficiency is always present as a result of the space between the cells (especially affecting cylindrical cells) and the housings surrounding the internal components of the cells. A way of increasing the packing efficiency would be to remove the housings entirely and hence enter the realms of electrode-to-pack (ETP) batteries.
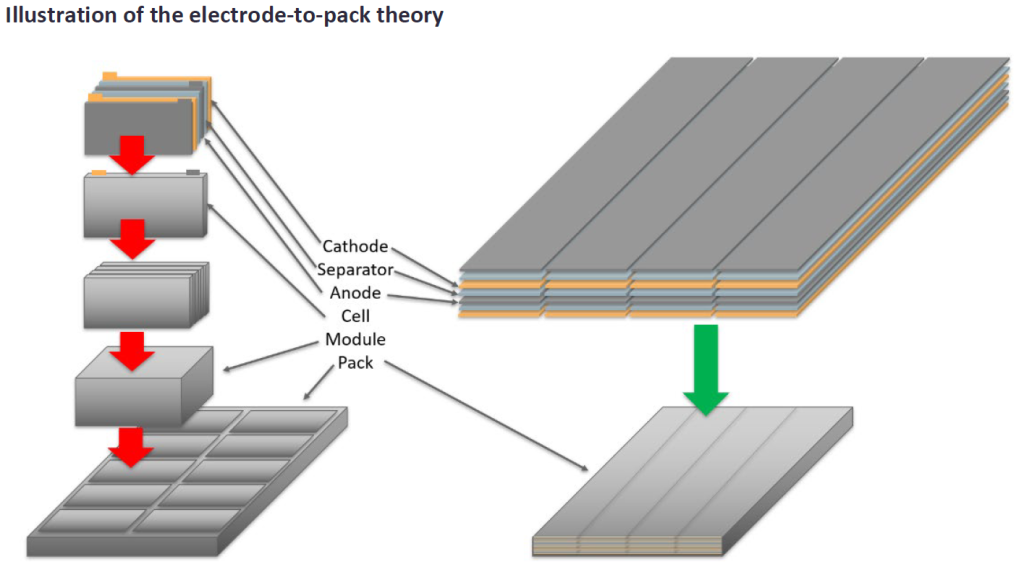
In theory, an ETP battery could offer the highest utilization of useful component space, as the core of the battery minimizes the space and weight devoted to non-battery materials, such as structural parts and conductive connectors, allowing for a more compact and lightweight battery pack. This would offer a huge advantage over traditional cell batteries.
The battery would need to be very stiff to ensure there is no movement between the cell components, as any motion could potentially result in a short circuit. However, this stiffness does offer the crucial benefit of providing a structural element in the vehicle.
There are several drawbacks to this technology, with manufacturability being the most notable. Layering anodes, cathodes, and separators directly into a large housing requires exceptionally high tolerancing. There are several ways in which this could be done: the illustration shows a parallel layer technique, but it is also possible to have layers that spread the entire width of the pack, or layers rolled and fitted into individual honeycomb sections in the housing. The layers would need to be contained in such a way that swelling between the electrodes is reduced, otherwise separation in the layers could occur, resulting in failure.
See Also:
In terms of robustness, cells need to function in a wide array of climates. With large temperature deltas throughout the year, the pack would need to account for shrinkage and growth. Cooling may be simpler – a plate cooler on either side of the pack may suffice, or the reduction in housing may offer a thermal conductivity benefit that could negate the need for high performance cooling. This would mean that only a cold plate to reduce temperatures from a high ambient may be sufficient.
How well do you really know your competitors?
Access the most comprehensive Company Profiles on the market, powered by GlobalData. Save hours of research. Gain competitive edge.
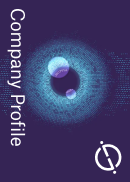
Thank you!
Your download email will arrive shortly
Not ready to buy yet? Download a free sample
We are confident about the unique quality of our Company Profiles. However, we want you to make the most beneficial decision for your business, so we offer a free sample that you can download by submitting the below form
By GlobalDataThis technology is likely a long way away from production, and perhaps a key enabler to this technology is solid-state or semi-solid-state cells. But if it is achievable, the potential benefits could increase packing efficiency beyond today’s realms, enabling smaller battery pack volumes and lower weight, and fundamentally a cheaper-to-produce vehicle.
Oli Petschenyk, Powertrain Analyst, GlobalData
This article was first published on GlobalData’s dedicated research platform, the Automotive Intelligence Center