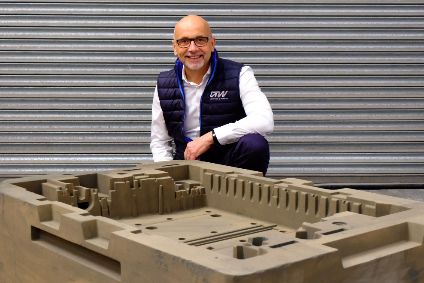
As vehicles are developed to meet the low emissions targets set around the world, it isn't just design and functionality which are being stretched: the materials that components are made from are under increasing pressure to perform. We spoke to Keith Denholm, engineering director at Grainger & Worrall (GW) to see how the industry is meeting the challenges posed by electrification, vehicle light-weighting and down-sizing. GW is a specialist in sand casting and metal technology, including metal additive manufacturing. In this interview, we learn more about the challenges of casting EV and hybrid components, such as electric drive units, where integration of several diverse systems leads to complex castings which need to withstand significant torque forces.
What is the biggest challenge faced by materials in the automotive sector?
We see three key ongoing challenges for materials selection in the auto industry; weight and recyclability and durability.
Light-weighting has entered the vocabulary in a big way. And for obvious reasons; the lower the mass or inertia of the vehicle, the less energy is needed to make it move. Brakes and suspension can then be downsized, kicking off a virtuous cycle. This is true regardless of the power source or the need to offset the carrying of batteries, for example. Much reliance is made and will continue to be made on metal for structures, chassis and powertrain for mass-produced vehicles – it's strong and versatile, and well understood.
Aluminium is the clear lightweight winner in terms of application and versatility, lending itself to almost all manufacturing processes. Once 'out of the ground', aluminium is extremely recyclable, which is beneficial as the industry moves towards whole-life cost analysis. There can be few other materials which, within seconds in a furnace, can be returned to its raw state. The growing challenge is to retain the metal's intrinsic quality from lifecycle to lifecycle so that its potential for 'primary' reuse is not diminished. Understanding these qualities, and how to ameliorate their losses is a big factor in light-weighting.
A third, less obvious challenge is that downsizing makes huge demands of materials, whose strength and durability are big factors in the success of the strategy. Higher specific power to reduce fuel consumption increases the thermo-mechanical burden on all engine castings, and material choice, accurate casting and thorough quality control are central to the durability of the finished parts.
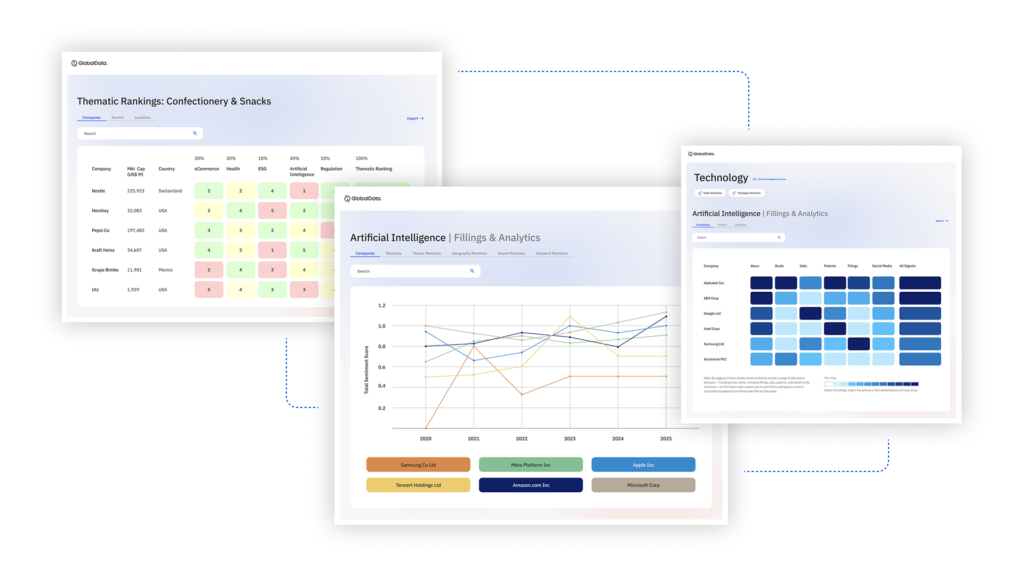
US Tariffs are shifting - will you react or anticipate?
Don’t let policy changes catch you off guard. Stay proactive with real-time data and expert analysis.
By GlobalDataWhat trends have you seen in the materials development process over the last few years?
The ability to cast aluminium into complex shapes makes it a clear winner where component stiffness is needed.
When weighing up the benefits of aluminium versus steel, there is little to choose in specific strength terms. However, the ability to cast aluminium into complex shapes makes it a clear winner where component stiffness is needed. This is driving the shift toward cast underbody structures and sub-frames in a big way. These are large and often very thin-walled castings, pushing the limits of process and material design and for us as a specialist caster/prototyper, this has driven innovation in how we do things.
While prototypes were once approximate shapes built to develop a concept, the prototyping process is now the ideal arena for detailed characterisation of materials and products. For example, unlike billet or sheet metals, castings present heterogenous properties. When combined with powerful simulation software, prototype properties can be tuned to meet functional requirements without over engineering, reducing unnecessary material and weight. Overall, this saves time in the development of products and assists production process selection, which means materials specialists like ourselves are being involved earlier in the design process.
Which direction do you see automotive materials technology heading in the future?
Our view would be that for some time aluminium will prevail as the dominant material in passenger cars, partly because much EV technology is based around skateboard battery housings which are ideal for multi process assemblies. For example, extrusions are being joined to pressings which are joined to castings, all essentially made from the same material. These various techniques require new joining technologies, with welding, riveting and glueing to name but three. At the extreme, Tesla has even toyed with the idea of casting the entire vehicle structure in one-piece. I love this ambition and it goes to show the potential versatility of liquid aluminium, but the need for thinner, more predictable outcomes is a vital consideration.
There are some interesting developments in composites, but manufacturing volumes and recyclability are still challenges to be overcome.
There are some interesting developments in composites, but manufacturing volumes and recyclability are still challenges to be overcome. Beyond automotive, the benefits of ferrous materials and their development should not be overlooked. In some markets, for example, off-highway and commercial vehicle, light-weighting and fuel efficiency remain as challenging as for cars. High strength, high thermal conductivity cast irons are a product group of great interest for us, as are the opportunities to use high strength inserts, possibly additive manufactured, as selective reinforcement in say an aluminium cast component.
We've all read about additive manufacturing, but its adoption has not been as rapid is we might have expected. Can it play a role in the future?
There is a virtue in growing a part rather than removing material from raw stock. This also avoids the need to accommodate tapers and clearances for cutters and forming tools and results in almost any shape being possible. The scope of this technology is wide ranging but the upscaling of it is less compelling. For large parts the time and cost to make things by so-called 'traditional means' cannot be equalled by additive processes where multiple series production is concerned. Furthermore, there are current limitations with applicability to aluminium structures where residual stresses are likely. That said, as a prototyping aid it has much to offer. We have invested in a different type of additive manufacturing where we print sand cores. This permits the tool-less creation of complex shapes which are then cast in the normal way. Castings of over two metres in length containing tens of cores are regularly produced by these means. It allows us to tailor solutions to short lead-time or high complexity without compromise to part function.
Are there technology transfer opportunities into or out of the automotive sector which can be exploited?
The automotive sector is a superb innovator, whether solving technology problems or finding ways to make things effectively. Some aspects of other sectors such as light aircraft, marine and defence are benefitting from these for very good reason – they share a requirement for low weight and high performance, as well as the need to reduce manufacturing cost. These sectors are sufficiently niche to benefit from the capabilities of cast aluminium, where alloys can be tailored for certain conditions and shape castings can replace complex fabrications and the like. As an example, some of the more challenging parts are transmission casings. Multi-speed gearboxes are large, often part of the structural design, and where helicopters or hypercars are concerned, carry considerable loads, all of which stretches the performance of the materials used.