This sliver of land with 10 million people on the Iberian peninsula may be known more in the U.S. for things like wine bottle corks, but there are 45,000 employed by the auto industry. Some of its plants are truly world-class. By Kermit Whitfield Senior Associate Editor.
Portugal’s pre-1983 automotive industry consisted of little more than a few plants doing rudimentary assembly work to satisfy local content laws. But then Renault built an integrated plant for manufacturing vehicles, engines and transmissions that began training a nascent industry on global competitiveness. Officials at Intelli, a government-sponsored think tank that studies and promotes the auto industry in Portugal, view Renault’s investment as the beginning of the modern era of vehicle manufacturing in their country. They also say that many of the best Portuguese suppliers at work today were trained by Renault. However, though Renault provided an anchor for the sector’s growth in the 1980s it has since moved on. The current dominant player is Volkswagen’s AutoEuropa plant, which opened in 1993 and produces fully half of all of the vehicles made in Portugal.
Unfortunately, the plant recently lost in its bid to manufacture the next generation Microbus, so its future is somewhat murky. The Portuguese government hopes to land another big factory to augment-and perhaps succeed-AutoEuropa, but a flat European market could make that a Sisyphean task. Yet the performance I saw during my visit to some facilities certainly indicate that the Portuguese know how to produce a whole lot more than outstanding Port. . . .
Beyond the “Chicken Farm”: Volkswagen AutoEuropa.
In 1991 auto colossi Ford and Volkswagen agreed to join forces to enter the Multi Purpose Vehicle (MPV, or “minivan” to North Americans) segment of the European market. Ford’s job was to build the plant and VW’s to design the product. Things didn’t quite work out as hoped. When the look-alike VW Sharan and the Ford Galaxy launched in 1995, they were dogged with quality problems so pervasive that VW bought Ford out in 1999 and took over the factory. Since then, VW has re-made AutoEuropa in its own image and is now turning out a re-designed product that its executive director, Gerd Heuss calls “the Mercedes of the MPV segment.”
Says Heuss of the incremental approach followed to achieve high quality production: “Our method is not to pursue a 20-year vision, but to implement a lot of small, intelligent steps that have immediate results.” Since he and his team took over in January 2000, lineside inventory – previously as large as three days worth of parts-has been dramatically reduced, and just-in-time deliveries have become the order of the day. “This means that everyone has to be nervous all the time, not just once every three days,” he quips. Not a man to mince words, he likens his first view of the final assembly line under Ford’s management to a “chicken farm,” but a walk through the same area today reveals a clean, open and well-organized operation.
![]() |
As part of a 130-million euro modernization in 2001, Opel’s Azambuja plant built a new state-of-the-art waterborne paint shop that pioneered new application techniques for metallic paint and PVC. |
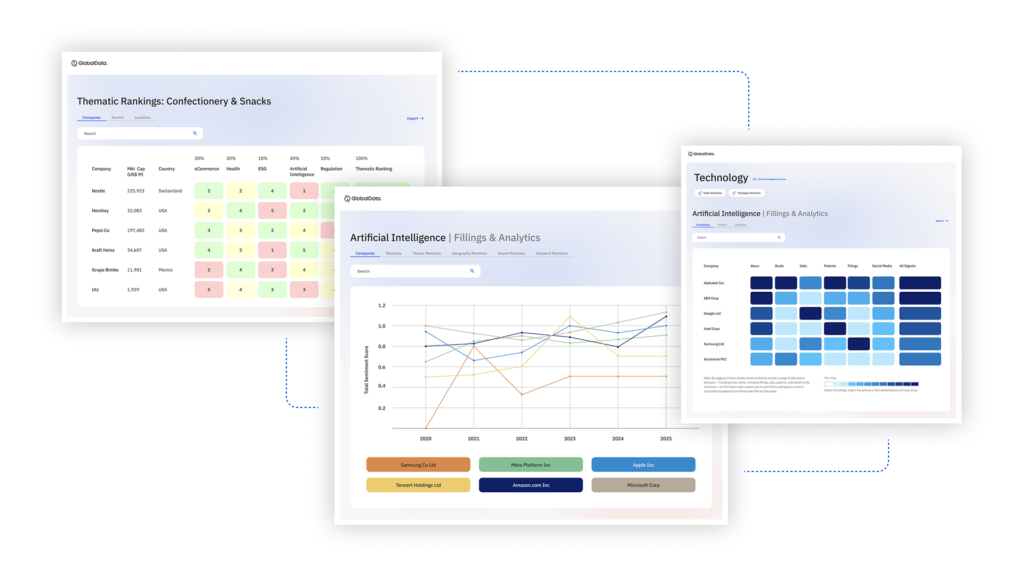
US Tariffs are shifting - will you react or anticipate?
Don’t let policy changes catch you off guard. Stay proactive with real-time data and expert analysis.
By GlobalDataSince AutoEuropa is the only plant that produces the unique MPV platform, it has an on-site staff of 80 product engineers and is able to maintain greater autonomy from Wolfsburg than many other VW plants. It also has its own extensive tool shop where it makes all of the major panel dies for the stamping department. Taken together, these unique capabilities translate into faster design change response. Boasts tool shop manager Mario Rodrigues, “We can introduce an engineering change within one week.” A recent concrete example: the introduction of curtain airbags on the Sharan required a die modification that the design staff and tool shop were able to implement in four days. “Any other facility would have taken longer than that just to move the 40-ton dies from the plant to the off-site tool shop,” he says.
Corsa. . .Combo. . .Cargo: Opel Azambuja
Though he is the managing director of the GM subsidiary Opel Portugal, Martin Apfel’s office sits in a building that used to belong to Ford. In 1963, both Ford and GM began operations in Azambuja, on the outskirts of Lisbon, in buildings that are just 100 ft. apart. Though Apfel jokingly speculates executives must have wanted to carpool together, Ford eventually closed up shop at a time when Opel was ready to expand. And part of the expansion is Apfel’s office.
The Azambuja plant is the sole production facility for the Combo, the kind of small two-box van that is ubiquitous in most of the world, but practically non-existent in North America. The “Cargo” version makes up 65% of production and is targeted at the business market, while the “Tour,” which is fitted with seats in the rear and intended for families, accounts for the remainder. The Combo is built off of Opel’s Corsa platform, but also shares many components with the Astra. Though Azambuja currently builds only the Combo, it has the flexibility to build the Corsa and the Corsa Van if needed.
![]() |
The assembly line at the Azambuja plant was completely |
In 2001, Opel invested 130 million euros to modernize the plant. It tripled the number of welding robots, installed a new conveyor system in assembly and built a waterborne paint shop. The latter made it the first Opel plant in Europe to utilize new application technology for metallic paint and underbody PVC insulation. This update increased the automation rate at Azambuja, but did not change the plant’s overall goal, which is to stay agile by balancing human labor and robotics. Apfel says, “Line speed changes are the order of the day.”
As a full-fledged member of GM’s production network, Azambuja has instituted the Global Manufacturing System (GMS) and works with other production facilities in Europe to standardize best practices and solve individual problems. Apfel says this community atmosphere is a big change from the fiefdoms of the past and gives GM a competitive advantage. “All you have to do is raise your hand and say you need help, and you’re going to get it.” He goes on to say, “I also know the cost details of all of GM’s plants in Europe because there is absolute transparency. There is no sense in playing games (between plants) because we don’t have time.”
Silicon Chips to Cast-Iron Chips: Visteon Palmela
Visteon’s Palmela plant houses what has got to be one of the most unusual operational mixes in the automotive industry. The 500,000-ft2 plant started out assembling electronic components in 1991, but in 1998 it added iron and aluminum machining capabilities and began turning out scroll compressors. Plant manager Sunil Bilolikar says that the ultra-clean mindset necessary for electronics work translated directly to the machining operations helping to make them among the cleanest in the world.
Palmela deals with a lot of complexity, churning out about 300 different products including radios, front and side crash sensors, voice control modules, instrument clusters and air handling assemblies. (These large assemblies are injection molded and assembled on site and shipped just-in-time to AutoEuropa a few kilometers away.) It uses lean manufacturing cells that range from five to 12 people. Each person is trained to do every job in the cell, which gives the plant the flexibility to adjust production based on the number of workers and vice versa. (This capability was effectively illustrated on the day I visited. There was a pan-European protest strike, so some of Palmela’s workers stayed home, but production continued to run at a healthy clip.) Flexibility is further enhanced by simple, effective ideas like lightweight workstations that can be switched out in a few seconds to accommodate product changes.
Palmela was the first plant ever to earn Ford’s “Q1” quality rating after only one inspection. It boasts a sophisticated error-checking system that keeps first time pass-through rates at around 99%. Electronic products are built from the ground up starting with flat, unpopulated circuit boards and not tested until the end of the line, so high quality must be maintained throughout the process. The same is true for the scroll compressors, which have to maintain such precise tolerances that helium is used to test for leaks on the final product because the molecules in the air are too large to detect the smallest defects.